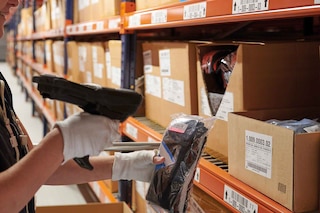
The importance of traceability systems in logistics
The concept of logistics traceability refers to the possibility of identifying the origin and different stages through which a product passes throughout the entire production process, as well as its subsequent logistical distribution until it reaches the end consumer. Therefore, a traceability or system comprises a set of procedures that make it possible to know the location of a product in the supply chain at all times. It also traces the product's route and knows in advance which way it will head.
In our article, we'll explain how it all works and what elements make up logistics traceability systems.
What is traceability in logistics good for? Benefits
Setting up a traceability system involves establishing a direct correlation between the physical flow of goods and the flow of information associated with it.
Logistics traceability systems have multiple benefits for each party involved:
- For companies: it helps them to identify critical points along the supply chain to resolve incidents and boost productivity. Thus, they can reduce problems related to mishandling or contamination of goods by increasing the service quality they offer.
- For consumers: it improves consumer confidence in buying products and services, especially in a global economy with complex domestic and international flows of goods. Moreover, with the rise of e-commerce, goods traceability has moved to the head of the line: it alleviates “package anxiety,” which is suffered by many online shoppers and is connected to the new paradigms of omnichannel logistics and e-logistics.
- For authorities: in key public health sectors such as pharmaceuticals and food, traceability systems are mandatory and have been highly regulated for years.
Types of logistics traceability
ACCORDING TO YOUR TRACKING ADDRESS
1. Reverse traceability
Traceability is used to identify the origin of a particular batch or unit load. It allows you to explore the stages that the product has gone through, from its processing to its final delivery, including the identification of raw materials used and the production operations carried out.
One example of how this type of traceability is applied is when there is a health alert due to food contamination. The aim is to find out where the spoiled batches were produced and withdraw them from the market.
2. Forward traceability
This refers to being able to follow the path that a unit load or batch is going to go down. In this way, you can predict which route it will take and estimate a delivery time. Traceability is widely used to report the stages that the product follows to the final destination in online purchases.
A typical example of forward-traceability is:
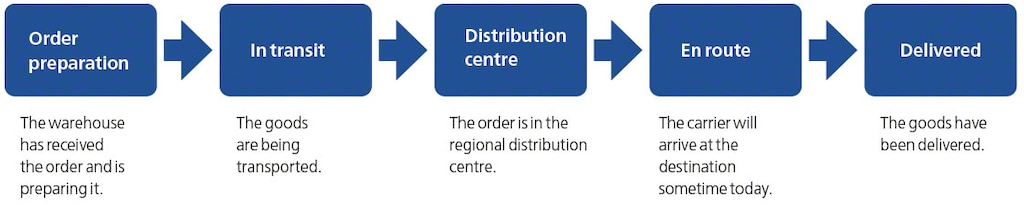
ACCORDING TO YOUR COMPANY’S SIZE
1. In-house traceability
In-house traceability involves the trajectory of products through the company's production chain until they are shipped out. The big challenge for this type of traceability is to detail the process in terms of the delineation, identification and registration of all the movements and handling that the product goes through.
This can prove quite feasible for warehousing thanks to SKU coding and the use of a WMS for inventory management. However, if you take a food producer for example, it must keep a record of each mixture of raw materials and semi-finished products.
2. External traceability
External traceability involves an identification and registration system that covers processes carried out outside a company. It encompasses all links in the supply chain and also extends to transit through different countries (when carried out by outside parties). For this reason, the coding system must be shared by all the agents taking part in the flow of goods. Hence, products should not only have in-house identifiers (such as SKU number).
Components of a product traceability system
1. Formulas for identifying and coding goods
One of the pillars on which logistics traceability is based is the unique identification of unit loads or batches. Integration of this info in the supply chain is only possible thanks to a standardised language shared with all those involved that facilitates automated data recording.
The most widespread systems are:
- Bar code (UPC, EAN): This is the most widespread method of product identification worldwide. This system uses a common language to create unique codes and, thus, identify products, thanks to a series of numbers with their equivalent bars. The GS1 organization establishes coding standards for different types of information linked to each product based on the Global Trade Item Number (GTIN). This number may be supplemented by other numbers adding additional information such as the batch, the Shipment Identification Number (SIN) or the Serial Shipment Container Code (SSCC), etc.
- Radio-frequency identification (RFID): in this case, the RFID tag is capable of transmitting the data autonomously via radio frequency waves. These tags store the product’s information and most activate when they detect a scanner nearby. Their use is not as widespread as that of bar codes and they are more expensive to deploy. However, the main advantage is that they don't require a direct line of sight to extract information, which improves the speed and accuracy of the records.
2. Data capture and recording systems
Once the products have a standard coding system, it is necessary to have data capture devices that serve as a bridge between the physical and the digital world.
These devices gather and record the information they subsequently transmit to the software. They can consist of, for example, bar-code readers, temperature and humidity sensors and RFID antennas or arches. In a warehouse, these systems can also be integrated in inspection checkpoints or in automated systems such as conveyors. Voice picking devices or radio frequency terminals would also fall under this category.
3. Data processing software
The link between the flow of information and the physical movement of goods is only possible thanks to an integrated computer system that brings all the data together, processes them and shares them among all those involved.
This system allows you to:
- Collect and store information related to the product’s movements in a consistent manner.
- Structure the data to make it exploitable.
- Create effective links between the devices and the different players involved in handling the product throughout the supply chain.
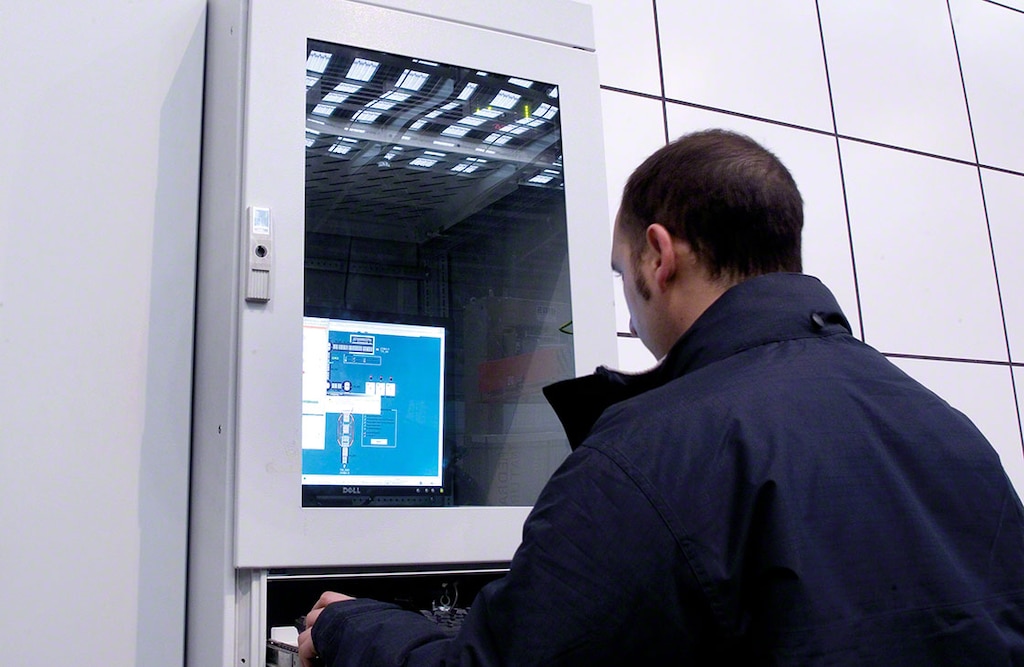
The main types of software used in traceability systems are the following:
- Business management system or ERP: works as an integrative software where different sources of information converge from the main areas of the company; e.g. sales, accounting, production, stock management, human resources, etc. Usually, it is the base system with which every company operates.
- Warehouse Management System (WMS): is a powerful software that optimises all material flows produced in a warehouse. Each phase that a product goes through is registered and communicated to the ERP and other systems with which a company operates.
- Transport Management Systems (TMS): organises and plans distribution routes. Especially in e-commerce shipments, it is usually the software in charge of notifying the customer about traceability issues. For greater process agility, it can be integrated with the WMS to consolidate labelling and information exchange between systems. In the case of Easy WMS from Mecalux, this connection is possible thanks to a module called Multi Carrier Shipping Software.
Traceability systems are designed to improve the goods safety, control risks and ensure the quality of processes and products. If you want to know how Mecalux's specialised software can help properly run a traceability system in your business, don't hesitate to contact us.