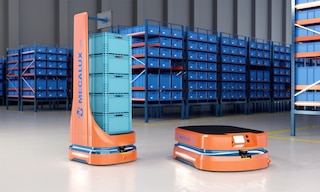
Tote-to-person: automated transport of picking totes
Logistics is constantly evolving, and there are more and more methods for achieving smooth, efficient operations to streamline the internal transport of goods. In recent decades, innovations have focused on guiding operators in fulfilling orders as fast as possible and using miniload systems, for instance. Now, technology has gone a step further with tools like AMRs.
What is the tote-to-person system?
Tote-to-person, or TTP, is an order picking method where unit loads — namely totes, boxes, bins or small bags — are brought to warehouse pickers automatically. This solution can work with automated storage and retrieval systems (AS/RSs) for boxes or autonomous mobile robots (AMRs), which transport items to humans autonomously. These intralogistics solutions save time, space and other company resources. They enable operators to fulfil more orders in less time by reducing warehouse travel.
The tote-to-person system is one of the latest advancements in order picking. It enhances employee efficiency by allowing operators to focus on their tasks without leaving their pick stations. Likewise, it gives organisations the option to optimise their floor space with vertical storage solutions. Moreover, AMRs are capable of moving freely and coexisting with other machines as well as humans. If they encounter an obstacle, they stop and recalculate their route. They also adapt easily to changes in the layout.
TTP is a goods-to-person strategy with multiple advantages. For example, the warehouse management system (WMS) organises operator tasks, productivity rises in terms of picks per hour and the return on investment is quick, thanks to increased shipments and fewer errors. For seamless integration of tote-to-person, it’s advisable to implement it with the help of experts. Additionally, you’ll want to standardise unit loads so they fit in the automated storage and retrieval systems (AS/RSs). It’s also vital for the AMRs to be robust enough to carry the weight of the totes.
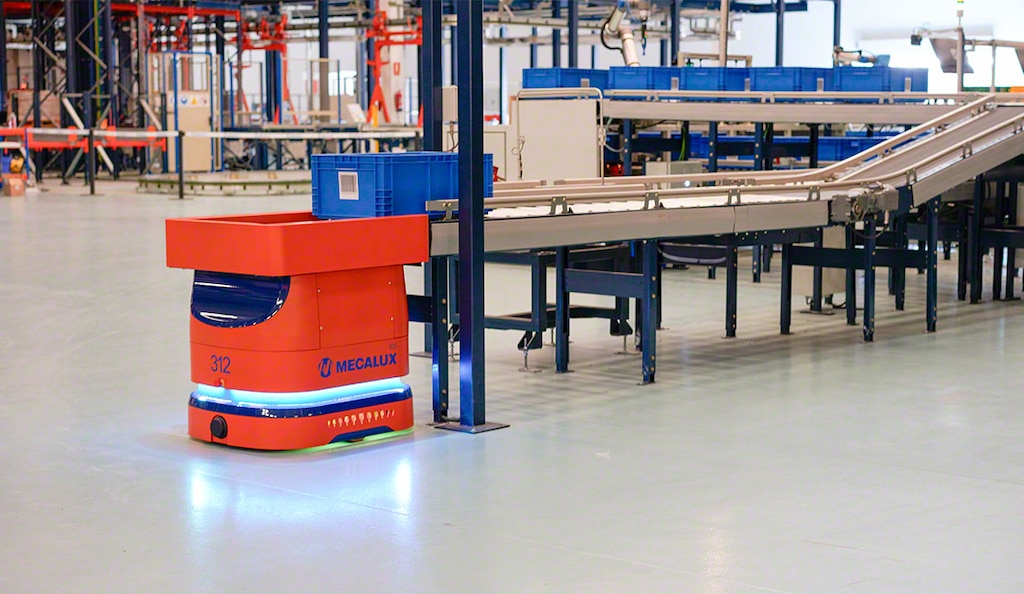
Which software guides the tote-to-person system?
Performing picking with the tote-to-person method saves operators from traveling long distances so they can focus on sorting goods and filling orders. Whether you use an AS/RS or an AMR, you’ll need a program to coordinate operations.
Mecalux’s AS/RSs for boxes use a single software solution. Meanwhile, its AMRs are run simultaneously by three programs with minimal human intervention:
- WMS software. This monitors, coordinates and manages all processes, including SKU location assignment and storage, fulfilment and outbound order shipping. The system sends operators instructions and is used with both AMRs and AS/RSs. It can also organise operations in manual facilities.
- Fleet management software. When performing tote-to-person with AMRs, the fleet manager monitors the robots’ traffic and assigns tasks based on their status and location. This way, the program selects the ideal AMR for each task and indicates the locations of the totes to be moved.
- Navigation software. Each of Mecalux’s AMRs incorporates a program that enables it to determine the most efficient route to follow in the warehouse. They’re capable of moving under racking units, detecting obstacles and stopping. They can even readjust their path, generating a new route to bypass the roadblock and reach their destination.
How does the tote-to-person system work?
Tote-to-person picking can be performed in several ways thanks to the wide variety of AS/RSs for boxes available. Storage units can be transported to operators in the following ways:
- Miniloads. These systems automate operations, handle hundreds of totes per hour and increase the capacity of a conventional storage system by tenfold.
- Box conveyors. Unlike AMRs, which offer greater autonomy, these internal transport devices are static, moving products via rollers, chains or belts. However, they generally operate at higher speeds.
- Shuttle systems. These AS/RSs consist of a shuttle car that inserts and removes goods from their storage locations automatically.
- High-performance pick stations. These solutions are designed to boost order picking significantly. They provide operators with simultaneous access to the greatest possible number of boxes to pick from.
- Picking robots. You also have the option to incorporate collaborative robots (cobots) into tote-to-person picking or even fully automate the process. Pick and place cobots operate entirely autonomously and handle a wide variety of items accurately, regardless of size or texture. The most sophisticated machines can even work with objects they’ve never seen before.
If you prefer to implement tote-to-person with the help of an AMR, the picking process is executed automatically from the receipt of the order. The most suitable robot is sent to the racking to retrieve the tote (box, bin, etc.). Then, it transports the storage unit to the worker to select the products for each order. The cycle is repeated as necessary until the order is fulfilled.
What are the advantages of a tote-to-person system?
Having robots move around the warehouse while people concentrate on their tasks provides multiple advantages:
- Efficiency. AS/RSs and AMRs pick the required items quickly, allowing operators to fill more orders in less time.
- Flexibility. If changes are made to the warehouse layout, AMRs automatically adapt to the new map.
- Optimisation. Solutions such as AMRs and miniload AS/RS offer greater capacity in the same floor space.
- Accuracy. Automating the delivery of goods to pickers decreases the error rate.
- Occupational health and safety. Freeing employees from lifting heavy loads and traveling excessive distances reduces the risk of accidents.
Solutions for speedy picking
Intralogistics solutions have continuously evolved in recent years. And the most competitive organisations are incorporating methods like tote-to-person and cutting-edge technologies in their operations. Are you considering modernising your picking processes, installing an AMR fleet or optimising space in your facility? Don’t hesitate to contact us. At Mecalux, we’ve been specialising in warehousing solutions since 1966. We’ll help you find the one that best fits your company.