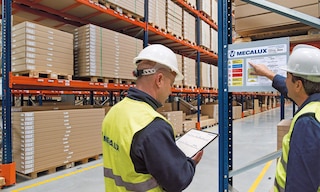
Predictive maintenance: techniques and advantages
Predictive maintenance helps avoid future disruptions or breakdowns in production lines, storage systems and supply chains before they happen, which is financially beneficial for businesses. But what does it consist of, exactly?
What is predictive maintenance?
Predictive maintenance is a technique that uses machine learning and asset monitoring to identify anomalies and defects in equipment and machinery before the event of a failure or changes in their correct functioning. Also referred to as PdM, predictive maintenance is part of regularly scheduled maintenance activities. It minimises interventions, avoids unplanned downtime and reduces costs. Predictive maintenance aims to keep physical assets in optimal condition.
How does predictive maintenance work?
Industries rely on three main components to carry out predictive maintenance in their supply chains:
- Internet of Things (IoT). Sensors and devices send real-time data on the condition and performance of machines via the IoT, providing analytics systems with more inputs.
- Software and cloud storage. Cloud computing opens the door to data mining, i.e., the analysis of large volumes of information through big data.
- Predictive models. Machine learning is trained based on previously processed knowledge. Therefore, predictive models establish patterns, make comparisons and generate predictions. This allows companies to avoid failures by scheduling tasks before any shutdowns or breakdowns occur.
Advantages of predictive maintenance
Leveraging technology to perform predictive maintenance on machinery minimises repair times as well as the cost of supplies and spare parts. According to a study by consulting firm McKinsey, this practice can reduce machine downtime by 30% to 50% and increase machine life by 20% to 40%. It also has other positive aspects:
- Energy consumption savings. Certain types of breakdowns can result in excessive power consumption. Examples include overheating or leaks in compressed air systems.
- Increased productivity. By shortening equipment repair times, preventing the total replacement of machinery and minimising downtime, businesses can carry out planned actions without unforeseen interruptions.
- Workplace safety. Predicting potential incidents reduces the risk of accidents, ensuring employee safety.
- Improved parts control. Knowing beforehand what components will be needed allows for better inventory management and guarantees their availability.
- Optimised maintenance. Instead of scheduling routine checks, predictive maintenance is only performed when necessary, resulting in a more efficient use of resources.
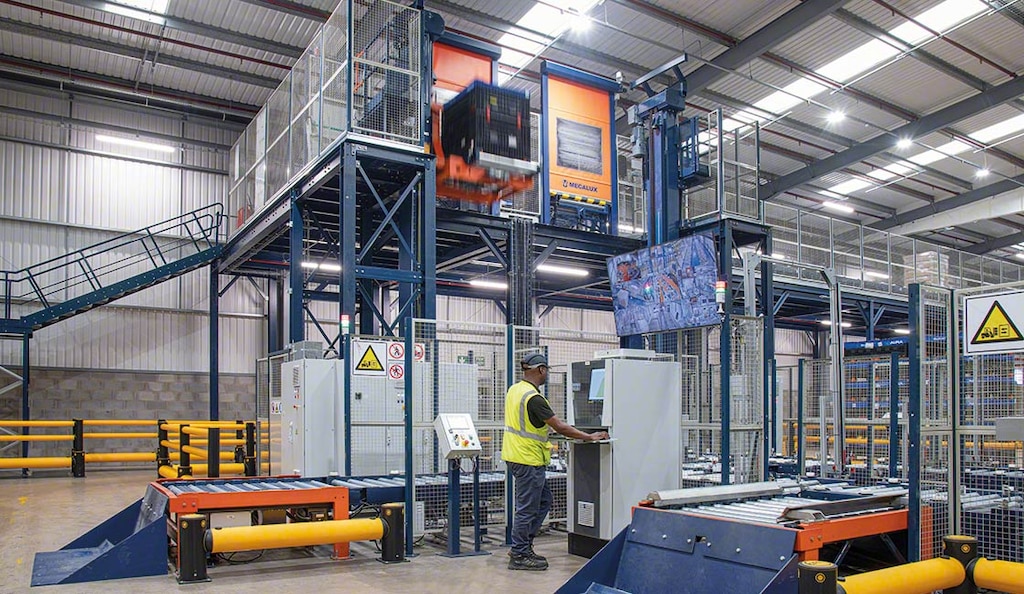
What are the types of predictive maintenance?
There are four general ways to organise predictive maintenance:
- Condition-based predictive maintenance. This system is designed to schedule maintenance tasks before a failure occurs and after inspecting a machine’s condition. It can be based on time or the usage of the devices.
- Time-based predictive maintenance. This follows an interval marked on a calendar and is performed at a preset time.
- Usage-based predictive maintenance. This model considers the equipment’s average daily use and exposure to environmental conditions. Based on this, a deadline is set for a future inspection.
- Prescriptive maintenance. This type of maintenance anticipates the error that will occur, when it will happen and its root cause. Accordingly, companies can analyse how to rectify it and its potential outcomes, mitigating operational risks.
Analysis techniques commonly deployed in the predictive maintenance of machines and components include infrared thermography and acoustic monitoring. Infrared thermography detects high temperatures, while acoustic monitoring locates gas or liquid leaks, vacuums, friction and stresses.
Who uses predictive maintenance?
Typically, the professional profiles that use these methods are production, supply chain and logistics managers, in addition to personnel responsible for equipment and facility upkeep. Predictive maintenance is used in sectors where operational efficiency and continuity are essential:
- In manufacturing plants, PdM optimises production lines to avoid downtime. One example is the automotive industry.
- In the energy sector, PdM enables turbines, devices and electrical networks to continue operating, ensuring a constant supply.
- In aviation, it prevents interruptions and aircraft breakdowns.
- In the oil industry, PdM is used on platforms and wells.
- In healthcare, it keeps medical equipment operational at all times.
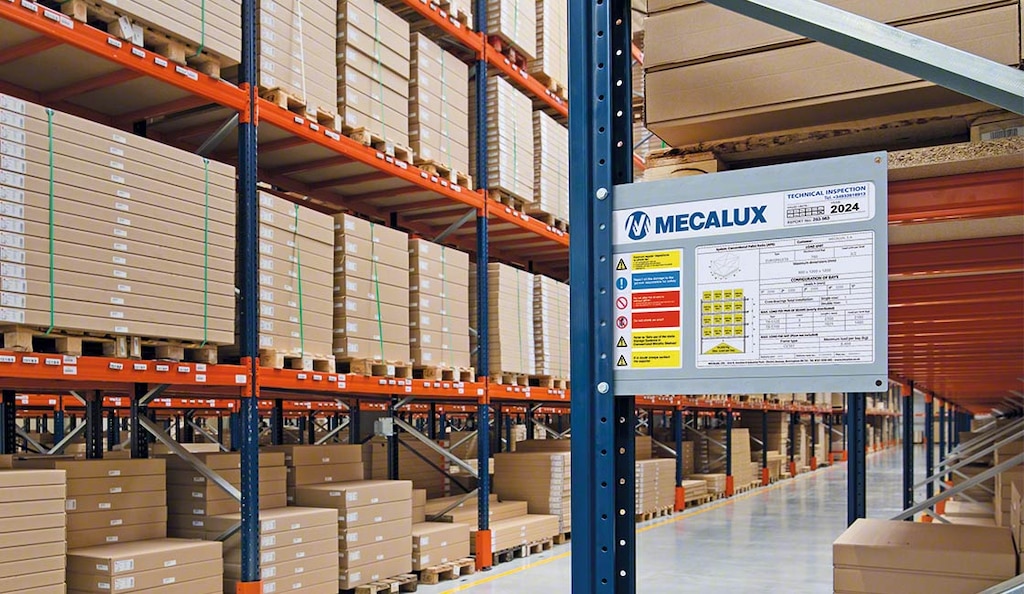
What are the differences between preventive and predictive maintenance?
Although they might seem similar, preventive and predictive maintenance are two different concepts. Predictive maintenance can be seen as an evolution of preventive maintenance.
Preventive maintenance | Predictive maintenance |
---|---|
Planned. | Proactive. |
Uses scheduling software to notify users when equipment maintenance is due. | Employs technology to address potential problems and schedule repairs before errors occur. |
For industrial equipment, this can involve researching general information on its brand and model to estimate when it should be inspected. | Centred on the performance of company assets and data collection. |
Provides indicators on asset health and performance. | Improves inventory efficiency by reducing reliance on spare parts. |
Requires periodic machinery shutdowns. | Ensures infrequent and brief machinery downtime. |
Usually employs maintenance checklists and standard operating procedures. | Leverages advanced tools, devices and analytics software. |
Example: When a car reaches a certain mileage, a dashboard warning light alerts the driver to change the oil. | Example: Conclusions are drawn by combining details from the expected life cycle with those from the historical performance of that particular unit. |
The two techniques seek to prevent errors proactively. However, as the table shows, predictive maintenance goes a step further.
Future of predictive maintenance: AI and the IoT
Predictive maintenance has been expanded through the Industrial Internet of Things (IIoT). Now that the devices in this network can share information on their activities and conditions, PdM models obtain the data required to make accurate predictions.
Warehouses and distribution centres are also crucial types of industrial facilities. Are you looking to foresee potential incidents such as bottlenecks and pinpoint their location? To do this, controlling your operations and goods would be highly beneficial. At Mecalux, we’re experts in this area. Our warehouse management system provides you with a comprehensive view of all your company’s logistics processes. Feel free to get in touch. We’ll advise you on this and other automated and conventional storage solutions, ensuring their optimal maintenance.