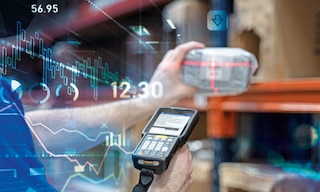
Stock coverage: What is it and how do you calculate it?
Stock coverage is an inventory management formula that lets you know the exact amount of inventory available in your warehouse to cover demand.
Knowing your precise stock coverage ratio is essential to ensure that your business can fulfil customer orders without experiencing stockouts.
What’s stock coverage?
Stock coverage is a logistics metric that shows the period — usually expressed in days — during which a company can meet customer demand with the available inventory in its warehouse. To calculate this key performance indicator (KPI), you divide the amount of stock stored in your facility by your average sales for a given period.
In the book Stock management: Excel as an analysis tool, logistics consultant and professor Mikel Mauleón defined stock coverage as “the number of days a business can meet demand with the average stock.” Nevertheless, the author notes that, when it comes to stock coverage, there are nuances: “Warehouse managers prefer to talk about a one-off coverage period. That is: As of today, with the anticipated number of sales, how many days will stock be available?”
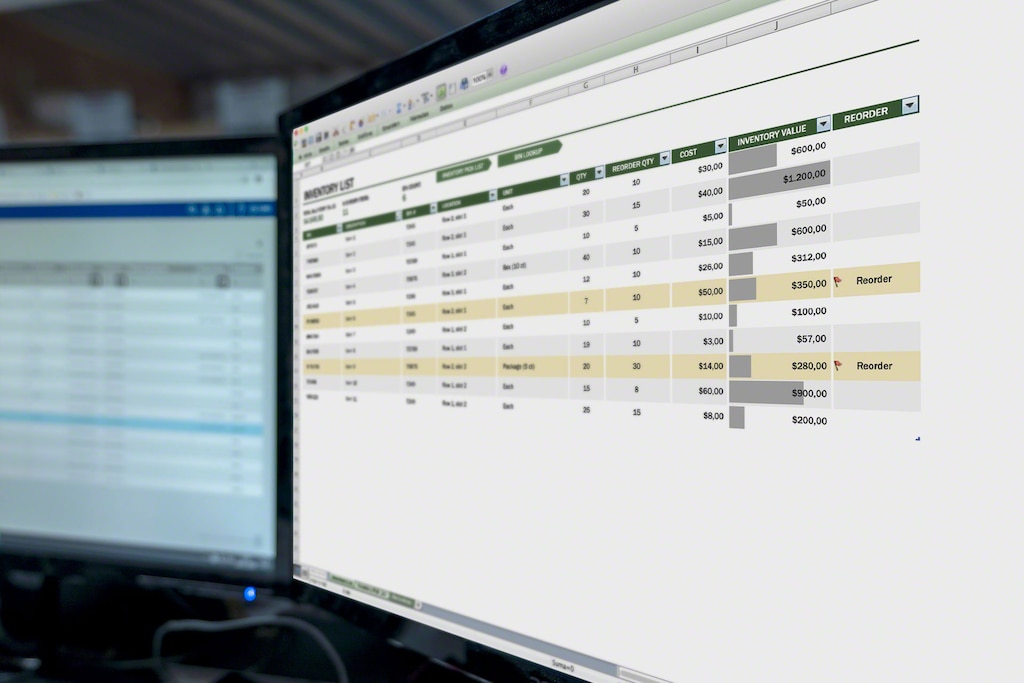
The numeric value obtained by this mathematic formula is extremely beneficial for inventory management. By knowing their real stock availability and average demand, logistics managers can anticipate or delay orders from suppliers or redistribute the facility to boost efficiency, among other actions.
How is stock coverage calculated?
Stock coverage allows you to estimate the period during which your business will be able to fulfil orders without having to purchase new product. To calculate this value, you divide the available stock by the average product demand over a specific period of time.
Thus, the stock coverage formula is as follows:
Let’s illustrate this with an example: an e-commerce retailer has a warehouse for storing, preparing, and dispatching its goods. This company sells 10 pairs of socks a day. If the current stock volume is 400 pairs, the stock coverage ratio will be:
The result in this case is 40, so the business has a stock coverage of 40 days for socks with the current average demand. In other words, with its available stock, this retailer can fulfil orders for 40 days.
How to interpret stock coverage
Stock coverage consists of a numeric value indicating the number of days a business can cover sales with its current stock. Logically, you should aim for a high stock coverage ratio in order to have maximum inventory availability without resorting to stock replenishment.
Nevertheless, if your company has excess stock in relation to normal demand, this could push up storage costs and make inventory handling more complicated. Moreover, in warehouses with perishable goods, overstock could cause the products to lose their properties if stored for too long.
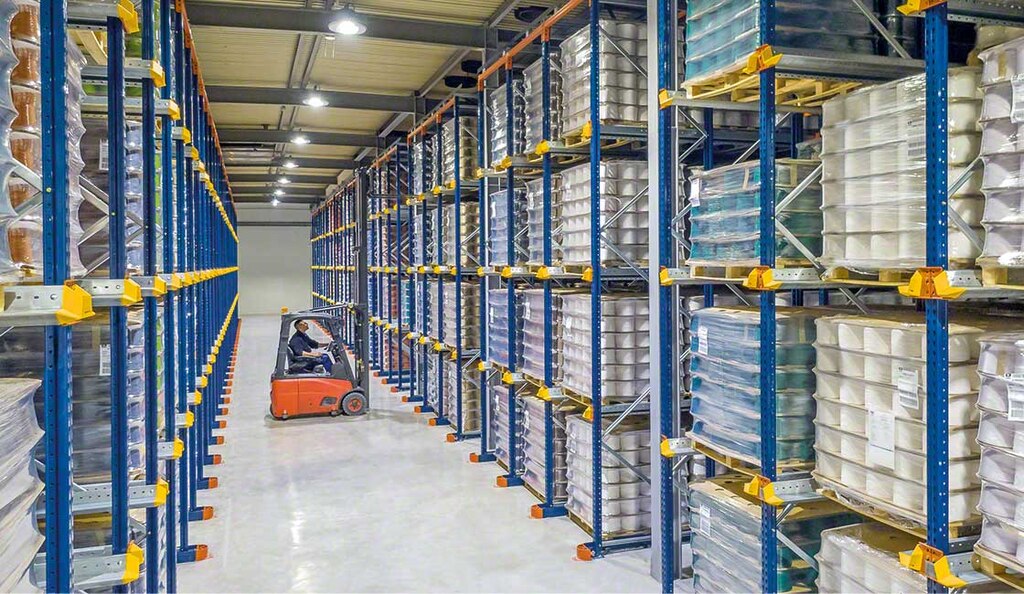
On the other hand, having a low stock coverage ratio could lead to stockouts. That is, you’d run a greater risk of not being able to fill orders due to lack of available stock.
Therefore, efficient inventory management is based on the concept of optimal stock levels, i.e., the ideal amount of stock to satisfy product demand without incurring unnecessary costs. This numeric value is calculated by means of the EOQ formula. Also known as the reorder point, this formula indicates when to place an order with a supplier and in what quantity to maintain stock availability. Tight stock control is key for guaranteeing that the required goods are on hand at all times.
Inventory software for zero errors
Office software programs such as Microsoft Excel can automate the stock coverage calculation to a certain extent. However, computing this variable manually increases the chance of error in inventory management. The complexities involved in goods management are driving companies to invest in tools that automate inventory control, providing logistics managers with real-time information on the status and availability of stock, its location, and product demand.
Implementing a warehouse management system (WMS) such as Easy WMS from Mecalux automates stock control and eliminates inefficiencies from inventory management. This ensures complete product traceability, as the logistics manager always knows where each item is and what processes it’s undergone.
In addition to organizing all operations in the facility, this software controls inventory in complex logistics scenarios including multi-store management, omnichannel retail, and marketplace sales.
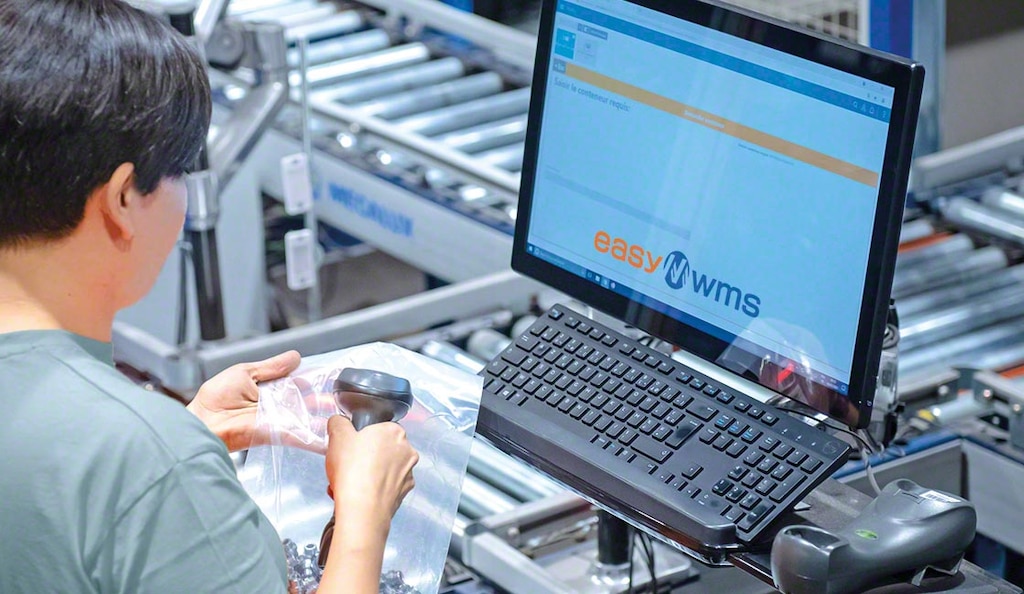
Stock coverage for effective order fulfilment
Stock coverage is a critical metric for guaranteeing inventory availability. Nonetheless, SKU proliferation in logistics facilities makes it more difficult to manage goods manually.
Against this backdrop, businesses rely on digital solutions like Easy WMS. This software automates inventory control, providing logistics managers with the stock coverage ratios for the quantities of goods stored in their centres. Interested in boosting your company’s throughput? Don’t hesitate to contact us. One of our expert consultants will advise you on the best digital solution for your warehouse.