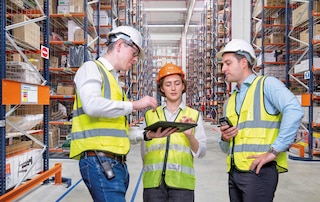
Operational excellence: principles and how to achieve it
In the business world, operational excellence represents an idea pursued by numerous companies. However, it’s often confused with similar terms.
What does operational excellence mean?
Operational excellence is a philosophy that regards problem-solving and leadership as key to continuous improvement. Rather than a set of activities or a specific strategy to follow, it involves a mindset that should be part of an organisation’s management and employees. The goal is to achieve the best possible results through optimal processes.
Also known as OpEx, this term consists of creating a culture in which workers and managers are involved and empowered to implement changes. If done well, both can grow and make better decisions. Operational excellence starts with a cultural shift that focuses on delivering quality products and providing exceptional customer experiences.
Differentiation can help your organisation stand out while continuing to execute internal procedures more effectively than competitors. The study Why do we undervalue competent management?, published in Harvard Business Review and carried out over 10 years, demonstrated that companies seeking operational excellence scored higher on metrics such as profitability, productivity, growth and longevity. Pursuing this philosophy promotes a stimulating work culture, helps meet customer expectations and provides a competitive advantage. Its results are reflected in quality, growth, costs and motivation.
What is excellence?
Excellence means making the best possible use of your available resources while maintaining continuous improvement as your objective and pivoting to business needs. In the context of companies, it can also involve minimising waste and repetition, identifying and solving problems, maximising productivity, creating satisfying user experiences and outdoing the competition.
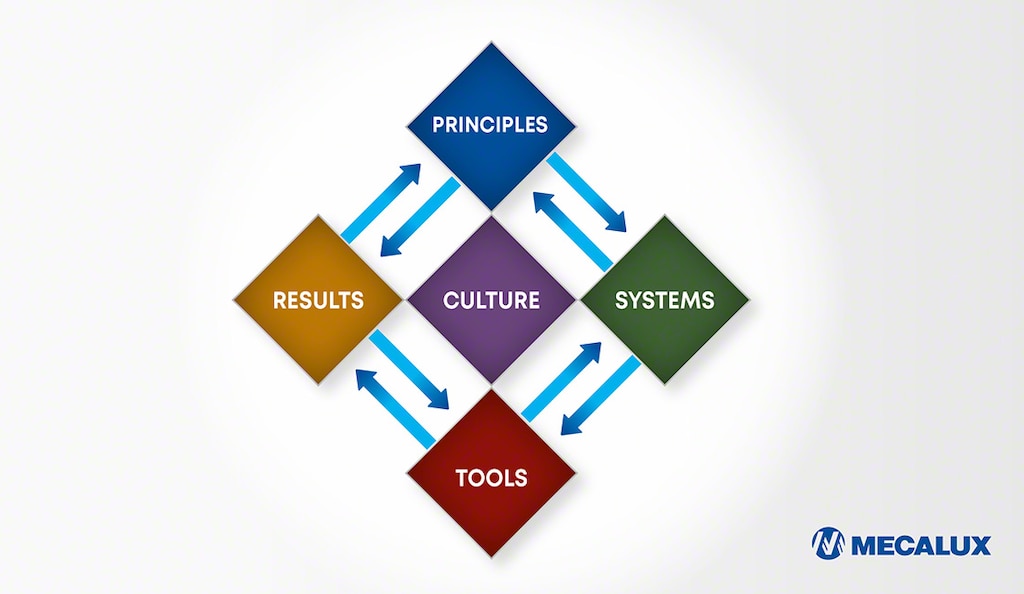
Core principles of operational excellence
The Shingo model was created by industrial engineer Shigeo Shingo. It emphasises quality, customer value and understanding the workplace at all levels. This Toyota collaborator is one of the creators of its lean manufacturing method and the inventor of the poka-yoke technique. The Shingo model’s 10 core principles are the cornerstone of operational excellence:
- Respect every individual. People are more likely to give more to an organisation when they feel valued.
- Lead with humility. This calls for implementing management systems in which leaders seek employee collaboration and the buy-in of all stakeholders.
- Seek perfection. This deals with finding new ways to act, opening the door to innovation and fresh perspectives.
- Embrace scientific thinking. This consists of creating a culture in which workers can test new ideas based on data and observations.
- Focus on the process. When things go wrong, companies should strive to improve them rather than blame individuals, which can be counterproductive.
- Assure quality at the source. Ensuring quality means doing the job right the first time, with the appropriate professionals and components.
- Improve flow and pull. Products ordered by customers must be available. You can achieve this through the lean supply chain methodology.
- Think systematically. Look for ways to boost your entire organisation instead of focusing solely on individuals or specific departments.
- Create constancy of purpose. Communicating your company’s mission, goals and customer commitments is fundamental to achieving operational excellence.
- Create value for the customer. Businesses revolve around clients, so your operations should meet all their needs.
Advantages of operational excellence
Like Toyota, companies such as Philips, General Electric, Nestlé, Danaher Corporation and Johnson & Johnson have also implemented operational excellence criteria, achieving the following benefits:
- Increased sales and customer satisfaction
- Stronger employee commitment
- Better use of resources
- Cost optimisation
- Improved quality standards
- Beneficial relationships with suppliers
Operational excellence vs. continuous improvement
While operational excellence is a mindset that fosters principles and tools for implementing new ways of operating within an organisation, continuous improvement is the ongoing effort involved in optimising processes, products or services.
Continuous improvement typically occurs incrementally over time rather than instantly or through a single change. When businesses pursue continuous improvement, they’re more likely to maintain and leverage this evolution.
Operational excellence, meanwhile, entails applying the right tools to well-defined procedures. By doing this, you’ll create the ideal work culture, keeping employees motivated and empowered.
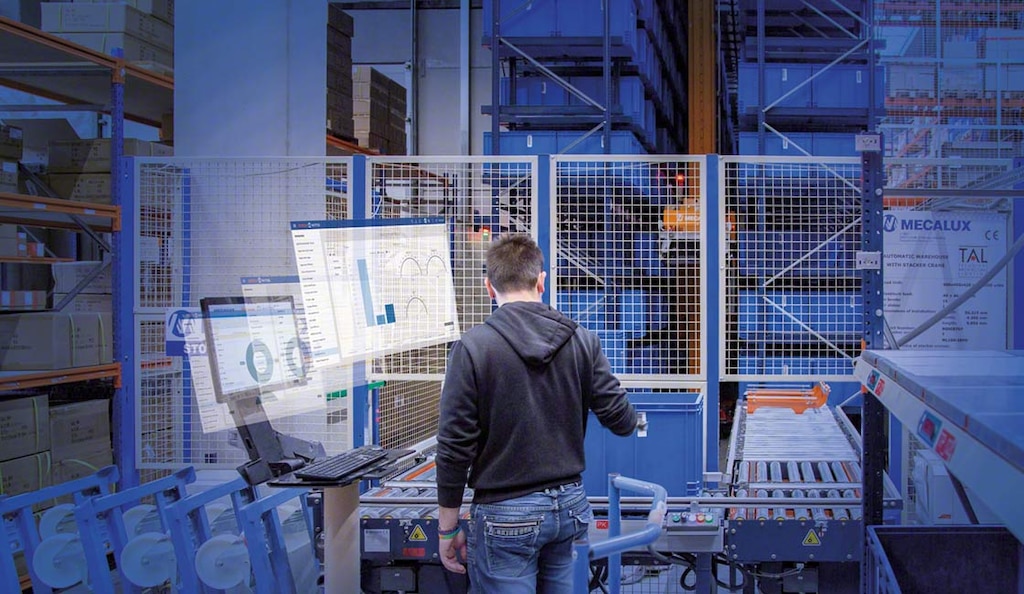
Operational excellence systems
Various methodologies can help companies achieve operational excellence. These are some of the most popular:
- Lean manufacturing. This strategy aims to eliminate waste in production systems and focus on creating value. It tackles overproduction, idle time, unnecessary travel and overstock.
- Six Sigma. This system proposes companies define, measure, analyse, improve and control (DMAIC) potential problems or challenges.
- Kaizen. This philosophy, which means improvement in Japanese, is grounded on the principle that good processes lead to positive results. It considers teamwork a key factor for success and contends that everything can be done more efficiently.
How do you measure operational excellence?
Assessing operational excellence involves thoroughly analysing multiple aspects of an organisation. It means ensuring that systems and strategies are optimised to offer maximum value. These are some areas to consider:
- Process efficiency. Study operation times, lead times and throughput to identify bottlenecks and areas for improvement.
- Quality and error rate. Monitoring services and products provided to customers delivers consistent results.
- Cost-effectiveness. This is measured by evaluating direct costs, indirect costs and cost-per-unit metrics.
- Customer satisfaction. Compiling feedback, analysing complaints and conducting surveys help to make positive changes.
- Employee engagement. As a rule, committed team members contribute towards positive outcomes. It’s advisable to analyse turnover rates, carry out surveys and hold sessions for exchanging ideas.
Achieving operational excellence in your warehouses
The most competitive organisations closely examine how they operate. They incorporate the latest technologies in their distribution centres to enhance the work of their teams. Automating and overseeing your facility with Mecalux’s Easy WMS warehouse management system will put your business on the path to operational excellence. This software provides complete visibility and traceability of all products and their status. Get in touch and we’ll find the most optimal solution for your company.