What is the honeycombing effect in a warehouse?
Honeycombing in a warehouse context consists of a loss of effective storage capacity caused by an excess of empty locations. In practice, these slots can’t be used, since they’re reserved for specific SKUs. This is common in facilities with very rigid location criteria and can also happen with certain compact storage systems. With honeycombing, when a load is removed and there isn’t enough stock of that SKU to fill the empty locations, it’s impossible to store a different SKU in those free slots.
But the good news is there are logistics solutions to mitigate honeycombing in warehouses where this is an issue. We’ll examine them in this post and show you how to implement them in a logistics facility.
What is the honeycombing effect?
Honeycombing in the warehouse refers to an empty storage space that can’t be used. It’s directly related to the loss of effective storage capacity. Honeycombing can crop up in facilities that have static slotting strategies with fixed locations (as opposed to chaotic warehousing) and those with compact storage systems, such as drive in pallet racks. The empty yet unavailable space is considered vertical honeycombing when it appears in height and horizontal honeycombing when it occurs depth-wise.
Let’s take a look at an example with drive-in pallet racks in which the same SKU is stored throughout the height and depth of the storage lane. Honeycombing takes place when one or more of the locations of that lane and the new load to be stored don't belong to that same SKU. The result is a temporary loss of storage space. When faced with this, many warehouses choose to mix SKUs in a single lane even though this makes operations more complex: to access certain pallets, others will have to be moved first.
In warehouses with a fixed slotting strategy, losing a certain amount of storage capacity is often inevitable, and the number of units stored will be less than the overall capacity of the facility. However, even if capacity is lost, the usable space can still be greater than what would be obtained with storage systems with direct access and without honeycombing. That is, under certain conditions, a configuration with honeycombing could be preferable to one without it.
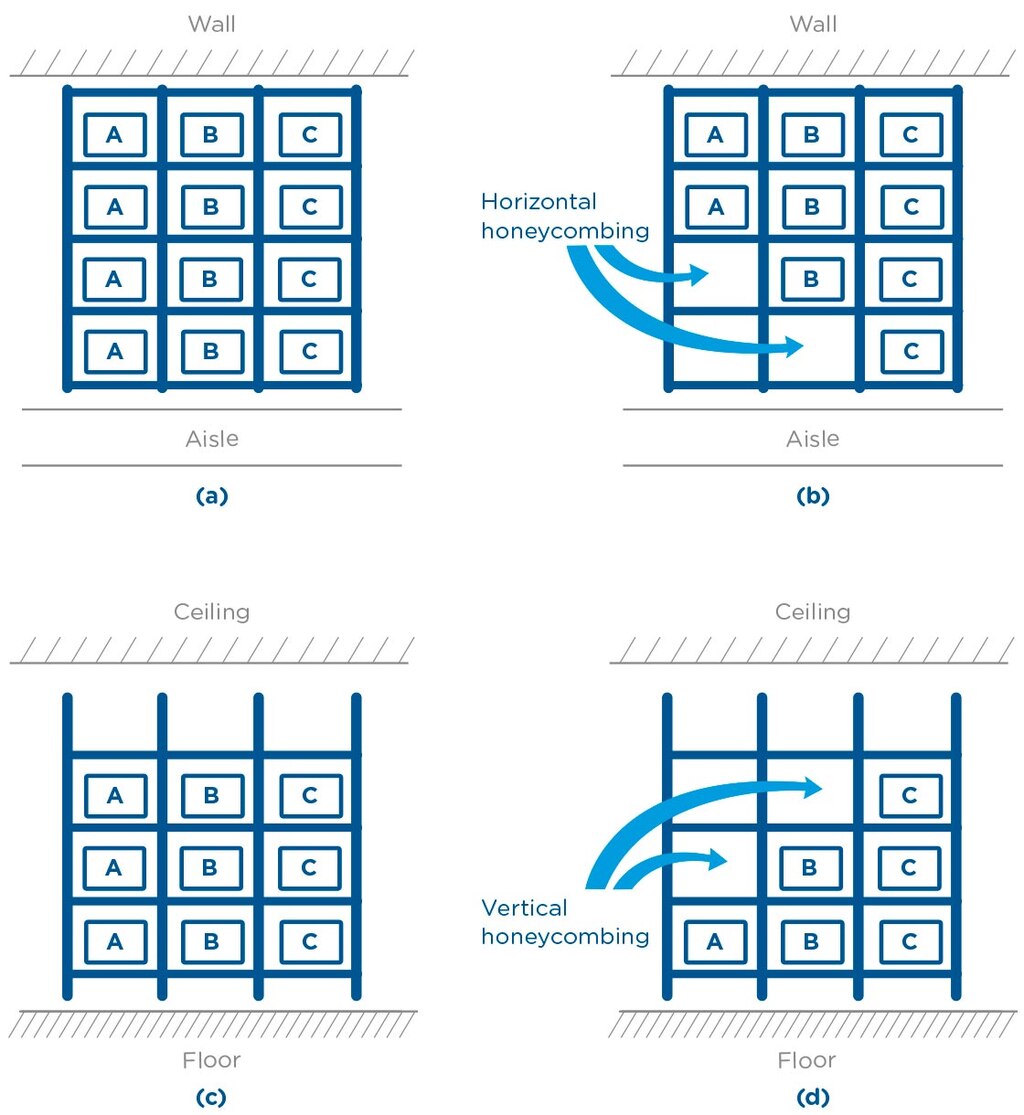
Causes of honeycombing
Honeycombing in warehouses can happen due to multiple reasons, among them:
- Product slotting strategy: honeycombing can be seen in facilities with a static location criterion or norm (specific SKUs stored in fixed locations). This is because it’s unlikely that the goods to be replenished will always match the positions available for each SKU.
- Poor warehouse management: lack of organization in stock management is one of the main causes of honeycombing. This can lead to stock losses that make it impossible to control warehouse slotting, creating empty spaces that aren’t taken advantage of due to lack of knowledge. Honeycombing can also appear when the goods are slotted incorrectly.
- Palletizing errors: mistakes in the palletisation process can involve errors when storing the goods. In fact, when the load overhangs the pallet or is stacked in an irregular way, this can create an empty storage space that can’t be used.
- Channel depth: storage systems with deeper lanes are more at risk of horizontal honeycombing, especially when products are removed in line with the LIFO (last in, first out) method.
How to calculate honeycombing
The loss of effective capacity in warehouses due to honeycombing can be calculated using this formula:
Effective capacity (%) = (cubic space used / total storage capacity) x 100 = (no. occupied locations) / (no. total locations) x 100
This formula indicates the percentage of storage space occupied at a given time compared to the maximum warehouse capacity. To get a more accurate picture of your facility’s efficiency, it’s a good idea to calculate this percentage periodically and then determine the average over a longer period of time. In warehouses with high-density storage, a high level of storage location occupancy tends to be around 85%.
For example, if the building’s maximum capacity is 1.679 m3, and 2.000 m3 of that space are occupied, the warehouse occupancy rate would be 84%. In other words, the resulting difference would constitute a honeycomb loss of 16%.
How to mitigate the honeycomb effect
Honeycombing can result in cost overruns for the warehouse. Although it can’t always be eliminated, there are logistics solutions on the market that lessen its impact considerably.
One way to minimize empty locations is to implement a warehouse management system (WMS). This software enables you to employ a chaotic product slotting strategy, meaning that SKUs won’t have fixed locations established and, in essence, can be stored in any available position. This leverages all spaces on the pallet racks and picking shelves. The WMS ensures total control over stock while automating slotting, taking into account variables such as product turnover.
When you need to store extremely varied goods in a compact way, mobile racking systems are a great option for preventing honeycombing. All the SKUs are perfectly accessible, as the working aisles can be opened and closed. This storage system is configured in such a way that no space is wasted when employing the chaotic storage strategy.
On the other hand, when storing similar goods, drive-in pallet racks are the go-to solution for compacting the goods. Nevertheless, with this system, only one SKU can be stored per lane — both in terms of the depth (horizontally) and levels (vertically) — increasing the risk of honeycombing. One way to avoid this is with the Pallet Shuttle system: a motorized shuttle is positioned inside the storage channels of the compact racking structure to organize the pallets. Forklifts don’t enter the racks, and the SKUs on each storage level can be different, raising the system’s effective capacity.
Two other high-density solutions that also let you store one type of SKU per level are push-back racking systems and pallet flow racks, which are characterized by their use of rollers and the force of gravity.
The solutions above reduce vertical honeycombing. However, it’s still possible for horizontal honeycombing to occur (half-empty channels). So, when designing your warehouse or storage system, another measure would be not to make your channels too deep; this way, you won’t jeopardize your effective capacity.
Honeycombing: the case of SLVA
French milk producer SLVA implemented a 4.000 m2 facility ― with only 2.829 m2 dedicated to storage ― to house over 7,000 pallets. To optimize the storage and retrieval of its goods, Mecalux equipped the warehouse with the Pallet Shuttle system. This way, the company could store different SKUs per bay (one per channel).
SLVA has three blocks of high-density racks of different depths that are divided according to the turnover rate of the products. To reduce honeycombing, these storage systems are outfitted with a motorized shuttle that organizes the channel and prevents the existence of unavailable spaces. The division of storage into blocks helps to mitigate honeycombing by housing goods of different turnover on racks of varying lengths.
For example, in one racking unit, with capacity for 3,792 pallets, the motor-driven shuttle can manage up to 24 unit loads deep, helping to minimize honeycombing. Inventory classification by turnover places low-consumption products on another block of racking that holds only three pallets deep per level.
Keep honeycombing at bay: choose the right storage systems
In a warehouse with manual operations, especially one with compact racks, goods movements create empty spaces. And these temporarily unavailable locations impede you from leveraging the effective capacity of your facility.
To lessen the blow of honeycombing on the warehouse, it’s necessary to consult a trusted intralogistics solutions provider that will design a solution based on your company’s needs. At Mecalux, we'll draw on our 50 years of logistics solutions expertise to maximize the throughput of your warehouse. Get in touch, and we’ll advise you on how to streamline your operations and optimize your effective storage space.