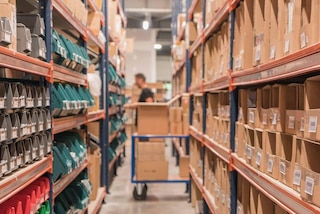
Lock stock and picking: main order fulfilment methods
The picking process and its preparation for dispatch are operations that requires the most time and effort in a warehouse. There are different order fulfilment methods: how do you know which one is the best fit for your warehouse? Let's review how picking types are classified and what considerations should be taken into account before opting for one or the other.
What are your objectives with picking?
The end aim sought from picking tasks is to reduce the time dedicated to it, to offer better customer care (e.g., shortening delivery times) and at the same time to reduce its hold on a warehouse’s operating costs where time is money.
Choosing one type of picking or another will be the right decision, if you are looking to:
- Reduce operator routes thanks to a correct layout and a good inventory zoning strategy (i.e., slotting).
- Decrease the number of operations and the time it takes the worker to perform them.
- Achieve zero-error accuracy.
- Maintain a precise stock rotation: for example, taking FIFO/LIFO criteria into account and maintaining constant control over it through a WMS.
Order fulfilment methods
1. Order fulfilment according to the direction goods flow
The two great picking paradigms are those that follow the person-product (person-to-goods) and product-person (goods-to-person) scheme:
- Product-person: is the foundation on which the installation of automated storage and picking systems is based. Machines such as stacker cranes collect the product and transport it to the operator. They are used in warehouses that require a high number of orders processed per day. It requires a higher initial investment.
- Person-product: this is the most commonly used operation when we refer to manual picking assisted by handling equipment, such as order pickers or forklifts. Its fundamental advantage is that it means a low initial investment.
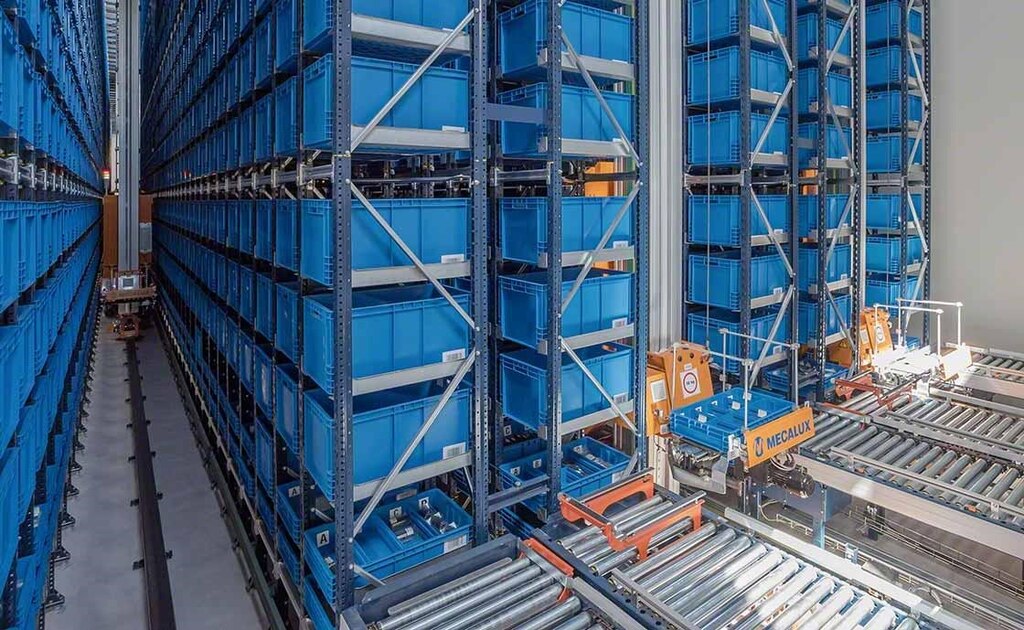
2. Picking according to the locations on the rack level
Depending on where the goods are on the racks or shelves, there are the following order fulfilment methods:
- Ground level order fulfilment : if the goods are on a single level at the ground floor.
- Lower level order fulfilment: shelve up to the operator’s height.
- Midlevel order fulfilment: levels do not exceed 11.5 or 13 ft in height.
- Order fulfilment at heights: operators adapt their movements to the full height of the shelves.
There is extensive information on each in our Technical Warehouse Manual.
3. Order fulfilment as per the way products are picked
Order picking (i.e., order fulfilment) can be carried out in different orders and phases:
- Order-by-order: This involves the basic picking procedure. The operator extracts a product and prepares the order directly afterwards. It is often used for orders involving large volumes of the same merchandise.
- Wave or group picking: In this case, the picking process is divided into two phases. First, all products are picked and placed on picking shelves and, in a second step, the orders are packed and packaged individually. This allows several orders to be prepared at the same time. It is the most common method when many SKUs are handled and each order contains just a few items. It is one of the methods that is normally recommended as a general picking improvement strategy.
- Picking by zones: This method of preparing orders organises order picking according to their location in the warehouse. As in the previous case, several orders are processed at the same time.
Criteria to consider when choosing an order fulfilment method
Choosing a pick method is directly related to the following factors:
- Initial investment: of course, this grows the more automated the solutions. However, the initial investment should not be an obstacle: The project’s ROI will be the key parameter to consider.
- Handling cost: This will depend on the type of merchandise you handle, since the handling cost is item dependent.
- Handling capacity: This refers to the number of orders that can be processed per day per time unit.
- The storage area in use: this is directly related to criteria such as the aisle width, the rack height, the floors that the warehouse has...among other factors.
Choosing the right picking method is a crucial decision that has a direct impact on the operating costs of an installation. If you would like us to put our warehousing logistics experience to the test, please do not hesitate to contact us: we would be happy to help you.