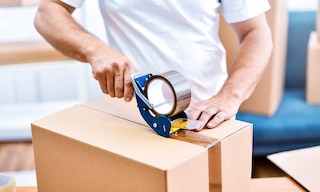
Cartonisation and its benefits for logistics
Cartonisation is the industrial process of packing products in cardboard boxes to protect them during transport and storage. The practice is common in the food, pharmaceutical and consumer goods industries, where merchandise requires packaging that keeps it safe as it moves along the supply chain.
What types of cartonisation exist?
There are several cartonisation methods depending on a company’s post-production logistics processes and the kinds of items being packed:
- Manual cartonisation. Used for small batches or products that are difficult to handle with machines. In this scenario, operators assemble the cartons and place the merchandise inside.
- Semi-automatic cartonisation. Machines form and assemble the boxes, but goods are placed inside manually.
- Automatic cartonisation. The entire process is automated, from carton assembly to product insertion and final sealing. This method is common in large industries that require high-speed and efficient packaging.
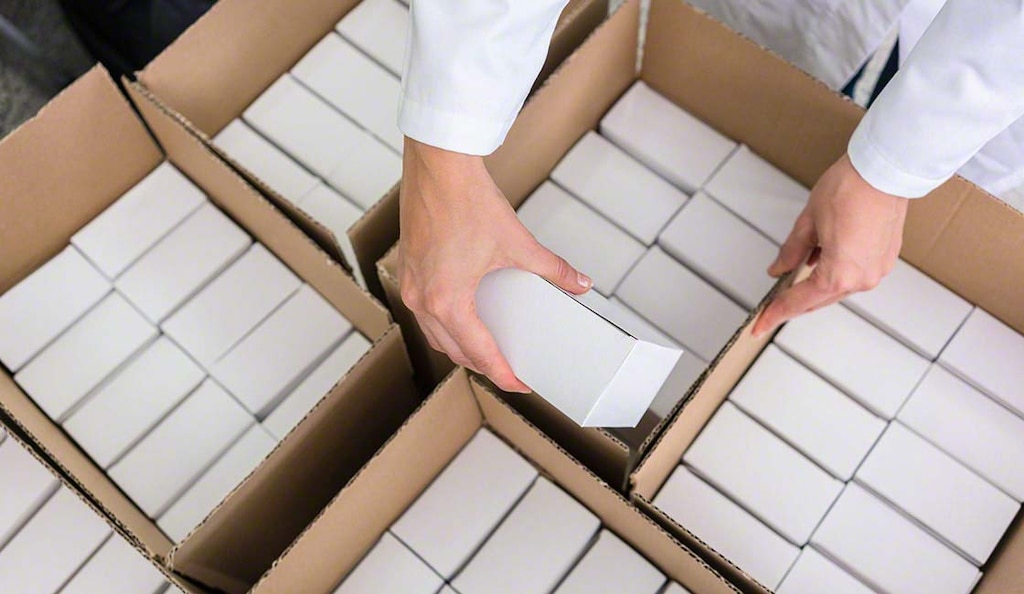
How does cartonisation work?
The cartonisation process typically follows these steps:
- Carton forming. Flat cardboard boxes are unfolded and assembled, remaining open at the top.
- Product insertion. Items are placed inside the box, either manually or automatically. Digitalisation, supported by a warehouse management system like Easy WMS, supports error-free picking.
- Closing and sealing. Boxes are closed and sealed with glue, tape or staples to protect the contents.
- Labelling and sorting. Finally, boxes are labelled for easy identification and organisation in the warehouse or during transport.
Automated systems use sensors and cameras to monitor quality, ensuring that each box is correctly formed, sealed and labelled.
What benefits does cartonisation have?
Cartonisation has numerous advantages for companies and their supply chains:
- Product protection. Cartons shield items from physical damage and unfavourable external conditions (e.g. humidity) during storage and transport.
- Space optimisation. Using appropriately sized boxes cuts down on wasted space, allowing for higher cargo volumes and fewer shipments.
- Reduced transport costs. Maximising transport efficiency lowers fuel expenses. Additionally, optimising space inside boxes minimises the risk of damage, decreasing returns and related costs.
- Easier handling. Packing products in boxes simplifies handling and enables companies to leverage automatic equipment such as conveyors. Robotic systems are ideal for accelerating ecommerce fulfilment.
- Streamlined inventory and picking processes. Packaging items in labelled and barcoded cardboard boxes improves stock tracking and boosts productivity in storage and picking operations. Methods like wave picking speed up order processing by grouping tasks based on zones, timing or priority.
- Improved sustainability. Cardboard is recyclable and biodegradable, making cartonisation an environmentally friendly option. It helps businesses comply with sustainability regulations and best practices.
To sum up, cartonisation boosts operational efficiency, lowers costs and provides environmental benefits. Therefore, it’s critical for supply chain competitiveness.
Examples of companies using cartonisation
Organisations across multiple industries rely on cartonisation to package their goods. Here are some examples:
- Nestlé. One of the world’s largest food companies, Nestlé uses cartonisation to package cereals, chocolates and other food products. Its production plants employ automated cartonisation systems to streamline the process and ensure goods reach consumers in optimal condition. A case in point is Nestlé’s Nescafé Dolce Gusto plant in Girona (Spain), outfitted with Mecalux automated storage and internal transport systems.
- Unilever. The multinational company Unilever, known for its food and consumer goods, uses cartonisation for packaging detergents, food items and personal hygiene products. In its warehouse in Pouso Alegre (Brazil), the retailer stores 83,500 pallets containing a wide range of SKUs.
- IKEA. The Swedish multinational leverages cartonisation to package furniture, home goods, components and accessories. In Malacky, Slovakia, IKEA Components operates an automated warehouse that streamlines the storage of finished products coming from production lines. Cardboard plays a key role in the company’s sustainable and efficient packaging strategy for transporting its merchandise globally.
- Coca-Cola. In the beverage industry, Coca-Cola employs cartonisation to package bottles and cans on its production lines. This allows the business to group multiple units into cardboard boxes for distribution to shops and supermarkets. Coca-Cola Refrescos Bandeirantes employs this method at its facility in Trindade (Goiás, Brazil). There, the retailer manages 14,200 SKUs and fills 3,000 orders daily using Mecalux storage systems.
In addition to its packaging efficiency, cartonisation is an asset due to its versatility and sustainability; as cardboard is recyclable, it helps lessen organisations’ environmental impact.
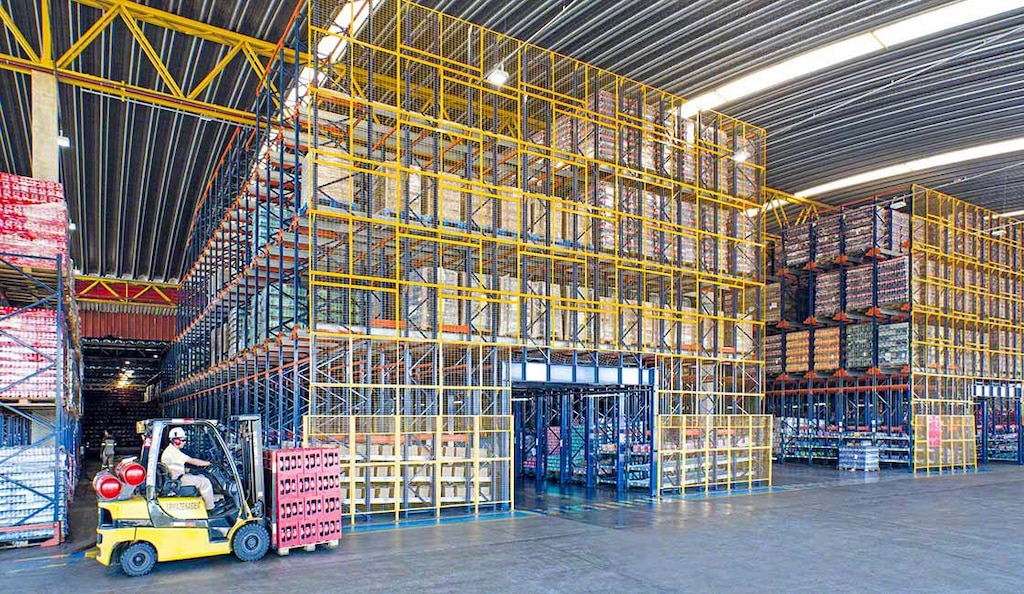
Cartonisation: essential for optimised logistics operations
Cartonisation has become a vital process in modern logistics. It helps optimise space usage, reduce costs and protect products during transport and storage. By adopting efficient packaging strategies, companies can maximise their shipping capacity, minimise the risk of damage, improve sustainability and increase operational productivity.
At Mecalux, we offer a variety of automated storage and internal transport systems capable of managing any type of box, tote or bin. If you’re looking to optimise your logistics processes, be sure to contact us. We’ll provide guidance and support you in implementing the solution best suited to your company’s needs.