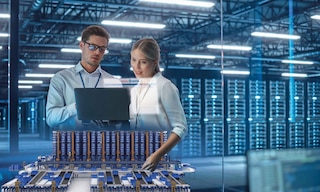
The power of best-of-suite software in the supply chain
Logistics is a critical area for any business. It requires effective coordination between the various stakeholders involved in the supply chain. To optimise operations, companies can equip themselves with digital systems that manage processes such as communication between transport agencies and ecommerce order fulfilment, among others.
What does best-of-suite mean?
Best-of-suite (BoS) software is an end-to-end technological solution that includes preprogrammed modules to perform core business functions. These range from managing human resources and financial assets to supervising logistics operations and internal communication.
Essentially, a single provider is charged with programming and implementing the system. Best-of-suite stands out for its advantages: one provider/contact person, a single product and a multitude of capabilities to address specific needs.
Best-of-suite is a business management software program companies use to streamline information flows between several departments. These types of systems aim to standardise operational processes through specialised modules. ERP software comes preprogrammed for the most common vital business areas.
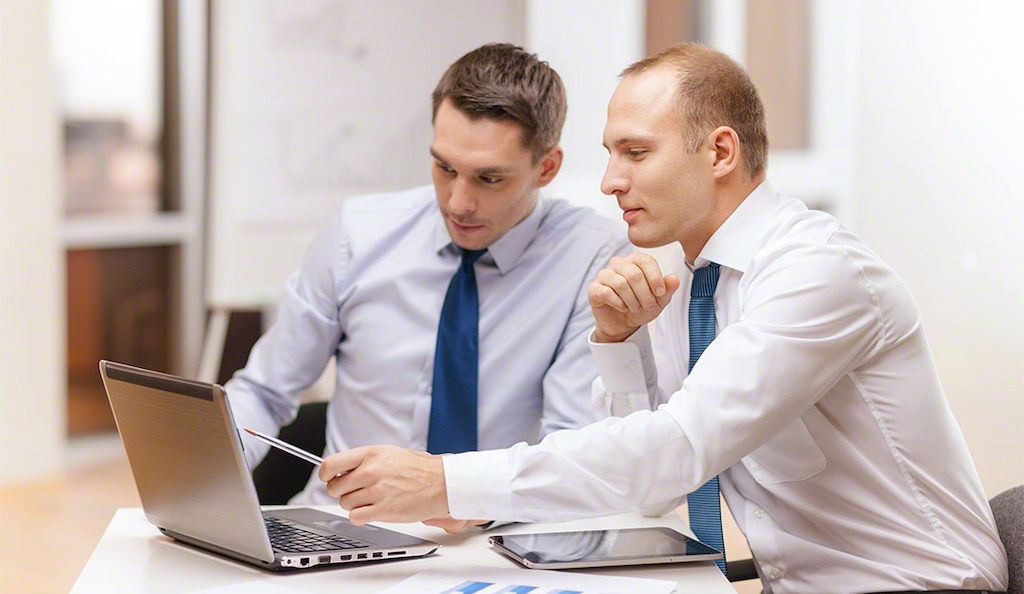
Differences between best-of-breed and best-of-suite
The best-of-suite approach is often compared to best-of-breed, a specialised system specifically focused on the execution of a particular process, such as warehouse operations management.
These are the differences between best-of-suite and best-of-breed solutions:
Best-of-suite | Best-of-breed | |
---|---|---|
Definition | Comprehensive solution for managing all of a company’s operations. | Specialised software programs tailored to each business area. |
Advantages | Implementation and administration with a single provider. | System specifically designed to maximise performance in particular areas. |
Disadvantages | Less flexible. The solutions incorporated for each area may be less advanced. | The software requires integration with the digital solutions used to manage other processes. |
Example | Enterprise resource planning (ERP) software. | Warehouse management system (WMS). |
Users | Organisations seeking consistent management across various departments (e.g., human resources, finance, logistics and sales). | Companies aiming to optimise warehouse processes and automate inventory management. |
Best-of-breed and best-of-suite: a win-win situation
What if you could install a best-of-breed solution for your warehouse with a single provider — as with best-of-suite — but with capabilities for performing additional functions? The good news is this is possible, thanks to a strategic combination of best-of-suite and best-of-breed approaches.
For example, Mecalux’s Easy WMS is a best-of-breed system crafted specifically to optimise logistics operations. But at the same time, it’s a holistic solution — i.e., best-of-suite — designed to enhance the supply chain. Moreover, a single provider — Mecalux, in this case — can implement this solution in all types of warehouses and activate additional modules to perform other actions. These range from connecting logistics processes with production (WMS for Manufacturing) to coordinating inventory needs for online sales platforms (Marketplace Integration).
Digitalising logistics operations with this type of solution provides multiple benefits: greater resilience and responsiveness along with greener, more cost-effective operations. With warehouse management software like Easy WMS, you can manage stock much more efficiently and organise processes rigorously. The result is product flows that enable you to provide the service your customers expect. Additionally, you have a tool that allows you to adapt to changes in your environment, such as seasonality or increased sales.
End-to-end digital solution: the example of Jim Sports
The supply chain of Jim Sports, Spain’s largest sporting goods distributor, stands out for its complexity and high level of demand. Every day, Jim Sports’ warehouse in Palas de Rei (Spain) ships hundreds of orders to more than 3,500 sporting goods stores and facilities in over 35 countries.
To simplify its logistics processes and make order distribution more agile, the company installed Easy WMS in its warehouse. “We decided to partner with the Mecalux Group on this project because it’s a logistics solutions provider with a significant advantage: it can assist us 24 hours a day. Because of the nature of our business, we can’t afford to halt activity in our facility at any time. If an incident were to occur, we’d need a quick solution. This is something that Mecalux has provided us with, which sets it apart from other companies,” says Marta Gontá, Chief Technology Officer (CTO) of Jim Sports.
The organisation chose Easy WMS because it’s a modular solution: its capabilities can be expanded based on business requirements. “We’ve updated the system to align it with our new needs and enhance our performance,” says Gontá. Jim Sports has installed three additional modules to address its new circumstances:
- Slotting for WMS. “With such a high number of SKUs in stock, order is crucial in our warehouse,” says Gontá. This software eliminates errors and boosts efficiency in managing locations: it recommends products be categorised according to sales forecasts or demand analysis. Each item has a defined profile with specifications (relating to size and demand level, for instance), which the software considers when deciding on a location for it.
- Multi-Carrier Shipping Software. This program automates the management of the processes that take place during the last supply chain stage: packing, labelling and shipping. “For example, if an order has at least one bulky product, it will be packed at a specific table. We also have another table reserved for orders that contain fewer than five items, another for those with six to 12 and one more for orders exceeding a dozen. This way of organising work prevents interference with other processes,” says Gontá.
- Client-Specific Rules. This tool makes it possible to customise warehouse processes in line with the particular needs of each client. It also complies with the requirements stipulated, such as maximum pallet height. In the Jim Sports facility, this module creates the documentation to accompany orders (labels and delivery notes) in the language of the delivery destination.
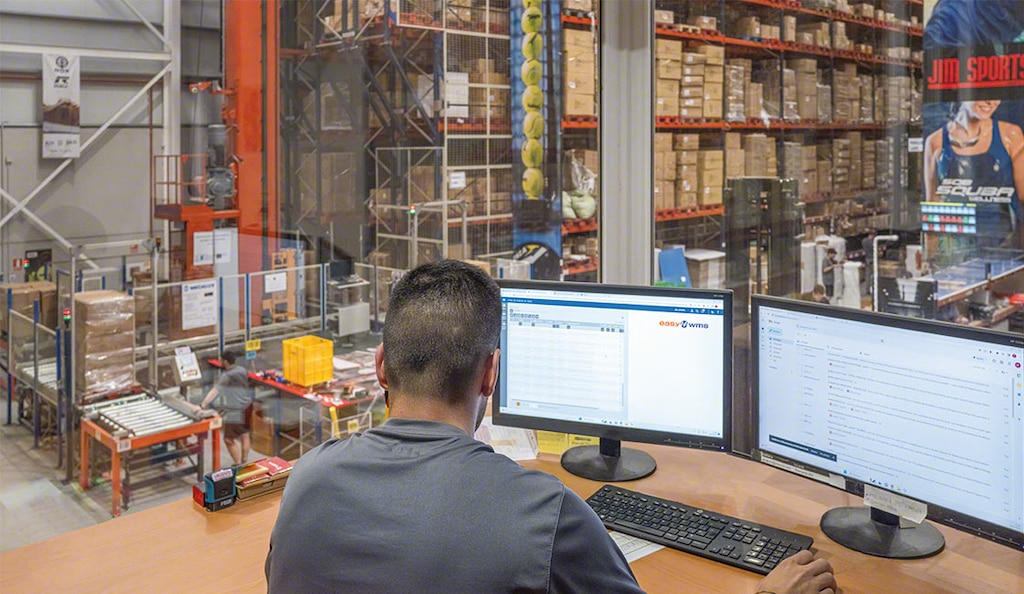
Digitalisation: the best solution for the supply chain
Effective logistics management is essential for the success of any company. And adopting technological solutions could be the key to optimising your operations. The strategic combination of a best-of-suite and best-of-breed solution gives you the whole picture in terms of your supply chain. Digitalising your logistics processes streamlines them significantly in addition to other advantages. These run the gamut from more efficient inventory management to adaptability to changes in your business environment.
Having a single contact when implementing technological solutions makes for a more cohesive integration between systems and more seamless communication. Mecalux’s expertise and specialisation ensure continuous support and comprehensive technical assistance. Be sure to get in touch. We’ll help you in adjusting your company to the dynamic shifts in today’s market.