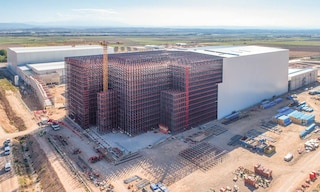
Rack supported building: maximum capacity
Interested in maximising both your storage capacity and operational speed? A rack supported building could be the perfect choice for enhancing your intralogistics processes.
What is a rack supported building?
A rack supported building is a warehouse where the racking that holds the goods is part of the frame that supports the facility. The racks are the main structural component of these facilities, which require neither pillars nor columns.
Rack supported buildings sustain the loads of stored goods in addition to the side and roof enclosures and the effects of external agents (e.g., wind force). This solution brings companies multiple advantages, including space maximisation. However, it must be designed to spec by qualified professionals.
Advantages of rack supported buildings
Also known as clad rack warehouses, rack supported buildings offer businesses several benefits:
- Space maximisation. By housing goods from floor to ceiling, these high-density facilities significantly increase the total storage capacity.
- Fast construction. Rack supported buildings require minimal civil engineering work. This facilitates their construction, which begins by pouring a concrete slab on a compacted surface.
- Great height. Maximum building height restrictions are defined by local regulations, though it’s also crucial to consider the material handling equipment your company will use. Generally, these facilities are under 45 m tall. That said, one way to maximise efficiency is to use stacker cranes or miniload systems. These automated storage and retrieval systems (AS/RS) reach considerable heights without jeopardising safety.
- Easy expansion. These installations, composed of assembled elements, can be extended very simply. Congelados de Navarra, a producer of deep-frozen vegetables, commissioned a 36-metre-tall rack supported building for 27,000 pallets in partnership with the Mecalux Group. A major increase in sales led it to set up a second cold store with a capacity of 36,000 pallets attached to the first. Years later, it created another space with the same characteristics for semi-finished products.
- Safety. These warehouses resist inclement weather such as wind and snow.

How does a rack supported building work?
Rack supported buildings can be tailored to individual customer needs, but by and large, they fall into three major categories:
- Automated rack supported buildings. Incorporating AS/RSs such as stacker cranes for pallets in a rack supported building leverages up to 45 m of vertical space to store goods. Moreover, these automated facilities are typically operated using a warehouse management system like Mecalux’s Easy WMS. This makes them one of the most efficient intralogistics options.
- Rack supported buildings for cold storage. These designs are compatible with cold stores for refrigerated or frozen products. They can be manual or automated.
- Manual rack supported buildings. Operations in these types of clad rack structures are performed using forklifts.
How is a rack supported building constructed?
The design and assembly of rack supported buildings differ from those of conventional warehouses. They normally involve these steps:
- Calculations. The building is designed considering the weight to support and other aspects such as standards.
- Foundation construction. The concrete slab is laid. It will support the structure and drainage systems.
- Racking installation. The racks are assembled, starting from the front end.
- Cladding. The enclosures (roof and facades) are attached as the work on the rack installation progresses, with the racks serving as the building’s structural components.
- Introduction of machinery. If the rack supported building is automated, handling equipment (e.g., stacker cranes) is incorporated at this stage.
- Other areas. Receiving and shipping zones are set up in building annexes.
- Final. The remaining racking and cladding are assembled.

Companies with rack supported buildings
More and more organisations from different industries are integrating rack supported buildings into their logistics activities. They’re advantageous for companies in any sector, including automotive, food, pharmaceutical, transport and logistics providers. In addition to Congelados de Navarra, these are some companies that use them:
- BASF. Chemical manufacturer and distributor BASF has a large rack supported building in the Brazilian town of Guaratinguetá. At 30 m high and 101 m long, it provides 1,400 m² of floor space for storing chemicals.
- Cepsa. “We’ve integrated our manufacturing, packaging and shipping processes into a single facility,” say Cepsa representatives. This energy group specialising in hydrocarbons reduced its logistics costs by setting up a rack supported building in the Spanish town of San Roque.
- Würth. German company Würth markets all varieties of professional fasteners, joints and assembly components. At its rack supported building in Agoncillo, Spain, it handles tens of thousands of SKUs. Würth now stores 15,000 pallets in just 3,500 m², which would have been impossible in its former conventional facility.
Mecalux rack supported buildings
Are you looking to open a storage facility that maximises space utilisation, is easily expandable and has annexes for production and shipping? If so, a rack supported building could be the solution. At Mecalux, we have extensive experience in designing and assembling these types of logistics centres. We’ll guide you in planning and building the warehouse your business needs. Contact us, and we’ll help you transform your processes.