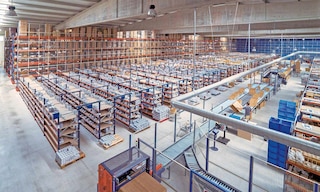
How to organise a warehouse to optimise resources
Focusing on warehouse organisation is crucial for ensuring smooth operations inside your facility.
How to organise a warehouse
Knowing how to organise a warehouse is essential for the success of any business with logistics operations. An orderly warehouse not only helps achieve business goals but also enhances safety, improves workflow efficiency and reduces errors.
The first step to organising a functional facility is designing it. This phase is critical because a poor layout can hinder processes. For this reason, it’s advisable to consult storage experts before renovating an existing warehouse or setting up a new one. Likewise, even the best layout won’t be effective without a well-trained team.
In the early stages of organising a warehouse, you’ll want to consider factors such as market trends, business strategy, sales model, supply chain structure, production requirements, available space and financial resources.
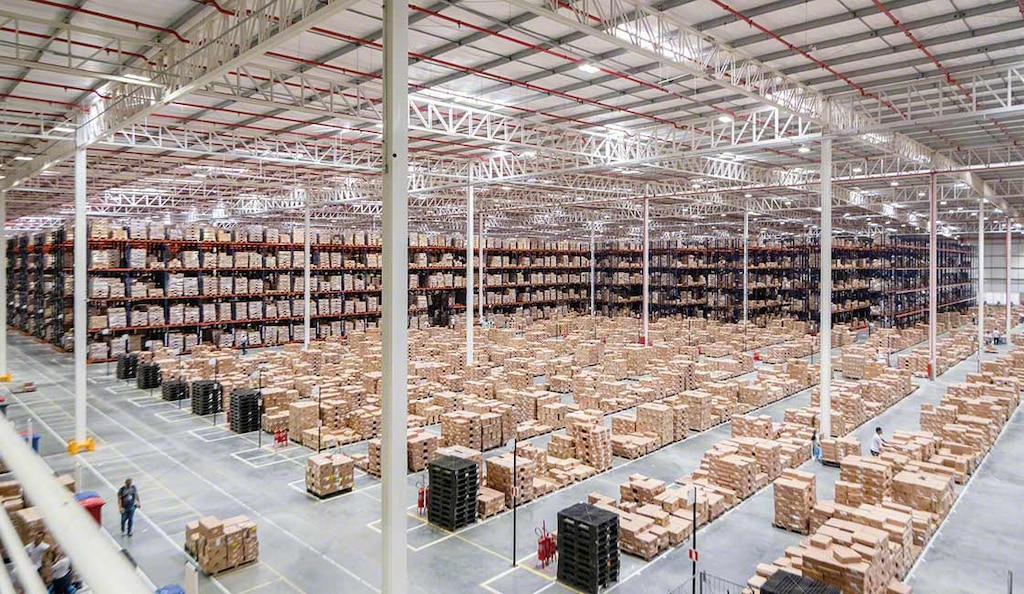
How do you lay out a warehouse efficiently?
Paying attention to the layout of logistics facilities and planning how to organise a warehouse maximises available space, saves time across all processes and optimises costs. Ultimately, it increases company profits.
- Choose the right storage method. There are three ways to determine the management of unit loads, based on a previously conducted functional analysis. In fixed or static slotting, each SKU is assigned a designated location in advance. In random or dynamic slotting — also known as chaotic warehousing — goods are placed in any available space. Lastly, mixed or semi-random slotting combines both approaches.
- Leverage vertical space. Warehouses have limited floor space, so making the most of their full height is key to maximising efficiency. This means opting for high-bay manual racks or, when possible, automated storage and retrieval systems (AS/RSs), which are more effective.
- Anticipate needs. Rather than focusing solely on the short term, logistics managers should plan ahead to keep operations running smoothly and address potential challenges proactively.
- Factor in inventory turnover. Knowing which inventory is in the highest demand at any given time makes it possible to organise a warehouse based on product rotation. Placing top sellers in easily available locations leads to more orders fulfilled.
- Implement cross-docking. When incoming goods go directly to the picking area without being stored on racks, it reduces handling time, storage tasks, delivery lead times and costs.
What happens when a warehouse is untidy?
Failing to manage a warehouse correctly complicates daily operations and can hurt a company’s performance and reputation. These are some common consequences:
- Products are hard to find. If employees don’t memorise locations and the facility isn’t kept organised, locating items becomes difficult. This slows down all processes and can even lead to inventory shrinkage.
- Excess or shortage of inventory. Without an orderly storage system, companies may unknowingly accumulate overstock. Conversely, they may assume certain items are on hand in the warehouse when they’re actually experiencing a stockout.
- You need more space. When products are placed haphazardly and aisles aren’t respected, it’s easy to feel like there isn’t enough room. However, making smart use of available space significantly improves efficiency — which is especially important when organising a small warehouse.
How to keep a tidy warehouse
Facilities that maintain a clean and orderly workspace save time and effort, improving both productivity and safety. One widely used method, originating from Japan, is the 5S system. It ensures organisation through the following steps:
- Sort (seiri). Remove anything unnecessary to free up storage space.
- Set in order (seiton). Equip the warehouse with the right tools to position products strategically and locate them quickly.
- Shine (seiso). Establish a schedule for regular maintenance and cleaning tasks.
- Standardise (seiketsu). Use correct signage to minimise misclassification errors and maintain order.
- Sustain (shitsuke). Turn cleaning routines into habits to prevent excessive dirt and clutter.
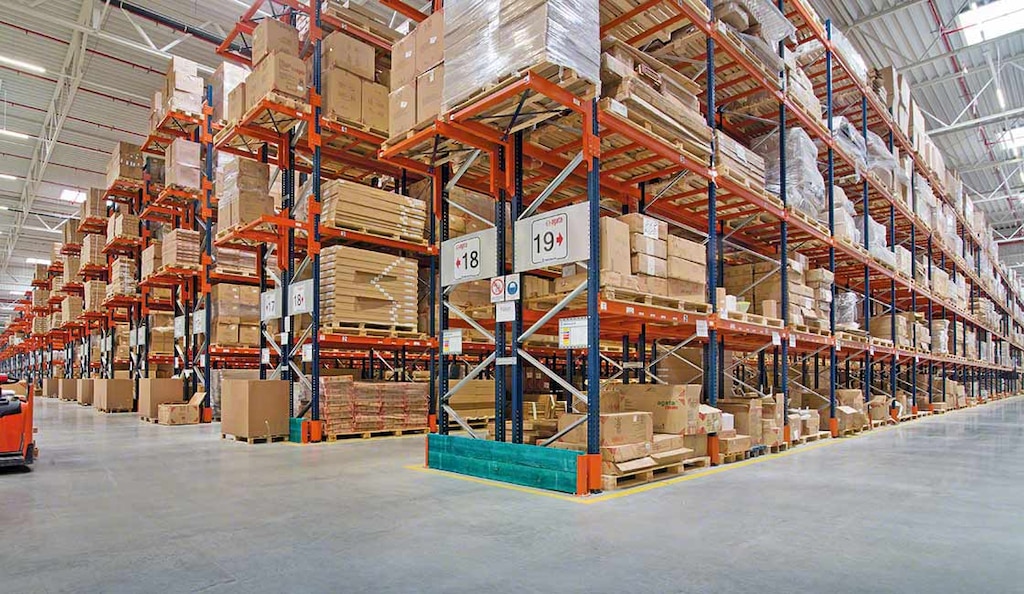
What are the steps to organise a warehouse correctly?
Here are some common issues in logistics facilities and the solutions to overcome them:
Problem | Solution |
---|---|
Long travel distances | Using the ABC analysis to organise warehouse inventory helps position high-turnover goods closer to shipping areas. |
Disruptions | Clearly marking pedestrian and equipment pathways along with designated movement directions avoids interference between teams. |
Manual counting | To maintain precise inventory control and save time, implementing an RFID tagging system is highly beneficial. |
Accumulated returns | Warehouses often overlook allocating space for reverse logistics, leading to piled-up returns. Planning storage areas from the start or reconfiguring existing space can resolve this issue. |
Unclean workspace | Dedicating time each day to warehouse upkeep reduces risks, enhances safety and creates a more pleasant work environment. |
Examples of pallet rack organisation
Although automation can take a company’s performance to the next level, these corporations operate highly efficient warehouses using manual racking systems:
- Leroy Merlin. The French DIY, home decor and gardening company redesigned its business strategy by opening new urban shops in Spanish cities such as Madrid and Barcelona while boosting online sales. To support these projects, Leroy Merlin equipped its two warehouses in Torija (Spain) with selective pallet racking. Standing 10.5m high, they provide a storage capacity for over 21,600 pallets and can accommodate any type of SKU, regardless of weight or volume.
- SMU. The Chilean supermarket’s logistics centre in Pudahuel, near Santiago, spans 70,000 m² and can store approximately 47,000 pallets. This significant retail player in Chile has a long conveyor system and racks with picking performed on the lower levels. These have been reinforced with double-column frames for added security, minimising the effects of potential earthquakes, as this warehouse is located in a seismically active area.
- Radec. Mexican spare car parts importer and distributor Radec, which operates centres in Villahermosa, Tijuana, Monterrey and Guadalajara, has grown rapidly in recent years. However, this expansion led to a lack of space in its facilities. After consulting with Mecalux, Radec installed pallet racking and multi-tier shelving to prepare up to 1,800 pallets a day at its Guadalajara headquarters.
Organise your warehouse with Mecalux
At Mecalux, our storage systems, AS/RSs and WMS solutions drive the operations of all kinds of facilities. We work closely with our clients, tailoring our warehouse management system to their particular needs. If you’re looking to enhance your supply chain, feel free to contact us — we’ll help you optimise your logistics operations.