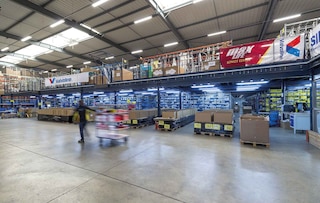
Batch picking: when should I use it in my warehouse?
Batch picking is an order prep method in which various units with the same SKU are picked for different orders. Take this basic example: you’re going to buy groceries for yourself, your brother and a friend, and each of you needs six cartons of milk. So you grab 18 cartons at once, later separating and organising them in your shopping cart.
This is a simple illustration of batch picking applied to supermarket shopping. Now, let’s take a closer look at the scope of this method in warehouse logistics.
Types of batch picking
This technique is based on collecting SKUs in lots, but there are several types of batch picking:
- Traditional batch picking: products extracted are deposited directly into an order-picking machine or roll container. They are then brought to a conditioning area to be sorted by order and consolidated. The advantage of this procedure is that, as no sorting is done in the cart, more goods can be picked in one go.
- Pick-to-cart: as the name itself indicates, carts are manned by operators, who move them down aisles with picking shelves. These pick carts are equipped with plastic crates identified by barcodes that link them to each order. Thus, the operator is already consolidating the orders; that is, each SKU is deposited in its corresponding box, facilitating the subsequent packing process.
- Pick-to-box: this is a variation of the previous method, whereby carts directly carry the parcel or cardboard box to be sent. In this way, three picking tasks are performed simultaneously: collection, consolidation and packaging. This method requires advanced coordination because you have to calculate beforehand the size and type of packaging necessary for shipping each order.
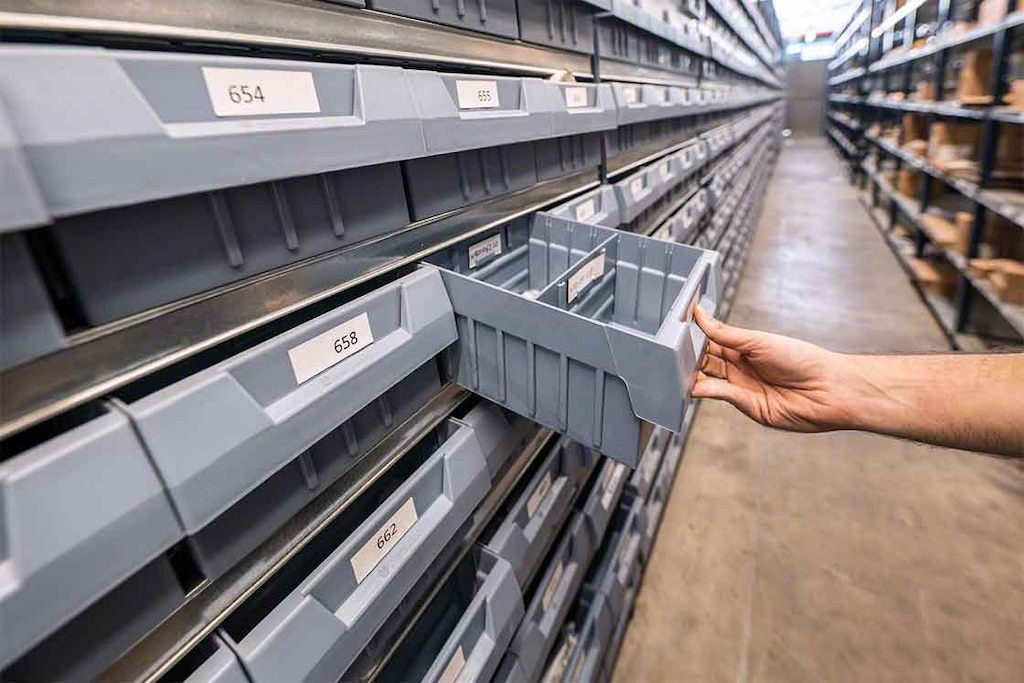
When to implement batch picking in your warehouse
The main advantage of batch picking is that it saves time by reducing operator travel distances. If there are 10 orders with the same SKU, the whole lot can be picked in a single run, without having to repeat the same trip 10 times.
For this to happen, though, the sequence of tasks has to be fine-tuned. Therefore, the warehouse layout, SKU locations and batch configurations have to be organised in a way that optimises operator movements up and down the aisles. This also enables employees to work without getting in each other’s way.
In this respect, warehouse management software is extremely helpful, as it allows you to set up batch picking operations while taking into account such variables as:
- SKU size: picking packs of cards is not the same as picking comforters.
- SKU location within the warehouse layout: to reduce movements as much as possible.
- The number of operators performing picking at the same time: to prevent interference between operators or excess traffic in the aisles.
- Order shipment priority: the WMS controls the travel, consolidation and packaging times so that orders are ready at the right time.
Batch picking is especially recommended when:
- The products stored can be easily handled and are similar in size. For example, when preparing jewelry orders, a hundred SKUs can easily fit in a single pick cart.
- There are many single-SKU orders. In this case, the order would be completed very quickly, since it wouldn’t be necessary to wait for more goods to be picked.
However, you might have a situation, even with a WMS, where operator traffic is very high or shoots up during periods of peak logistical activity. When this happens, one way to breathe life into the operations is by deploying wave picking, programming limited intervals dedicated to order prep.
Selection of the picking method is a strategic decision. For this, there’s no better companion than a warehouse management system such as Easy WMS: it facilitates data recording to optimise the entire operation and test changes to picking formulas, including batch picking. Don’t hesitate to contact us: we’ll show you the potential of Easy WMS with a personalised demo.