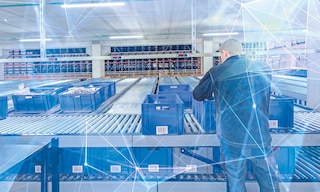
Picking systems to boost warehouse efficiency
The picking systems companies use to fulfil orders are constantly evolving to adapt to new market requirements.
Order picking is one of the most demanding operations in the supply chain for numerous organisations. With the rise of omnichannel logistics, businesses are faced with the challenge of preparing increasingly smaller orders — made up of compact-sized products — while meeting tight delivery deadlines.
What is a picking system?
Warehouse picking systems are the strategies employed to fulfil orders that will be shipped to end customers, other logistics facilities or production centres.
In the warehouse, picking consists of gathering all the products required to fill a customer’s order. It can be performed by collecting full cases (on pallets, in containers or on shelves), selecting the smaller units inside the cases or dividing bulky items such as pipes or cables into more compact units.
Given the importance of order processing in the supply chain, choosing the ideal picking system will streamline this operation. To ship the largest number of orders in the shortest possible time, you can assign operators to specific zones to fulfil orders. Another excellent option is to incorporate robotic handling equipment.
In addition to the picking system you select, you can optimise fulfilment with warehouse management software (WMS). This digital solution is an absolute must for maximising efficiency in order picking. The program distributes the goods in the facility strategically to avoid unnecessary travel and speed up the picking process.
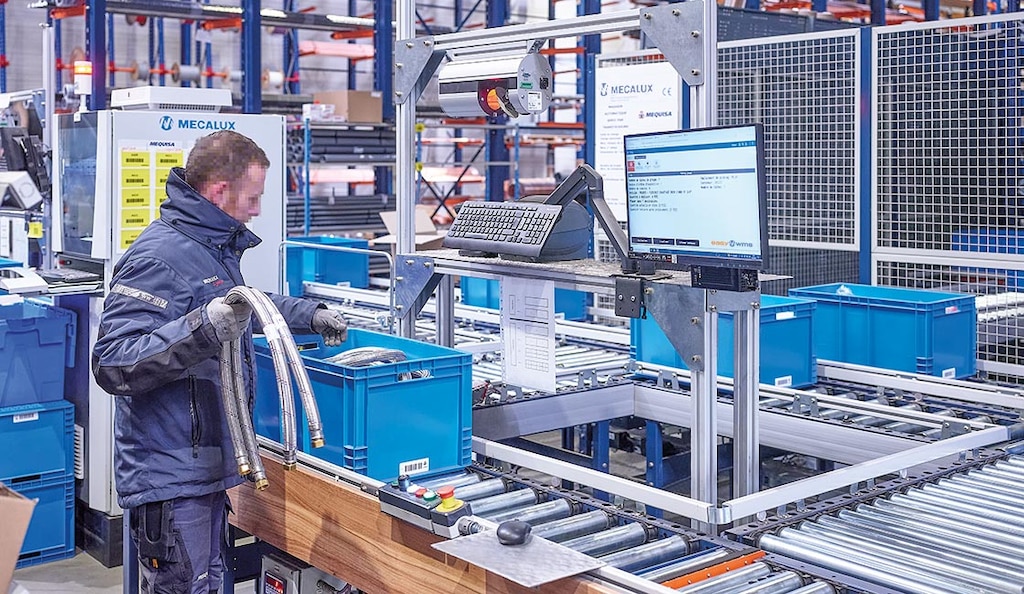
Types of picking systems
The various order picking systems and strategies can be applied individually or combined within a single warehouse:
Order picking according to work method
The way picking is performed in a facility directly affects the speed and efficiency of order picking and distribution. Operators can either travel around the warehouse to pick the required products or remain at their pick stations as automatic handling equipment moves the items to them systematically.
Cross-docking
With this working method, the merchandise received is distributed directly into orders without being stored. Cross-docking adapts to any type of good, from raw materials and components sent to production to finished products shipped to brick-and-mortar stores or end customers.
When implementing cross-docking, your facility needs to have adequate space to organise the items without storing them and to receive, sort and ship orders as rapidly as possible. It’s also best to equip your warehouse with a WMS to manage the merchandise effectively and minimise mistakes.
Person-to-goods
With this picking system, operators move through the facility, locating the products that will make up a specific order. These workers typically remove merchandise from the shelves and place it in carts. Once in the consolidation area, the items are sorted into orders.
The person-to-goods system is applied much more efficiently with a WMS. Following the software’s instructions, operators walk the shortest distances and complete orders more quickly.
Goods-to-person
Also known as product-to-person, goods-to-person is the most common method used in automated storage and retrieval systems (AS/RS). Operators stay at their pick stations while automatic handling equipment brings them the merchandise, they need to put together orders.
With mini-load systems (AS/RS for boxes) and the Shuttle System, conveyors transport the items to the pick stations. There, operators receive bins and remove the stipulated product units. Subsequently, the remaining goods are automatically returned to the shelves.
Automated order picking systems
To automate warehouse picking, you can swap manual movements of materials with machines and technologies that enable end-to-end robotic order picking. Robots ramp up operational throughput, as they can work 24/7 without making mistakes.
An automated warehouse picking system is the perfect solution in logistics facilities with high order volumes and in complex environments like cold stores. For example, automatic movements of merchandise with stacker cranes, conveyors and autonomous mobile robots can be enhanced by incorporating anthropomorphic arms designed to accelerate picking.
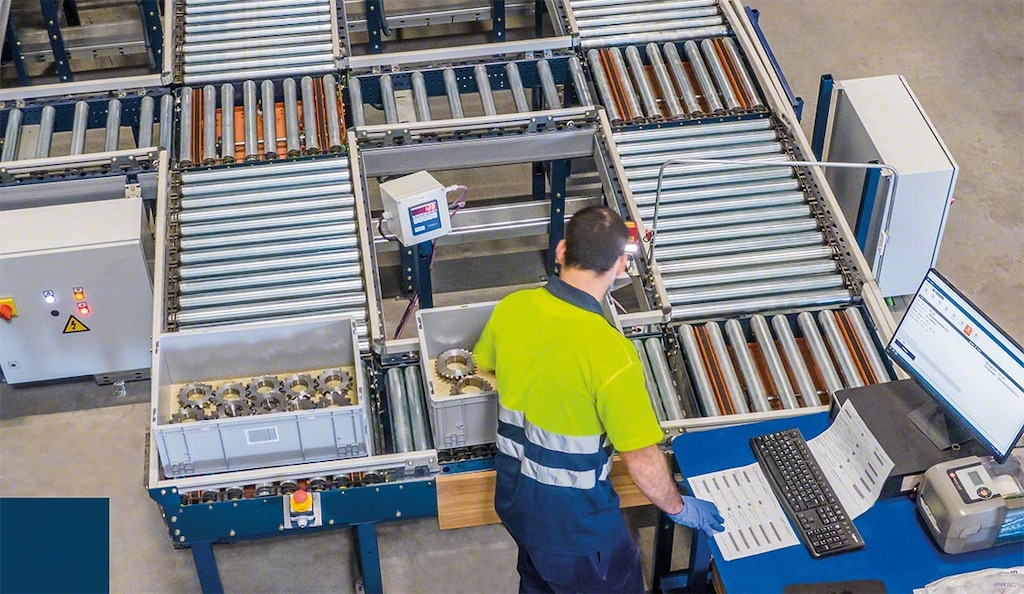
Zone picking
When planning order processing, it’s up to the logistics manager to decide whether to allocate a single workspace to picking or divide the operation into different zones. In the latter case, operators are assigned to a specific area to pick and fill orders.
One or more picking zones
The facility is split into different spaces based on multiple criteria such as product type, demand level, storage conditions and number of SKUs. Each zone is assigned a certain number of operators, who retrieve merchandise stored in their area, optimising picking times.
Orders prepared across multiple zones are eventually taken to the consolidation area, where they’re checked to make sure they include all the requested products before being distributed. To speed up the operation, you can install a conveyor system to connect the different picking zones with the shipping area.
One or more floors
To make the most of your building’s height, two go-to solutions are mezzanine floors and multi-tier shelving. Each level can comprise a single zone or be subdivided into several areas. It’s also crucial to plan how you’ll transfer materials between floors.
To make multi-zone/multi-level picking effective, you can deploy a WMS to automatically coordinate movements of operators and goods. The program organises all fulfilment stages and comprehensively controls operations to avoid errors.
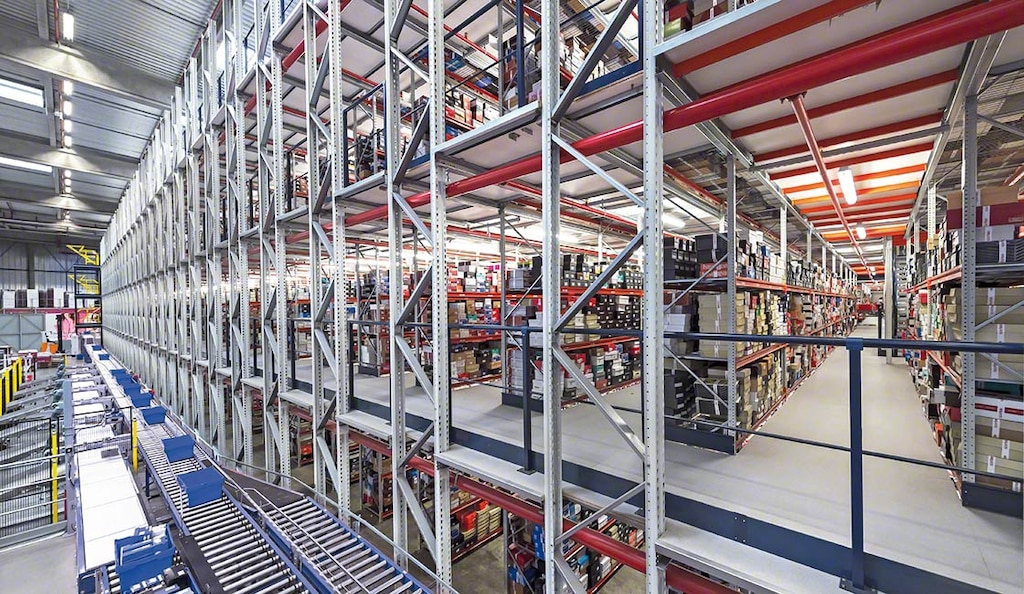
Picking by order grouping
Orders can be picked individually or in batches. Your choice will depend on the number of orders to be filled or customer urgency.
Discrete picking
Operators walk around the warehouse to locate and pick the items they need one by one. Then, they move the completed order to its destination point. The pickers repeat the process for each assigned order. The discrete picking system is generally applied in small facilities or companies with retail stores.
The advantage of this working method is its simplicity. Once the order is filled, it merely has to be packed and labelled prior to being sent to the customer. Orders containing full cases can be grouped on a pallet, which is subsequently sent to the shipping area.
Batch picking
With this picking system, operators locate the SKUs required to fill several orders simultaneously on a single run through the facility.
The items are then transferred to the consolidation area, where they’re arranged into orders. You’ll need to plan how to move the goods to this zone, whether by cart or other types of material handling equipment such as box conveyors.
Wave picking
As with batch picking, operators also complete multiple orders at once with this picking system. In wave picking, operators sort products into orders as they remove them from their locations. Pickers use a cart with different boxes, each corresponding to a specific order.
For wave picking to be effective, operators should use handling equipment outfitted with a system that prevents errors. One widely-used solution is put-to-light devices, which show operators which totes to place each item in.
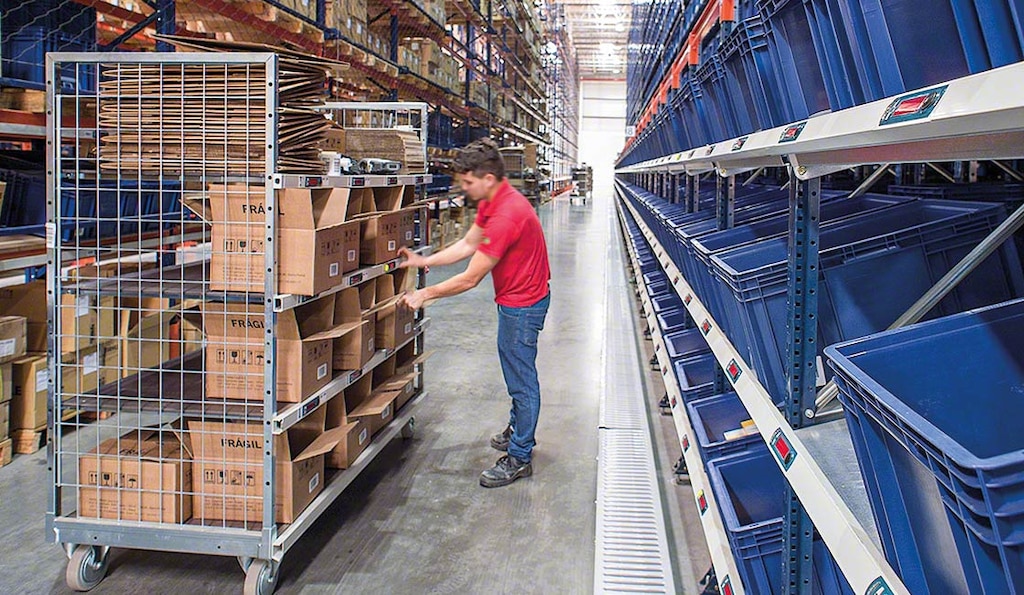
Maximum efficiency in order picking
Order picking is a key warehouse operation. To fulfil as many orders as possible, it’s necessary to make a number of strategic decisions. In addition to implementing WMS software, you should choose the storage system, picking assistance devices and picking systems that best fit your business requirements.
The optimal solution is the one that aligns with the unique characteristics of your company. It should address your specific warehouse needs and meet your business’s expectations. At Mecalux, we’ve been developing logistics solutions for organisations from all sectors for more than 55 years. Be sure to get in touch. We’d be happy to guide you in optimising key operations like order picking.