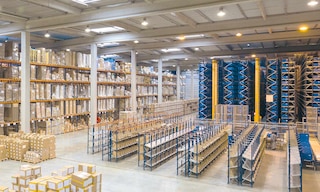
Racking systems: types and how to choose them
Identifying and installing the right racking system for your warehouse operations can make the difference between optimal logistics performance and bottlenecks. You’ll find a wide variety of industrial racks in today’s market. The ones produced by top manufacturers undergo testing and simulations, comply with regulations, follow the strictest safety controls and incorporate high-quality raw materials.
What is a racking system?
A racking system consists of several modules with shelves used to store industrial products and other types of items on pallets or in boxes or bins. The racks are typically made of metal and play a crucial role in facilities like warehouses and logistics or production centres.
Unlike wooden structures, metal rack storage systems withstand intensive use and facilitate material handling. Therefore, they’re compatible with material handling equipment such as forklifts, typically employed to store and remove pallets from the racks.
Advantages of racking systems
Incorporating racking systems into your operations to raise competitiveness brings multiple benefits, for example:
- Inventory control. Well-organised storage systems streamline operations. They allow for better tracking, from receiving to order fulfilment and shipping.
- Increased storage density. Compact racking systems concentrate large amounts of materials in the same available space.
- Space utilisation. Floor space is limited, and purchasing logistics real estate can be costly. Thus, designing a well-organised warehouse layout with the right racking systems or automated storage and retrieval systems (AS/RSs) is more cost-effective.
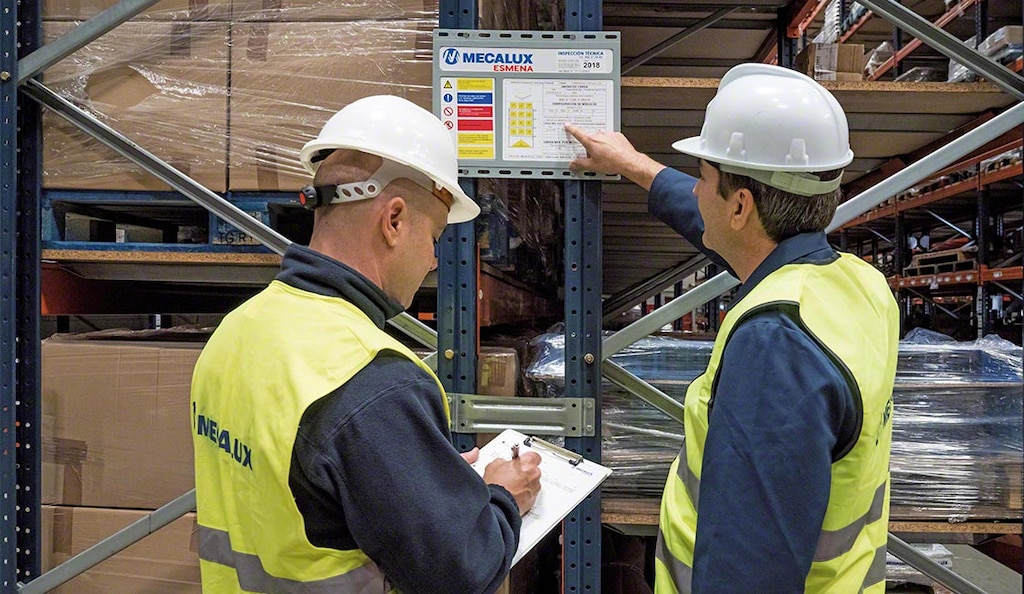
How do I choose a racking system?
Using the appropriate equipment for each task is essential for ensuring warehouse efficiency. As a result, racking systems vary greatly depending on a company’s sector and activity. Your end goal in selecting a racking system for your business is to save time and money during operations. These are some factors to take into account:
- Characteristics of boxes or pallets. Knowing the size, shape, quantity and weight of the unit load that best fits your inventory is vital for choosing the perfect racking system.
- Warehouse layout. In addition to the available square metres of floor space, it’s fundamental to consider the height of your facility. This factor can be decisive for its capacity to carry out large or small operations.
- Accessibility. Operators must be able to reach pallets and materials quickly and efficiently.
- Budget. Consider which option will be more cost-effective in the long term. Some might require a more substantial initial investment but deliver a generous return and superior strength and durability.
To make the right choice, it’s advisable to rely on storage experts and familiarise yourself with the main types of racking systems.
Types of racking systems
Racking systems can be grouped into three major categories: pallet racks, picking shelves and other racking solutions.
Pallet racking
With pallet rack systems, loads are stored and removed using forklifts. They can provide direct access to each pallet or function as a high-density solution.
- Selective pallet racking. This system offers direct access to every SKU in the warehouse. It’s the most universal storage solution thanks to its versatility and is suitable for companies with very varied SKUs.
- Drive-in/drive-through racking. This is the simplest and most affordable high-density system. It consists of racks with lanes accessed by forklifts to deposit and retrieve pallets at several levels and depths. With drive-in racking, pallets are loaded and unloaded from the same working aisle. With drive-through, pallets are stored from the front aisle and retrieved on the opposite side.
- Mobile racking. Mobile racking systems combine the two advantages of the previous types: they store unit loads in a compact way while allowing direct access to each pallet. The racking is installed on motorised mobile bases that enable controlled movement of the blocks. These can be joined or separated to open the required aisle as needed.
- Pallet flow racking. In this high-density storage solution, pallets move by gravity along channels equipped with rollers. Loads are inserted in the highest part of the channel and slide forward to the opposite end.
- Push-back racking. This similarly compact storage solution houses several pallets deep and a different SKU per channel. Loads are pushed along slightly sloped channels.
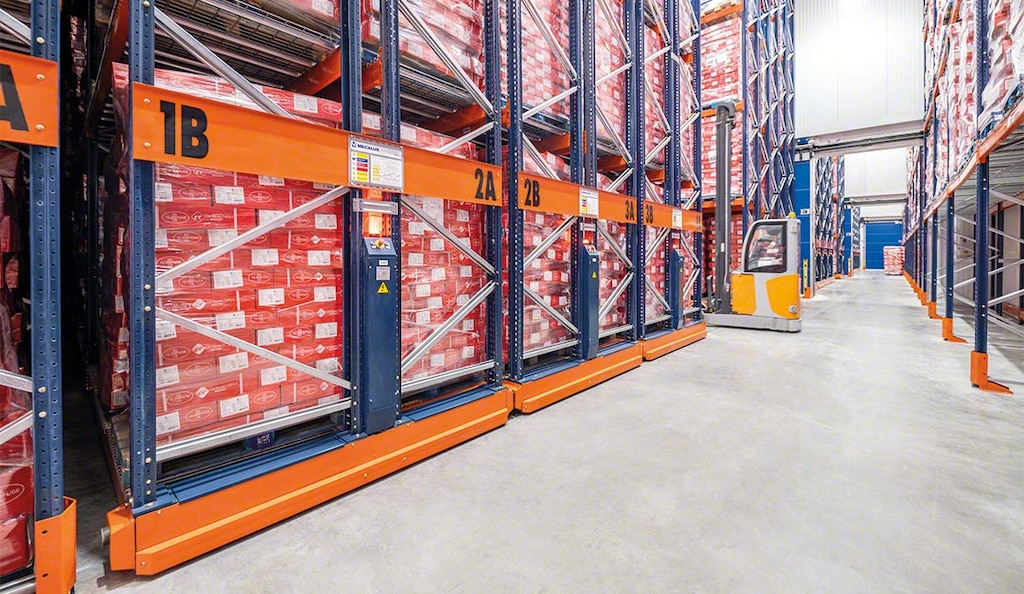
Picking shelves
Picking shelves accommodate individual boxes and loose items picked manually. They generally fall into these categories:
- Medium and heavy duty racking. Top-quality shelving supports weights of more than 1,000 kg per level.
- Light duty shelving. This is designed for moderate loads in warehouses, workshops, offices and shops.
- Live storage for picking. In this gravity flow storage system, goods are placed on slightly inclined roller platforms. This convenience streamlines order picking and ensures SKU turnover.
- Multi-tiered shelving. This solution for non-palletised goods consists of combining high-bay shelving with one or more walkways supported by the racking system.
Cantilever racking system and others
Besides picking operations and pallet storage, a racking system can come in handy in several other cases. Cantilever racking, for instance, is specially designed to house long loads (e.g., tubes) and products of varying sizes. It’s also common practice to use specific racking for products such as reels.
Installing racking systems with Mecalux
Identifying which racking system is ideal for workflows in your centre will maximise your throughput. As this decision involves multiple factors, it’s best to count on the guidance of experts. At Mecalux, our extensive experience designing and installing racking systems dates back to 1966. Get in touch, and we’ll provide you with consultation on this and other aspects like intralogistics automation and digitalisation of internal transport, inventory and order fulfilment through software.