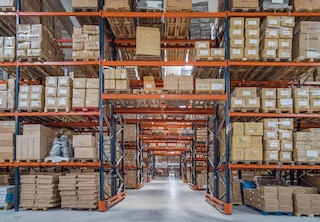
ABC analysis: advantages for warehouse inventory classification
The ABC analysis for classifying inventory enables you to organise the distribution of various goods within your warehouse according to their importance for the business, their value and their turnover. This method prioritises the procurement and placement of products not by volume or quantity, but rather by the economic contribution they make to the company.
The ABC system is based on the Pareto principle or the 80/20 rule, which indicates that 20% of your effort will account for 80% of your results. When applying this to the warehouse ecosystem, 20% of the items generate 80% of the movements in the installation, while 80% of the products create the remaining 20% of movements.
Inventory classification levels with the ABC method
SKUs are classified on three levels:
“A” items
In quantity, these usually occupy 20% of inventory. Nevertheless, they’re the ones with the most turnover and, thus, are of strategic importance. The A SKUs are products in which the business has invested the most money and that generate 80% of its revenue. That’s why it’s crucial to prevent stockouts of these goods.
Also pertaining to this group are products that, because of their characteristics, are critical to the smooth operation of the business. In any case, it’s advisable to maintain tight stock control over A SKUs, with frequent or even perpetual inventories.
As far as the location of A goods in the warehouse, they’re usually placed in the lower areas, with direct and easy access for the operators and close to the shipping docks.
“B” items
These make up the medium turnover range and usually account for 30% of the inventory. As these goods are replenished more slowly, their value and importance count for less than those of A products
In this sense, it’s necessary to pay attention to the trends for B SKUs: they could make the jump to A-turnover products or, conversely, become C goods. Procurement of this type of stock can be carried out according to the minimum/maximum stock level rule, as opposed to maintaining strict control over purchases and issuing orders continuously (which may well be the case with A items).
In the installation, these B products are located in intermediate-height areas. They can’t be accessed as directly as A products, but they’re not the most inaccessible either.
“C” items
As a whole, C products are the most numerous, amounting to 50% of SKUs stored. However, they’re also the least requested by customers.
Since they aren’t strategic items, the resources allocated to controlling these SKUs can be more modest and their replenishment is often adjusted via safety stock. In any case, it’s a good idea to keep an eye on these goods so they don’t end up as obsolete inventory with zero turnover. When it comes to C products, the big question is: is it worth investing part of your budget in maintaining this kind of stock?
As these items are accessed sporadically, they occupy the highest and least accessible areas in the storage installation, as well as those furthest from the shipping docks.
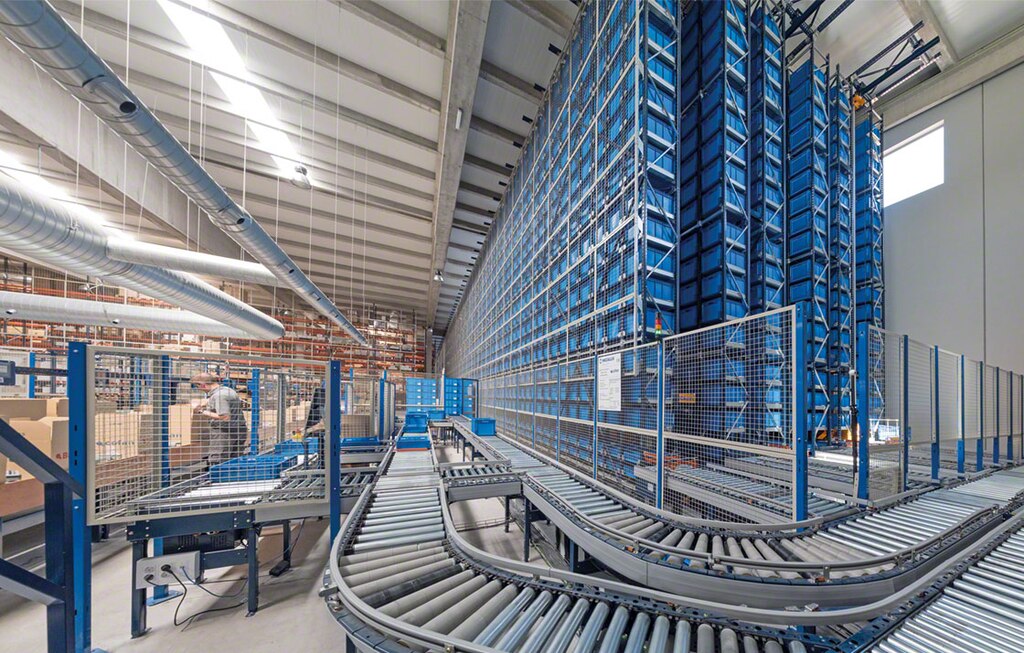
How to classify products using the ABC analysis
There’s no single standard for classifying products into the A, B and C categories. Each company determines this based on the specific way in which it operates and on demand and product characteristics. When examining the theory, we see that there are three main methods of calculating SKU turnover in the inventory:
ABC classification by unit cost
Goods are sorted depending on the level of inventory investment allocated to each of them. That is, the higher the cost of goods, the more the attention paid to procurement management. This focus is useful when storing products of considerably differing value (but not so much when their prices are similar).
ABC classification by total inventory value:
The difference compared to the previous tactic is that this technique takes into account the units of each SKU in the inventory when doing the calculation.
When sorting items according to this method, they often fall between categories. Hence, it’s more difficult to determine the group to which they belong. What’s more, the classification changes constantly, making it necessary to recalculate on a weekly or monthly basis to prevent the system from becoming outdated.
ABC classification by use and value
This is the most widespread method when it comes to warehouse organisation. It uses the demand and value of the goods as a basis for calculation. Compared to the others, this technique goes a step further: although a product might be important for the inventory because of its high value, if it’s not sold frequently, it won’t occupy the space in the storage installation dedicated to A items.
In this vein, it should be noted that, in bringing the ABC method closer to reality, product demand isn’t the only metric to bear in mind. We shouldn’t lose sight of other considerations, such as the profit margin for each product or the impact of stockouts.
The difference between the two methods lies in the criteria used to sort goods. However, the way in which the SKUs are grouped together is based on the same principle. With the data dumped into a table or list, figures are organised in descending order. Products accounting for the top 15% will be A items (in the highest positions). The following 20% will be categorised as B items and the remaining 65% will constitute the C items (these will more or less take up the bottom half of the table).
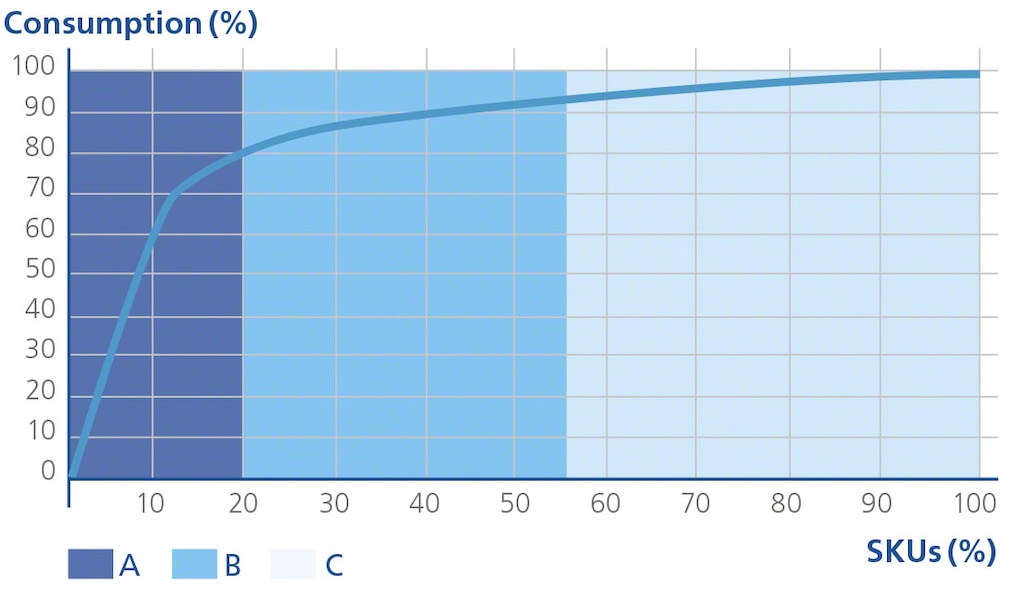
Implementing the ABC method in warehouse organisation
The ABC analysis is one of the cornerstones of warehouse layout design. Here’s how you can make the most of this inventory classification system to organise goods in your installation.
1. Adjust the storage system for each SKU type to leverage space
We have to start with the premise that classification according to the ABC technique is one more parameter to take into account when managing locations. It has to be combined with other key product characteristics, such as hazard level, required storage temperature, volume, size and the like.
So, how does the ABC method relate to storage systems? It’s recommended that you equip your installation with various types of racks. This way, they’ll adjust to the movements made for each product group and optimise available storage space. Standardisation of unit loads on pallets or in boxes helps to make the management of locations in the warehouse more flexible, as it allows them to be reorganised.
For example, it’s common practice to place A SKUs on high-density racks close to the shipping docks or picking area, where there will be a greater number of pallets per SKU in continuous movement. On the other hand, lower-turnover goods will be put on pallet racks, which ensure direct access to the product when required. An example of this redesigning of the layout in accordance with this type of strategy is the installation of Spanish company Marvimundo.
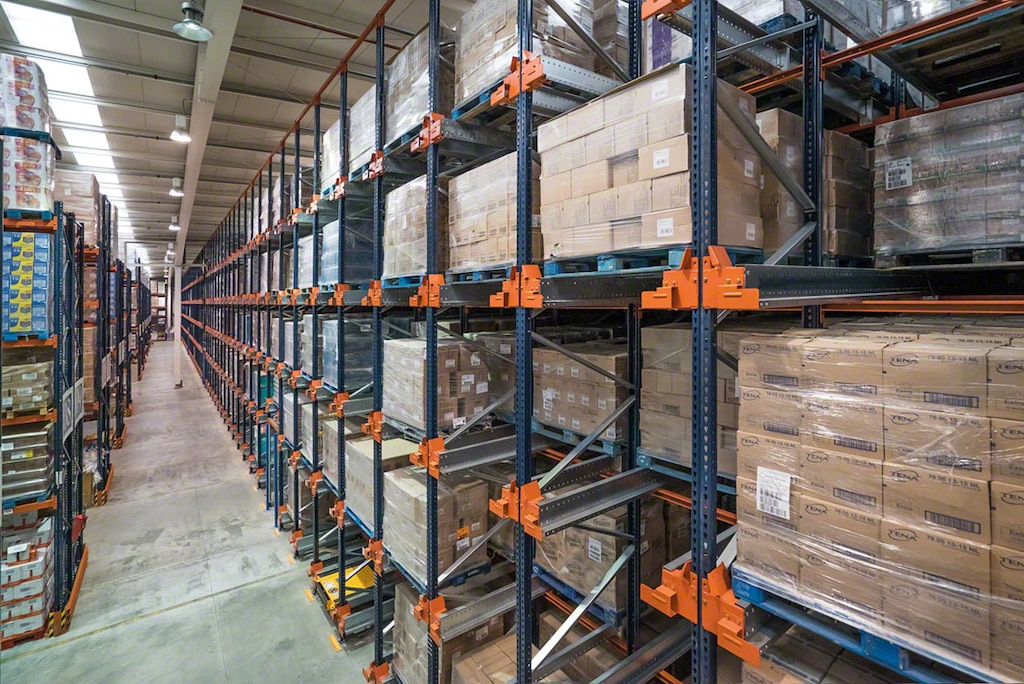
2. Streamline transport between the various areas with automated systems
The ABC method is useful for classifying inventory based on value and SKU rotation. Nevertheless, when the majority of the stock catalog needs to be dispatched within very tight deadlines (as occurs with many warehouses dedicated to e-commerce logistics), it’s vital to provide the installation with the necessary agility to prepare orders on time. How can you do this?
- Automated transport systems such as roller conveyors make it possible to speed up goods movements, limiting the number of picking maneuvers made and reducing time spent on travel.
- Motorised shuttles such as the Pallet Shuttle facilitate the extraction of loads in high-density storage systems. This is the case for both the semiautomatic version of the Pallet Shuttle and its fully automated variety used with stacker cranes.
- Proper selection of the picking or order prep method and organisation of the process are fundamental aspects when optimising load extraction routes.
3. Take advantage of a WMS to establish location rules based on the ABC analysis
Warehouse management systems enable you to make the most of goods classification via the ABC analysis. This software makes it possible to:
- Configure allocation strategies: their aim is to condense storage space as much as possible, redistributing goods based on their area of turnover or moving them closer to the exit to streamline their dispatch.
- Organise stock replenishment priorities around supplying the storage and picking areas and preventing downtime from occurring in the order prep process.
- Monitor goods movements accurately: stock control is essential for assigning ABC classes to the various products. In the end, classification often varies and it’s common to find items that change category. It’s advisable, therefore, to reorganise them in the warehouse or make changes to the zoning of the layout.
Classifying SKUs according to the ABC method lets you save time and effort in warehousing logistics operations. If you think there’s room for improvement at your installation in this sense, get in touch. We’d be glad to put our extensive experience in the sector at your service.