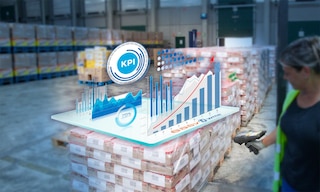
10 inventory KPIs to monitor in your warehouse
Inventory KPIs are key performance indicators that evaluate stock management in the warehouse. Facilities that have identified these metrics can ensure efficient control of inventory and of goods inflows and outflows.
In this post, we analyse the main inventory KPIs to monitor in the warehouse, how to implement them in your company’s logistics operations, and, most importantly, how to leverage them to tighten control over your stock.
What are inventory KPIs?
In the context of inventory management, a KPI (key performance indicator) is a metric that helps to monitor stock, product entries and exits, and the availability of inventory. This information facilitates decision-making to improve logistics planning and stock control based on the warehouse’s real throughput. Proper monitoring of these indicators boosts the productivity and efficiency of the facility.
Inventory KPIs are extracted from the continuous analysis of formulas and numerical results. To facilitate the tasks of the logistics manager, warehouse management is often digitised, converting these data into information. The implementation of a warehouse management system (WMS) automates the entry of data related to all operations taking place in the facility, organising and structuring the information to make it visible and useful for the warehouse manager.
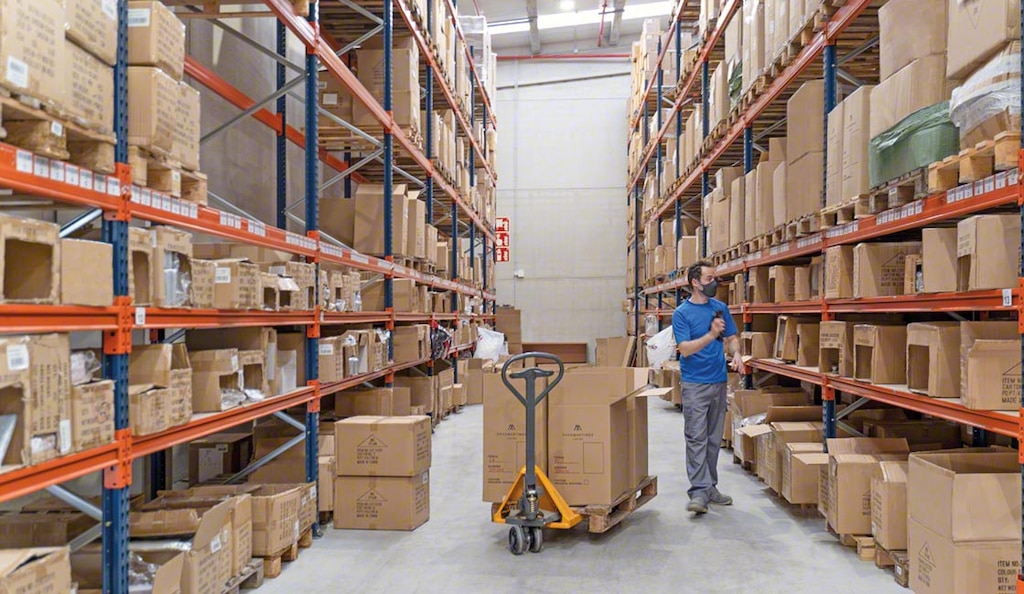
Inventory KPIs: 10 indicators for assessing stock availability
Managing stored goods is one of the most complex logistics operations. Below are 10 inventory KPIs that ensure more efficient stock control and, above all, the availability of goods at all times, making it possible to fulfil your customers’ orders.
1. Average stock
This indicator relates to the average number of SKUs stored in the warehouse over a specific period of time, usually a year. This metric provides the logistics manager with objective information on the average quantity of stock stored in the facility during the selected period.
Average stock = (beginning stock + end stock) / 2
2. Optimal stock level
The optimal stock level is the exact amount of inventory a warehouse needs to meet existing demand without stockouts (in other words, not being able to sell the order due to lack of stock). This KPI shows the warehouse manager the optimal stock quantities for obtaining maximum profitability and minimising storage costs.
Optimal stock level = optimal order quantity + minimum stock + safety stock
3. Inventory shrinkage
Inventory shrinkage indicates the difference between the stock recorded in the inventory program and the actual stock available in the facility. This imbalance could be due to, among other reasons, errors in periodic inventory counts, operational or handling mistakes, or the existence of damaged products.
Inventory shrinkage = (stock you should have - stock you actually have) / stock you should have
4. Average stock loss
This inventory KPI denotes the stock that has been lost or has become obsolete in the warehouse during a particular period of time, usually within a year. Stock losses can occur for many reasons, for example, theft, deterioration of the merchandise, or administrative mistakes. This value informs the manager of the degree of effectiveness of stock management, operator efficiency, and storage conditions in the facility, among other matters.
Stock loss = (quantity not supplied / quantity requested) x 100
5. Days sales of inventory
Days sales of inventory refers to the time the products remain stored until they are dispatched. This calculation, which analyses the storage costs for each item, directly affects the company’s liquidity: the less time inventory remains in the warehouse, the lower the storage cost and, hence, the higher the profitability.
Days sales of inventory = cost of average daily inventory / (cost of goods sold annually / 365)
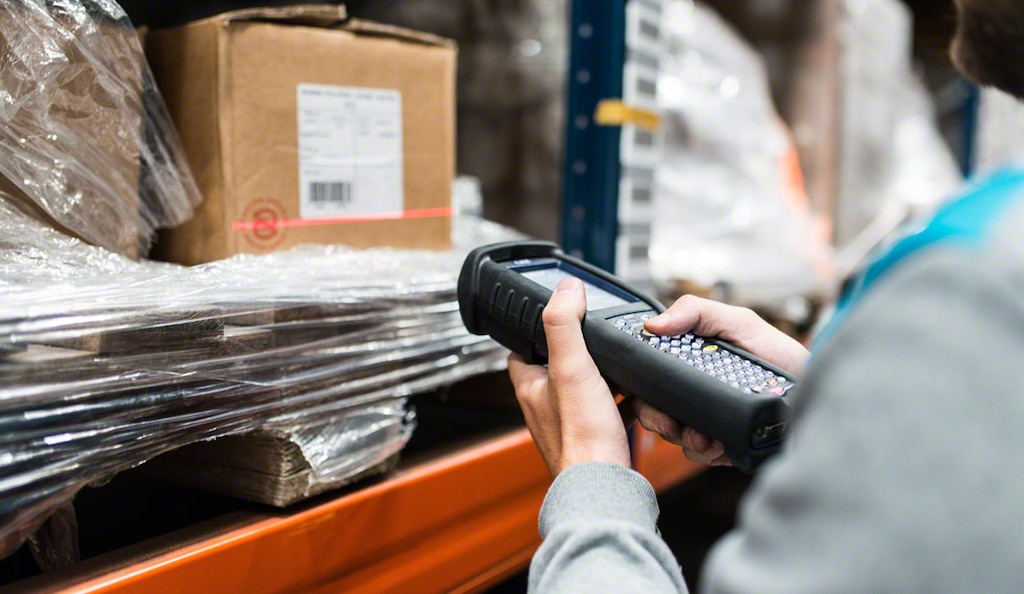
6. Stock turnover rate
Stock turnover, is an inventory KPI that measures the speed at which stock is replenished during a specific period of time. In other words, it shows how many times an item has gone through the entire business process, i.e., the sale, delivery, and payment of the order. This indicator helps the logistics manager to assign a type of inventory according to the ABC analysis, where A items have the highest turnover and C the lowest. With this information, products in the warehouse can be classified more appropriately, based on their demand level.
Stock turnover rate = monetary value of SKUs sold / average stock value
7. Stock return rate
This indicator expresses the percentage of orders returned to the facility after having been sold due to errors in the delivery or picking processes, among other reasons. Reverse logistics accounts for one of the greatest logistics challenges nowadays, particularly because of the standardisation of free ecommerce returns. A high return rate means poor order management and, thus, logistics cost overruns that could jeopardise the company’s competitiveness.
Stock return rate (%) = (No. of items returned / No. of items sold) x 100
8. Sales-through rate (STR)
Also known as the direct selling rate, this metric compares the percentage of inventory sold with the amount of stock received from the manufacturer or supplier. Typically calculated on a monthly basis, this inventory KPI is especially critical in ecommerce warehouses on account of the sector’s high competitiveness and very narrow profit margins. The STR helps to detect trends in order demand and changes in product turnover.
Sales-through rate (%) = (quantity of inventory sold / quantity of inventory received) x 100
9. Backorder rate
This inventory KPI specifies the number of orders pending delivery because the product isn’t physically in stock in the warehouse. A high backorder rate could mean that the stock management strategy is not the best. However, several ecommerce businesses have implemented backordering, an inventory management method that secures the sale before actually having the goods on hand in the facility.
Backorder rate (%) = (No. of backorders / No. of total orders) x 100
10. Cycle service level
The cycle service level is an indicator that shows the probability of having enough stock available to meet product demand. A high cycle service level percentage means that the company is capable of supplying almost all the demand created for a certain product.
Cycle service level = [(No. of items sold and served) / (No. of items sold and served + No. of items sold but not served)] x 100
WMS: software that analyses warehouse performance
A warehouse management system is a fundamental tool for measuring the various inventory KPIs, as it facilitates the collection and analysis of all the data produced in a logistics facility. This information makes it possible to make key logistics planning decisions regarding stock on the basis of preselected KPIs.
Easy WMS, the WMS from Mecalux, features the advanced functionality Supply Chain Analytics Software. This module uses big data to monitor and manage information generated throughout all the logistics processes. This tool helps to identify inefficiencies and opportunities for improvement in stages such as order processing and product slotting management by monitoring indicators such as inventory KPIs. This program automates the collection of data such as backorder history, stock shrinkage, and sales through rate, facilitating the warehouse manager’s analysis tasks.
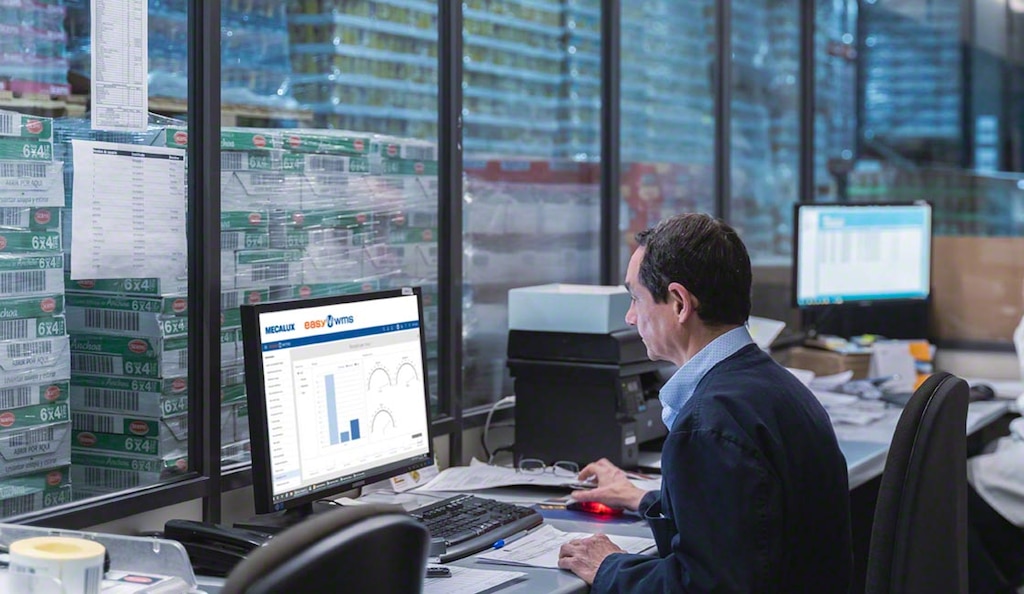
Collecting inventory KPIs: first step towards an efficient warehouse
Monitoring all logistics processes is essential to achieve maximum efficiency, and inventory management is no exception to this rule. For that reason, analysing stock control based on preset inventory KPIs is the best solution for knowing the warehouse’s real throughput at all times.
Want to enhance your logistics operations through inventory KPI analysis, controlling everything that happens in your warehouse? Don’t hesitate to contact us. One of our expert consultants will advise you on the best solution for your needs.