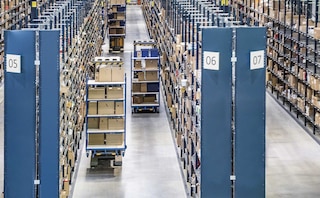
Autonomous mobile robots: warehouse applications and uses
In recent years, autonomous mobile robots (AMRs) have gone from being a futuristic system within reach of just a handful of corporations to a viable, well-established solution in a multitude of warehouse automation projects.
According to LogisticsIQ’s Warehouse Automation Market report, the global market for autonomous mobile robots is expected to exceed 4 billion dollars by 2025, representing a market share of nearly 15% in the warehouse automation sector. What’s behind this expansion? What are the most common mobile robot applications for installations? We’ll analyse this in depth below.
What are autonomous mobile robots?
Autonomous mobile robots, or AMRs, are devices capable of performing tasks and moving around the warehouse without the need for human intervention.
These autonomous robots are equipped with advanced sensors, AI software and a digital layout of the installation, which allows them to interpret their surroundings. Generally, AMRs are charged with moving lightweight unit loads (such as boxes), although there are also those made to handle pallets.
In the storage environment, mobile robots are integrated with a WCS (warehouse control system), which, in turn, is linked to the WMS (warehouse management system). Aided by these software applications, AMRs follow optimal routes when moving goods, identifying and sidestepping any obstacles they come across.
Autonomous mobile robot types: functions
The various kinds of mobile robots are classified by the tasks they fulfil in the installation.
- Mobile robots for picking
The type of picking method used in the facility will determine which tasks AMRs will facilitate:
- AMRs for person-to-product picking: the mobile robot serves as a picking cart, accompanying the operator autonomously. The worker, then, is responsible for selecting the products from the shelves and depositing them in the robot. Once this process has been completed, the mobile robot itself takes the goods to the consolidation and packaging zone. This does away with the need for the operator to leave the picking area.
- AMRs for product-to-person picking: this type of robot can lift the entire shelf (usually small or medium-sized) containing the product and move it to a pick station. This way, the AMR places the shelves so that the operator can prepare orders without having to move. Once the worker has finished, the robot returns the shelf to its place and performs the next task.
Both types of autonomous robots can be equipped with pick to light systems that help employees to select products.
- Mobile robots for sorting
AMRs for sorting have a reclining tray and a barcode reader enabling them to sort packages and place them in the appropriate outgoing line. At the pick station, the operator deposits the packages in the robot, which, in turn, scans the label, processes the information and brings the parcels to the dispatch area.
Another type of robot for sorting is one that operates on mezzanines. It has entry channels for goods coming from an upper level and exit ramps that lead to the dispatch area. Workers place the packages in the robots, which receive the incoming products, sort them and take them to the corresponding exit.
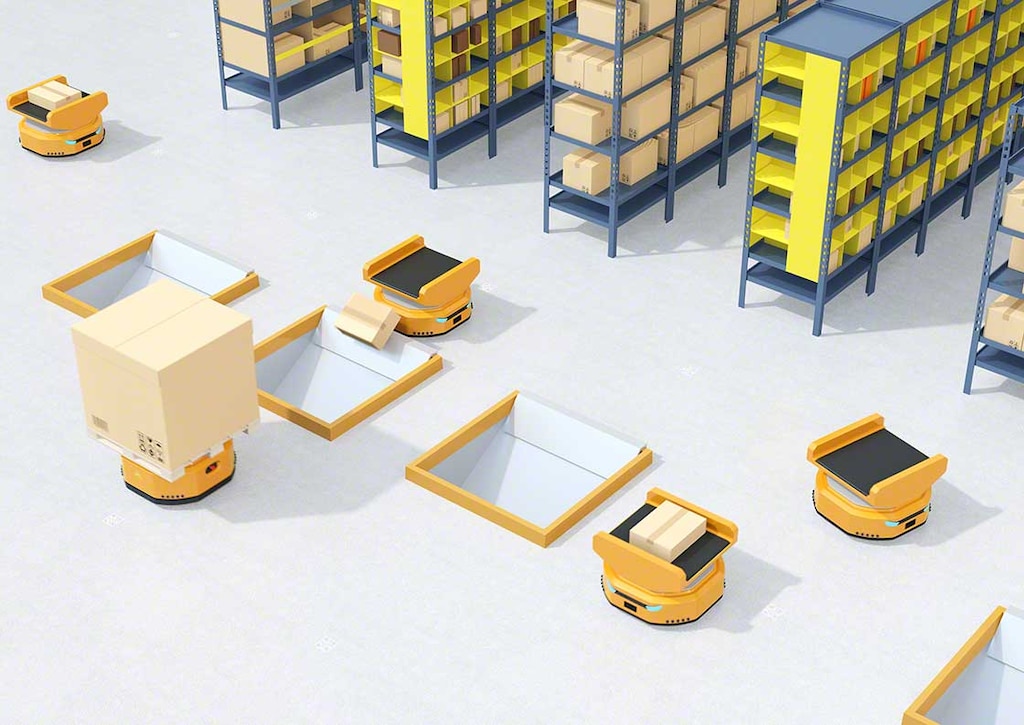
Advantages of AMRs
The three main advantages of mobile robots in the warehouse are:
- Flexibility and fast implementation: as it’s not necessary to predefine the routes these machines need to follow, the deployment phase is significantly shortened. The robot is capable of “making decisions” and adapting to changes based on information in its surroundings through the use of AI and machine learning. For example, it can distinguish between a rack (permanent obstacle) and a forklift (temporary obstacle), acting accordingly.
- Accuracy: advances in navigation technology, robotic vision and sensors are increasing the safety and dexterity of robots when performing tasks.
- Connectivity: mobile robots are integrated with the other systems operating in the installation. This will be reinforced with the progressive implementation of 5G technology. These robots can, thus, perfect their operation and they represent an additional source of data on the logistics operations taking place in the storage facility.
AMRs vs. AGVs
Autonomous mobile robots are most often compared with automated guided vehicle (AGVs), which are well established in warehouses.
The main difference between automated guided vehicles and mobile robots lies in the distinction between an automated and an autonomous system. While AGVs move along a predefined path that they detect by means of laser- or wire-guided systems, autonomous robots continuously adjust their route, thanks to AI. Load capacity accounts for another marked contrast: autonomous mobile robots usually operate with boxes or lightweight packages, whereas AGVs are normally used with pallets.
As for market trends, the AGV sector saw an overall increase of 6.8% in 2019, according to Research and Markets’ Automated Guided Vehicle Market Analysis. AMRs, however, grew at a rate of over 20%, as stated in a report by consulting firm IDC.
In any case, it’s not that one system wins out over the other, but that they both meet different needs. AGVs, for instance, are extremely efficient when handling heavy loads in installations with stable operations over time (such as facilities related to manufacturing logistics). That’s why this system has successfully penetrated the automotive and food industries, as per the Europe Automated Guided Vehicle (AGV) Market Report by consulting firm Mordor Intelligence.
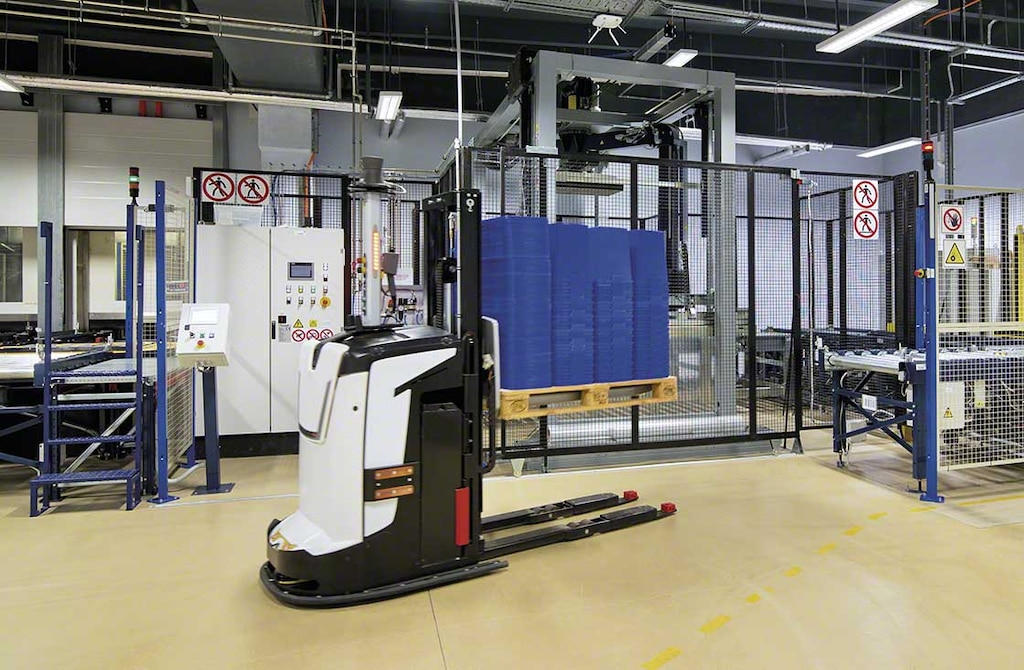
AMR safety and maintenance
In the US, guides for safe operation of mobile robots are the ANSI/ITSDF B56.5-2012 Safety Standard for Driverless, Automatic Guided Industrial Vehicles and Automated Functions of Manned Industrial Vehicles and the ANSI/RIA R15.06-2012 Industrial Robots and Robot Systems – Safety Requirements.
Nevertheless, the ISO (International Organization for Standardization) has created the new ISO 3691-4 standard, a specific international safety standard for this technology, published in 2020.
With respect to maintenance, just as with the rest of the automated systems, it will be necessary to include AMRs in industrial preventive maintenance plans for warehouses. In this sense, in many cases, AMR suppliers will be the ones who resolve incidents that arise or provide specific training to company technicians so that they’ll be able to do so.
Cost of autonomous mobile robots
As new technology on the rise, the cost of mobile robots isn’t less than that of traditional automated systems. Be that as it may, over the past few years, the industrial robotics sector is experiencing a sharp drop in prices due to technology development and economies of scale, based on data from ARK Investment Management.
In any event, as this system doesn’t require major changes to be made to the storage facility, there are various contracting options. It’s possible to purchase the autonomous robots or, alternatively, pay for a license to use them, known as the RaaS (Robotics as a Service) modality. This opens up a whole host of possibilities for businesses when implementing a project with autonomous mobile robots.
Mobile robots in the warehouse: maximum efficiency for lightweight products
So, when is it advisable to use mobile robots in your installation? AMRs have proven to be especially efficient when managing small and varied goods subject to very tight delivery times.
In fact, warehouse management metrics such as the number of picking orders per hour per operator or internal order cycle time (obtained via an LMS) allow you to calculate the productivity required per robot. This ensures that their implementation will be cost-effective for the company.
Material flow increases and pressure on profit margins have made mobile robots a viable logistics automation solution for many installations. All the same, to get a fast ROI with this type of automation, it’s a good idea to analyse in detail current processes and the ability to incorporate these machines into existing workflows.