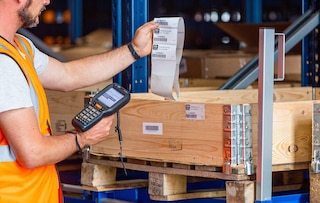
What is a SKU? Meaning and in-warehouse usage
SKUs or Stock Keeping Unit codes are one of the fundamental elements for keeping track and managing stock in a warehouse. A SKU is a product's one-of-a-kind reference number, as registered in a company's system.
What characteristics define SKU codes?
Here, we descramble the meaning of SKU or Stock Keeping Unit when it comes to inventory management:
- It identifies the smallest sales unit. For example, in a footwear company one of its SKU codes could be a pair of white size 41 sports shoes of a specific model (and not each individual shoe as they are not sold separately).
- A SKU is a unique code that is usually composed of letters and numbers. Normally, it is possible to deduct from this data which product it refers to. However, those generated automatically by computerised systems are not as easy to guess. As in the previous example, a very basic SKU for a pair of white size 41 sneakers model XYZ could be DEPOR-XYZ-BLN-41.
- SKU codes are generated by the company's ERP, while the WMS connects to the ERP and manages the SKU codes in all warehouse operations.
- The parameters upon which a SKU is created are determined from the attributes of the product being stored and each combination results in a different SKU code. The white size 41 sneakers will have a certain SKU, but the size 39 ones will be assigned a different Stock Keeping Unit.
- A SKU’s function is to record the characteristics of each product stored in a specific place. Because this code represents the smallest stored unit in detail, the Stock Keeping Unit allows for greater accuracy in the warehouse's available inventory and better traceability of product references at different supply chain stages.
- If there are several units of the same SKU, they will share SKU number, since they are identical.
- SKUs can also refer to services. But, in this example, we focus on their value for warehouse inventory management.
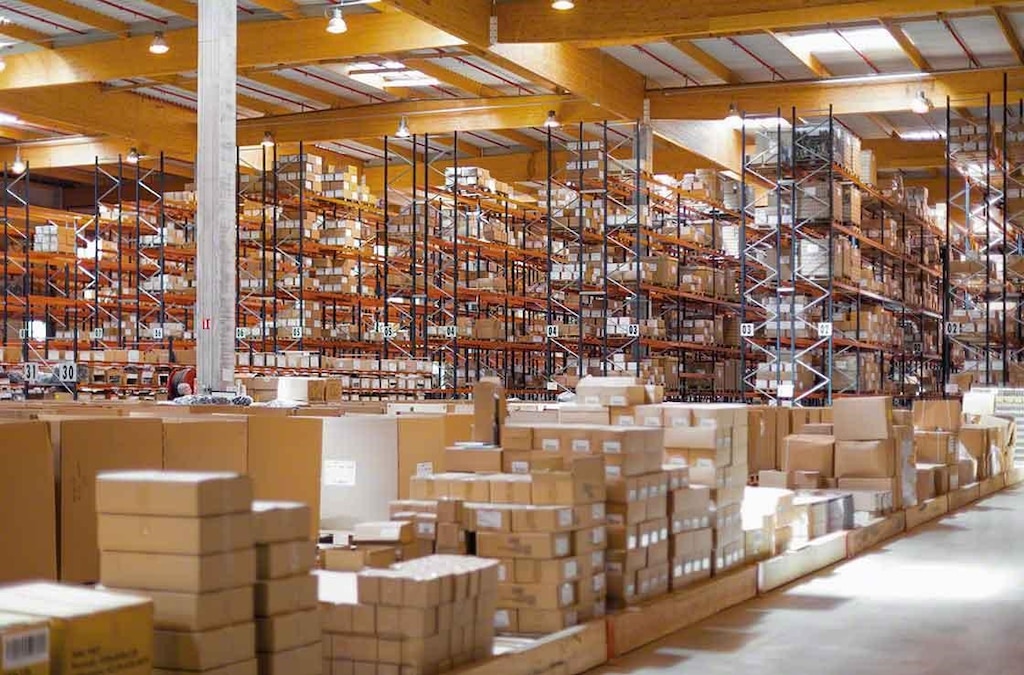
What is the difference between SKU, EAN and UPC codes?
SKU codes in a warehouse are the master keys that unlock the doors to accurate inventory control. But in practice, product tracking is done by scanning barcodes that record each stock movement in the software. This is why SKU codes are often confused with EAN (European Article Number) or UPC (Universal Product Code) codes, or are generically called ‘barcodes’.
So, what are SKUs compared to other formats? To clear up any doubt, the following table shows the main differences between them:
SKU | Bar codes (UPC, EAN) |
---|---|
It is alphanumeric. | It is a series of numbers. |
Its length is variable, although it should always be short (between 8 and 12 characters). | 12 digits, which go with a scannable barcode. |
Each company can set their own parameters according to the products they handle. | International standards regulate how barcodes should be configured. They are administered from the global organisation called GS1. |
Its length is variable, although it should always be short (between 8 and 12 characters). | 12 digits, which go with a scannable barcode. |
A SKU contains information about the product for managing a company's inventory: colors, sizes, warehouse locations... | It comprises handy information to identify manufacturers, trading companies, production origin... |
These data are for internal use. It can be different in each company that markets a product. | This is for external use. It is the universal code that comes marked on the product. It remains unchanged throughout the supply chain. |
The inordinate rise of the SKU: both friend and foe
Many warehouses are facing the challenge posed by the disproportionate growth of SKUs, a phenomenon known as SKU proliferation. At the root of this trend is the fact that customers demand a wide range of products and require immediate access to them. So, it is easy for the number of stored SKUs to skyrocket, increasing the minimum assumable stock levels.
Managing this complexity is key and, therefore, stock management strategies need cutting-edge tools that know how to resolve all these different situations. Ultimately, the goal is to optimise the available inventory and their in-warehouse locations. As such, it is increasingly difficult to achieve this without a powerful warehouse management system that centralises information and uses it to improve the global performance of the warehouse installation.