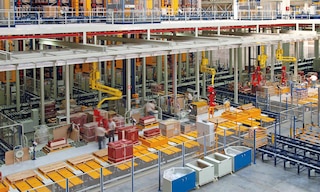
Automated picking for fast deliveries
In automated picking, robotic handling equipment facilitates order picking. Picking is one of the most demanding warehouse operations: its objective is to dispatch goods at minimum cost and in the shortest possible time.
With the help of the latest technologies, order picking can be optimised and accelerated to ensure better service and, consequently, customer satisfaction. There’s a wide range of solutions available on the market to automate picking: from operator-assisted devices to goods-to-person picking systems.
Why automate picking?
New market trends and changing consumer habits are transforming operations in logistics facilities. “New market developments, e-commerce and increased customer expectations have raised the competition for warehouses and manufacturing facilities to handle more orders within tighter delivery times,” says a study by Chalmers University of Technology (Sweden).
Every company’s priority is to meet customer expectations while ensuring fast deliveries. To do so, organisations have had to adapt their storage systems, handling equipment and processes to work more quickly and efficiently. Businesses are turning to automated picking solutions to cut costs, achieve greater accuracy and streamline goods deliveries.
An academic publication by Saarland University (Germany) states: “While order picking systems (OPSs) have traditionally been operated manually, new technologies offer opportunities for reducing the workload of warehouse workers.”
Order picking is one of the most cost-intensive operations in a logistics facility. The study reveals that incorporating the latest fulfilment technology in order picking brings economic benefits. The authors argue that companies should move towards hybrid picking, where technological solutions help operators complete the job to reduce costs and improve ergonomics. Automated handling equipment is capable of higher speeds, accelerating order completion and resulting in fast deliveries to customers.
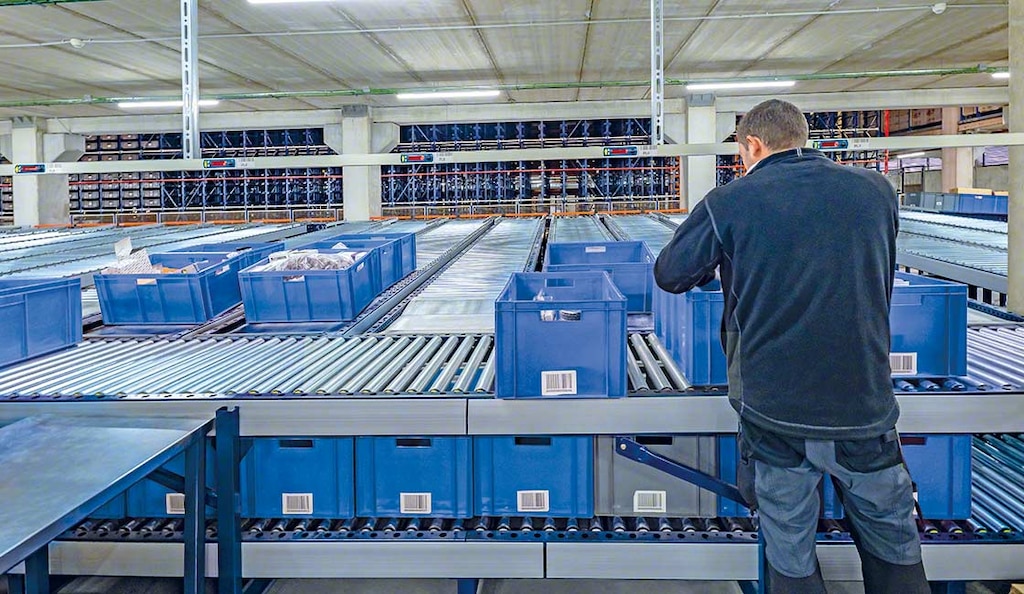
How to automate picking
The first step in automating order picking is to equip operators with assistance devices such as pick-to-light, pick-by-voice or RF scanners. In warehouses where orders are picked on a person-to-goods basis — where operators walk around the facility picking the products — these devices increase the throughput of picking tasks.
Via their assistance equipment, operators receive instructions from the warehouse management system (WMS) on how to prepare orders. This software indicates, for example, the items to be located, their exact location and the quantity to be picked. The advantage of this type of solution is that by following the software commands step by step, the risk of errors is minimised and the warehouse throughput is increased.
Another way to automate picking is to implement the goods-to-person criterion: the products reach the operator directly by means of robotic systems such as conveyors. With this working method, operators don’t have to scour the warehouse to locate the items they need, streamlining the picking and distribution of orders.
To increase throughput in picking operations, companies can opt for automatic storage solutions, such as the Mecalux Shuttle System and set up pick stations. These are workspaces where operators receive goods from the automated storage systems and sort them into orders according to the instructions given by the WMS software. Logistics centres usually have one of these three types of picking stations:
- Traditional. Ideal for sporadic order picking. Operators pick the boxes they receive from the AS/RS and distribute them in the locations behind them.
- Multi-order. Orders are prepared on either side of the operator, who only has to turn 90°.
- High-throughput. This provides immediate and direct access to as many boxes as possible. Thanks to its ergonomic design, it facilitates the picking of up to six simultaneous orders.
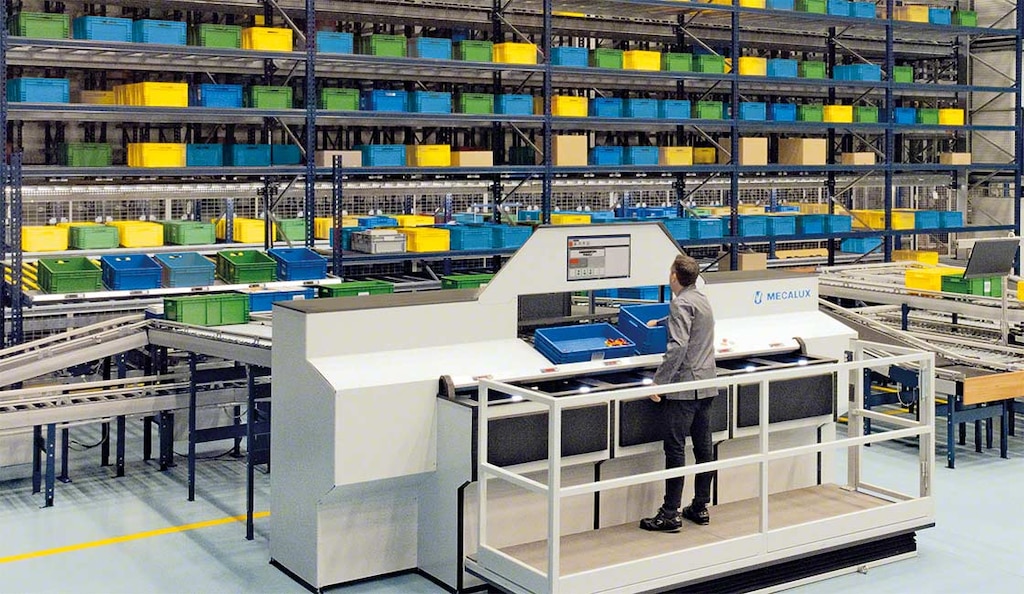
The consolidation of new technologies makes fully automated order picking possible. One of the most modern and advanced solutions to streamline picking are autonomous mobile robots (AMRs). These are devices capable of moving around the warehouse without the need for human guidance.
AMRs can move the goods to the consolidation and packing area, avoiding the need for the operator to leave the pick station. They can also lift the entire rack where the product is located and move it to the operators (these racks are usually small or medium-sized).
Picking robots can also be installed in warehouses to increase productivity, reliability and speed in picking. Industrial robotic arms handle goods at higher speeds and without the fatigue that repetition of movements creates in humans. They can work 24/7, without interruption or human supervision. They also offer great speed and agility in picking tasks. Anthropomorphic arms sort products very quickly and accurately.
Automation makes order picking easier
Automated picking streamlines the sorting and distribution of goods with a single aim: to ensure fast deliveries to customers. In an increasingly demanding market, robotisation can respond to new consumer demands by boosting productivity and eliminating errors and inefficiencies.
To automate picking, companies must equip themselves with automated systems that provide greater reliability and safety when handling goods, as well as warehouse management systems that control inventory and product movements in real time. At Mecalux, we have a long history of designing solutions to modernise order picking. If you are considering maximising productivity in your warehouse, do not hesitate to contact us and we will inform you about several different options for streamlining picking.