Having analysed storage systems for pallet picking, it is time to examine another type of installation, namely the one used for small sized product.
There are two main problems that can occur with the storage of small or lightweight units. First, there can be a large number of SKUs, i.e. a wide range of units to sort. Second, a high rotation ratio is required in small product storage solutions like the MIniload systems for boxes, etc.
This section will establish the factors that must be taken into account when creating an almost perfect warehouse for small pieces. Such a warehouse will provide sufficient capacity, both now and in the short- and long-term, and the highest possible rotation ratio.
This is achieved most efficiently and rationally through automation. However, when designing a warehouse, above all if this is automated, it must never be forgotten that the cost of the installation must be proportional to the total cost of the operation. In other words, there must be a balance between cost and utility.
To achieve these objectives it is essential to analyse each of the parameters that can be involved, and these are set out in the following sections.
The importance of warehouse storage to the production chain
A warehouse is not a passive element within the production chain of an industry; rather, it is one of the most active and strategic elements. It can be just as or more productive than the assembly or distribution line, since if the warehouse does not operate correctly any such line could be brought to a halt due to a lack of supplies. These supplies can only be properly controlled when the warehouse runs smoothly.
Owing to the above, it is vital that companies that need a warehouse to perform their operations first consider issues such as whether the pieces with the most movement need to be positioned for easier access, whether the most delicate items have been deposited in clean locations, and the degree of safety required, at least for certain products.
Obtaining sufficient capacity for current and future needs
The warehouse is an element of the production chain which must be viewed as a living organism, since any change in demand directly affects it.
When the economy is experiencing rapid growth, for example, the warehouse must become faster, expand its capacity, increase the number of SKUs handled and, as a result, adapt to a reduction in the number of pieces that must be stored initially, and which will rapidly tend to rise.
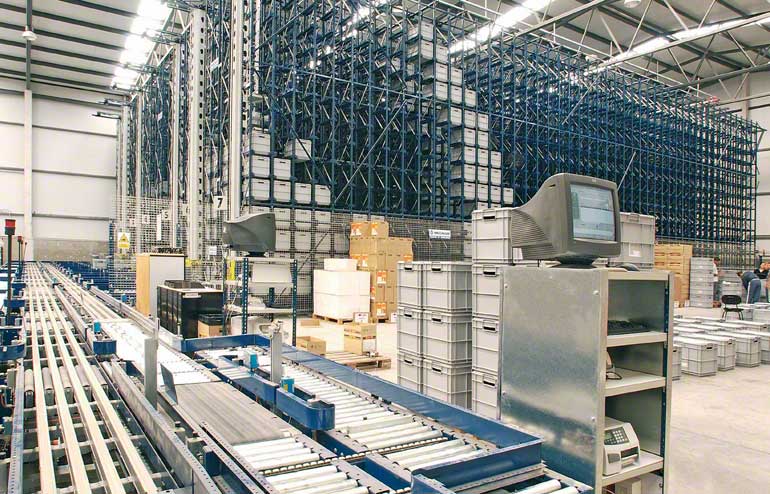
Small parts warehouse installed in a components and assembly company.
These ups and downs must be considered from the earliest stages of the warehouse design process. However, there will be unforeseeable circumstances that may force the designer to use other systems. For this reason, it is vital to know how to adapt to sudden growth once the warehouse is operational. This is the subject of the following section.
How to increase capacity in an existing warehouse
Increasing capacity for the storage of goods can be relatively simple or very complex, depending on the installation. There are two basic strategies for achieving this. One is to redesign the warehouse using more modern techniques. The other is to construct new facilities with a larger capacity.
The first option can be more or less complicated, since not all warehouses can be extended. If they cannot, the only solution is to choose the second option.
There are several alternatives on the market to increase the capacity of an existing warehouse or a new warehouse. First, one could use ultra-compact storage, which focuses on height and very narrow aisles and uses standard, semi-automated, or fully automated handling equipment.
A second option is horizontal carousels, which can even be combined to offer the capacity required and extended in the future. Vertical lift modules, which can also be combined and extended in the future, are another option. Another alternative is to modify part of the existing facility and construct a self-supporting warehouse.
These four solutions should help the planner design the most appropriate warehouse, given the type of product handled in the facility. It is possible that the ideal solution in a specific case is none of these on their own, but rather a combination to offer the almost perfect storage defined at the beginning of this article. However, in making the right choice, bear in mind the second of the factors discussed above; which we analysed below.
How to obtain the highest possible rotation ratio
The rotation ratio measures the frequency with which stored goods leave an installation. To calculate this ratio, the volume of a good consumed is divided by the average stock of that good in the warehouse. For example, if over the year 100 units of a product have been consumed and the average stock of this product during the year was 25 units, the rotation ratio is 4. This is the number of times that this product has been restocked.
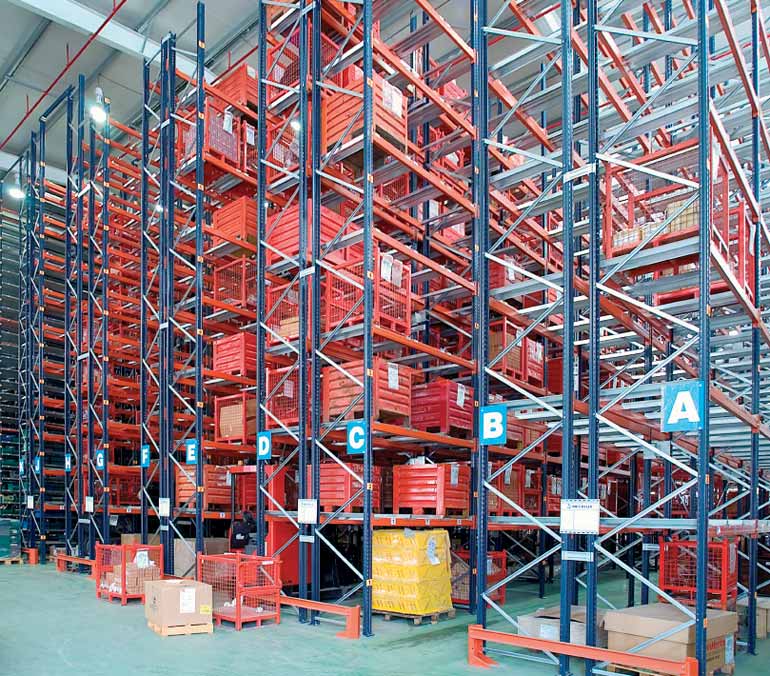
Warehouse installed in an automotive business.
The rotation ratio of a warehouse can vary significantly. Whether or not a rotation ratio is acceptable depends on whether or not it applies to all goods. It is not enough to reach an optimal overall rotation ratio, which in some cases can be 12, in others 20, and in others just 3. If there is a single product with a rotation ratio of, for example, 0.01, this signifies that the installation has a serious error, or at least that something is going on with this SKU, since the company will be storing a large quantity of a product which is not leaving the warehouse, wasting space and reducing efficiency.
It would also be unacceptable to have a situation in which there are high rotation ratios for all low-priced products, but not for more expensive products.
Therefore, having a balanced warehouse is almost more important than a high average rotation ratio.
The effect of streamlining on the storage of small pieces
Any increase in streamlining has a highly positive effect on the total cost of storing small pieces. This factor is improved by using the appropriate equipment for handing and storing materials, as this eliminates downtime and, above all, unnecessary movements.
Streamlining can also be increased through the use of faster and safer channels for the flow of materials. This avoids the use of unsuitable, complicated and tortuous routes that increase the time taken for cycles, with the associated increase in handling costs.
Another issue that influences this factor is the correct planning of the storage element layout within the installation, as this optimises the supply and exit routes. An efficient system to control and administer each and every resource also helps improve efficiency and improves the smoothness of operations at the installation.
A final element that should be considered in this section is the creation of workstations inside the warehouse that have a worker-friendly environment and effective task planning, which makes the installation more efficient.
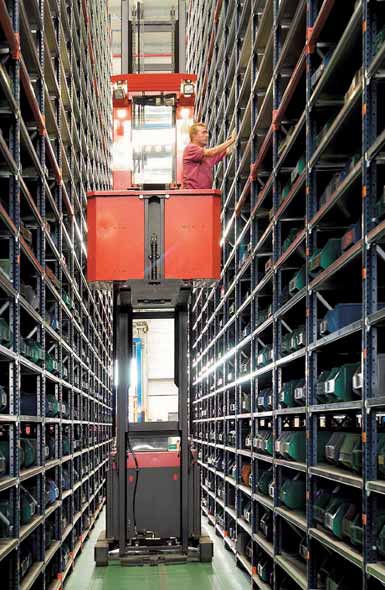
Order picker.
Key principles when creating storage
for small pieces
Once these initial considerations—which are required as a starting point for the analysis of both general and specific objectives and circumstances—have been taken into account, the next step is to analyse the various options available when creating the best possible design for the storage of small pieces.
There are two basic key strategies when planning an installation of this type. One or the other can be used, or both. As already mentioned previously, these are the person-to-goods strategy (in which the operator moves) and the goods-to-person strategy (where the load moves to the operator’s position).
There is no single standard or perfect solution when choosing between these two options. It is even possible for there to be no single best solution, or for the most appropriate solution to be a combination of both. There are many questions related to this issue which are difficult to answer, since these strategies must adapt to each specific product and industry.
The aim and contribution of this article is simply to provide information which is fairly disperse and which changes as new solutions and elements are developed. In this way, even if they do not have much training in the latest storage systems, the reader can have an overview of the options available.
With the essential involvement of specialists, he or she can look at more decision factors when analysing options for its facilities and any improvements that could be made there. Starting this premise, the following is a discussion of the options offered by the specialist industry.
Person-to-goods strategy
The person-to-goods strategy is the most standard, widely-used of current strategies. It has the disadvantage of high handling costs and the fundamental advantage of its low investment costs.
With this option, products are stored on racking units positioned in various ways depending on the system chosen. These elements are handled manually, with the product positioned piece by piece, or mechanized, whereby complete unit loads, generally boxes or containers, are handled.
Units are usually picked manually, with the operator moving on foot or riding onboard a machine to where the SKU required for the order is located.
The systems used for this approach are racking units on one floor, racking units on several floors (through the use of walkways or mezzanines), mobile racking units, narrow-aisle storage, and live pallet racks.
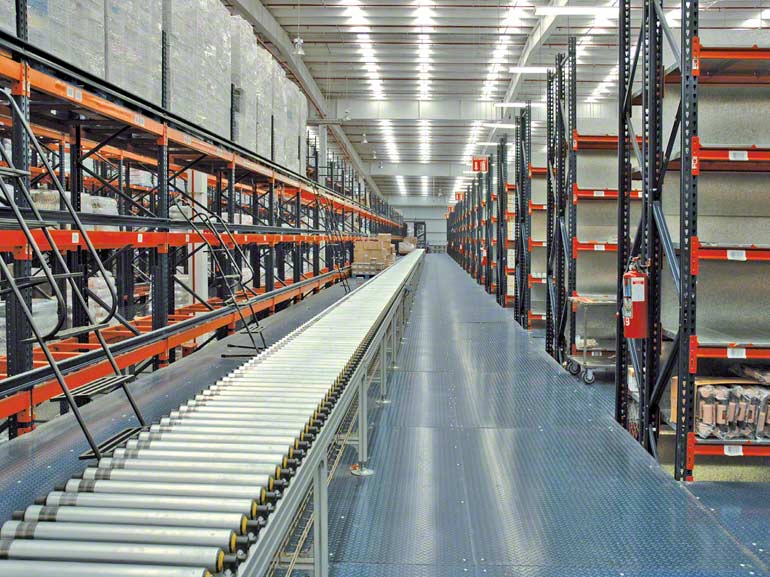
Installation for a chain of self-service shops.
The degree of automation in these systems is very low, and depends on the characteristics of each application. Only the live rack system with pick-to-light devices and the use of shuttles with put-to-light involve a significant degree of automation.
Not all person-to-goods systems are exactly the same. The various options can be classified using a scale of 0 to 10, applying four criteria.
These four criteria are: the total cost of the investment, the cost of handling in terms of labour (handling cost per item, which is independent of the investment), handling capacity in terms of the number of movements per unit of time and, lastly, the area usage index in terms of its effective use.
The following paragraphs go through these solutions one by one and scores them on the basis of these four criteria.
Racking units on a single floor
These racking units, which are generally low-duty, are distributed throughout the warehouse, leaving a small aisle for the operator and the picking trolley.
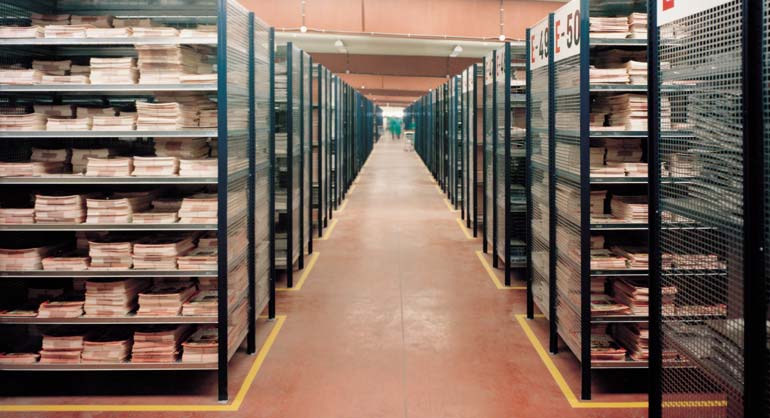
Installation in a publishing warehouse.
There are very sophisticated systems with drawers of different sizes and layouts that are suited to all possible product sizes and industrial activities. Usually, heavier products are stored on the lower levels.
Although these racking units are not usually very high, this feature will depend on the requirements of each industry and each warehouse. It should be remembered that in very tall structures, it can be difficult to rapidly access products stored in the highest positions. At times it may be necessary to use ladders or ladder-trolleys (which are almost always manual), but this slows down the process of picking and dropping off units.
Other mechanised equipment can also be used in warehouses with these systems, such as manual or self-propelled stacker cranes and low and mid-level pickers, as explained in the article "Handling equipment".
Scores for this system:
Criterion | Score | Comments |
Total investment cost |
1 |
Low. |
Handling cost | 8 | High. In general, handling is completely manual. |
Handling capacity | 4 | Average. |
Use of the surface area | 3 | Fairly good, as a result of the narrow aisles. Inefficient use of volume. |
Racking units on several floors
This storage system follows the same principles as the previous one: in practice, it involves two or more one-floor storage areas, installed one on top of another to increase storage capacity or create high racking units with walkways (which has the same effect as having several floors).
With this system there is no need for manual ladders or ladder-trolleys. As a result, the time required to pick and deposit each item is shorter.
In warehouses with this system mechanical devices cannot be used, except on the lower floor or on heavy-duty mezzanines (which are more expensive to install). However, forklifts and other devices, such as lifts or goods lifts, can be used to supply the upper floors with full pallets.
Scores for this system:
Criterion | Score | Comments |
Total investment cost |
1.5 | Slightly above a single-floor warehouse. |
Handling cost | 9 |
Higher than single-floor warehouses. Mechanical devices cannot be used in slotting and picking on upper floors (their use would require a major investment). |
Handling capacity | 3 | Lower than a single-floor warehouse, since it slows down the operation in upper floors as mechanical devices are not used there. |
Use of the surface area |
5 | Surface area use is similar to a one-story warehouse, but it doubles or triples the volume offered by such a warehouse. |
Mobile racking units
The mobile racking unit system saves a great deal of space by reducing the number of aisles, generally to a single aisle. Nonetheless, when racking units are used very frequently or there are a very large number of racking units, these can be designed with more than one aisle, with racking units grouped into several blocks.
Products are placed and picked exclusively by manual means and, given that the distances to be covered are much shorter than when using fixed racking units, the time required to open up the aisle(s) is more than made up for.
With these systems, in which the racking units are hermetically sealed to form blocks, products are stored free of dust. In addition, when the movement is electrically controlled, these blocks of racking units come with a safety system which automatically halts the maneuver if an obstacle is encountered, preventing potential accidents such as a member of personnel being crushed.
Mobile racking units can be controlled by a computer, so that the opening and closing of the aisles is programmed. This system speeds up operations.
Scores for this system:
Criterion | Score | Comments |
Total investment cost | 3.5 | The smaller the facility, the more expensive the investment (in proportion to its capacity). Mobile racking units can be positioned on several levels. |
Handling cost | 8 | The ease of opening and closing the aisle in automated systems reduces the operating time, with the resulting increase in productivity and lower labour costs per item picked or deposited. |
Handling capacity | 4 |
The reduction in operating time means an increase in the number of items deposited and picked per time unit. |
Use of the surface area | 7 |
The much-reduced number of aisles required by these installations considerably increases the area usage index. This can be even greater if the system is installed on several levels, although this also means a considerable increase in investment that is not offset by a positive impact on handling costs and capacity. |
Warehouses with narrow aisles
As part of the category of person-to-goods systems, storage structures with narrow aisles score highest in terms of surface area use, handling capacity, and handling costs. However, the investment cost for this option is higher than for the others, although it is still within acceptable levels.
The surface area occupied is very limited with the layout of very narrow aisles that, depending on the type of load, can be as narrow as 1 metre between loads. Nonetheless, the most common option is to create aisles from 1.5 to 1.7 metres, to be able to use full loads. These systems allow the full height of the warehouse to be used up to the ceiling.
The handling devices used are exclusively mechanical. These devices include turret-type trucks, VNA trucks, high-level pickers, and manual stacker cranes, all of which were explained in the "Handling equipment" article.
With these systems, a high level of streamlining is crucial to maximise capacity. The use of roller conveyors, pallet trucks, forklift trucks, and even auto-guided and laser-guided vehicles (AGV and LGV), which connect the various picking phases in the warehouse, is crucial to achieving this objective.
The correct working position while picking and depositing goods on the shelves is also vital. The operator must be able to move vertically and horizontally between the racking units and perform operations that are ergonomically correct and, therefore, safe and efficient.
There are other essential factors in achieving high productivity levels. These include the incorporation of a good warehouse management system (WMS) and the use of radio frequency devices, which help the operation take place in the proper sequence and, among other things, enable each operator to manage several orders simultaneously.
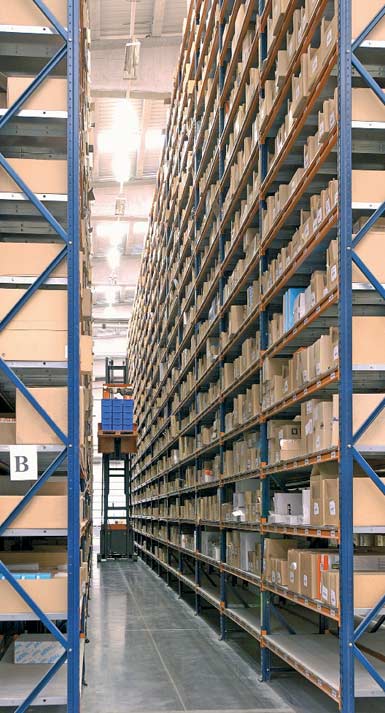
Example of a warehouse with narrow aisles.
Scores for this system:
Criterion | Score | Comments |
Total investment cost | 3 | The investment required is fairly high, but can be worthwhile given the improvement in the other criteria. |
Handling cost | 2 | The labour costs for handling are lower because the entire operation is carried out using mechanical equipment. |
Handling capacity | 5 | The speed of movements obtained with the system means this factor grows spectacularly. |
Use of the surface area | 6 |
This ratio is very high, thanks to the use of very narrow aisles and the entire height of the warehouse. |
Flow racks for picking
In terms of person-to-goods strategies, the picking system for small pieces providing the best performance is the one based on the use of flow racks.
Each box along the picking aisle represents one SKU, with those behind them reserve boxes. The number of aisles required in a warehouse is reduced considerably, as is the distance that the operator has to cover.
Thanks to this minimum space used for aisles, this system makes much better use of the surface area than other types of system.
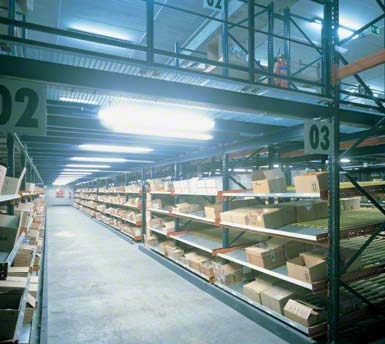
Warehouse for an airport retail company.
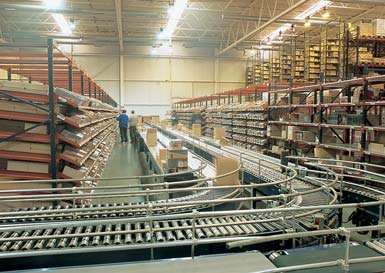
Warehouse for a CD distribution company.
Orders can be prepared in three ways. The simplest is to use a trolley (or a picker) with which the operator moves around the racking units and prepares the order.
The second possibility is to install conveyors on one side of the aisle, adjacent to one of the racking units.
The third option again uses conveyors, but in the centre of the aisle. Here, the emphasis is on the operability of the warehouse at the expense of its capacity. The image above illustrates this third option.
The different structural solutions available allow live picking racking units to be adapted to meet different needs. For example, the higher levels can be used to store pallets with reserve goods, and can even combine live racks for boxes and for pallets. The different options are discussed in more detail in other storage systems articles.
These systems can be improved, considerably increasing the number of operations, with the installation of a pick-to-light system, which indicates from where and in what volume each SKU must be removed. The management system is responsible for managing and controlling these devices.
Carton flow racks for picking are essential when preparing lots of orders with lots of SKUs. If pick-to-light devices are also used, these systems come very close to what is considered automated or goods-to-person picking. In fact, it is common to install these systems along with an automated warehouse for boxes or horizontal carousels when handling consumer goods. In these cases, picking from live racks is managed as part of these automated systems.
Scores for this system:
Criterion | Score | Commentary |
Total cost of investment | 8 | The cost of the investment is average (even though it is an 8, this is offset by the advantages and efficiency it provides). |
Cost of handling | 2 |
The handling cost is very low, given that the efficiency of the personnel is greater with this system. |
Handling capacity | 8 | Very high in environments with a large number of operations, particularly if pick-to-light is used. |
Use of the surface area | 8 |
Very high, due to fewer aisles. Inefficient use of height, except when the space above the flow racks is used for reserve pallets. |
The goods-to-person strategy
This principle, the complete opposite of the person-to-goods principle, involves bringing the units to the operator so that the movement of the operator is reduced to a minimum. This system eliminates the downtime produced when moving from one position to another to deposit or pick goods.
Unlike the systems seen previously, the process for depositing of the product in position and its picking are practically manual, although the movement of the units is almost totally automated.
The storage systems that use this strategy are vertical storage (Clasimat), horizontal carousels (Spinblock), and miniload stacker cranes.
Although some of these systems have already been described in the "Goods-to-person solution" article, they are examined again below from the perspective of the four productivity and efficiency measures used in this article.
Automated warehouse for boxes (miniload)
In essence, the miniload is a compact storage system supplied by a fully automated stacker crane. The units handled by these systems are boxes or containers, which normally measure 600 x 400 mm or 800 x 600 mm and are adapted to the size of the pieces they contain.
This system can also handle trays, instead of boxes, which can be used to house many different very small products at once, forming a mini unit load. In fact, this is where it gets its name: miniload.
This storage option requires very little space and, given that it follows the goods-to-man principle, allows for the creation of ergonomic and very efficient working positions. Miniloads can also be combined so that a single work position can work with several devices at the same time.
This system can handle loads of up to 100 kg per unit (box, container, or tray) and reach lifting speeds of up to 90 m/min. It can also reach good horizontal movement speeds (up to 250 m/min.).
One of the most important advantages of these systems is stock control. Normally, items are identified using barcodes read by scanners. The IT system that incorporates the miniload both controls and manages the goods, and operations that need to be carried out.
When it comes to miniloads, one must remember that there are different configurations for this type of automated storage, with different capacities and speeds. As a result, the solution can be adapted to the needs of each company or industry.
Specifically, miniloads are classified as medium, high, or very high performance. Medium performance miniloads are those that can move up to 150 boxes per hour (75 in, 75 out) in a combined cycle (the movement to add one unit is combined with the removal of another unit, or vice versa). As with the pallet stacker cranes, one side of the racking units that houses the load can incorporate inclined live racking levels for picking rotation A products using a parallel aisle, while B and C rotation SKUs are served through the front of the miniload. They can also be fitted with pick-to-light and put-to-light devices to speed up the operation even further.
High performance Miniload stacker cranes can move 150 to 180 boxes per hour in and out in combined cycles. As with medium performance systems, they can include levels of carton flow racks on one side. They are also suitable for installing various conveyor system in the front of the warehouse if this is considered worthwhile. With these systems, it is essential to use pick-to-light and put-to-light devices.
Lastly, very high performance miniloads can handle more than 250 boxes per hour coming in and 250 going out in combined cycles. Generally, with these models the boxes are only supplied through the front of racks and picking positions can be established in an annexed area. In these warehouses, ergonomic resources, very intuitive support systems, and advanced management and control software are essential.
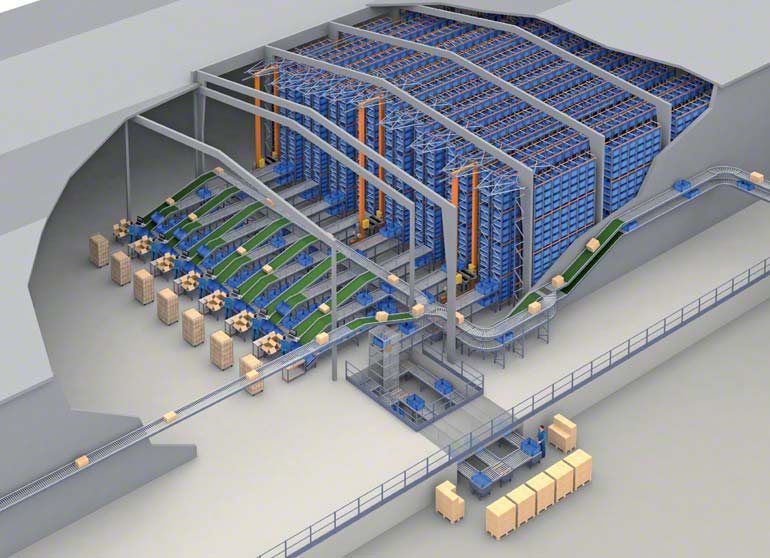
Very high-performance automated warehouse for boxes.
Owing to their characteristics, very high-performance miniloads are a good choice when picking large numbers of boxes in extremely short periods of time. As a result, they can be ideal as temporary storage for picked orders (buffer), storage for supplying assembly and handling positions, or as a sequencer for very quick delivery of sorted boxes.
Scores for this system:
Criterion | Score | Comments |
Total investment cost | 7 | Medium to high. |
Handling cost | 1 | Because it is an almost completely automated system, the influence of the cost of the labour for handling is almost zero. |
Handling capacity | 6 | The handling capacity score is medium-to-high/very high, depending on the model. |
Use of the surface area | 8 | Storage capacity is very high, given the surface area used. It can occupy the full height of the warehouse. |
Although these three systems (vertical lift modules, carousels, and miniloads) are the most widely used, other solutions are constantly appearing on the market. Therefore, it is useful to be aware of the options available at any time and storage installation suppliers must keep up to date with any new developments, so that they can offer their clients the best service and the most suitable options.