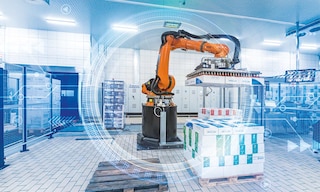
Types of warehouse robots: which are the most common?
The various types of warehouse robots on the market today can meet the needs of any company, regardless of its sector. In a world where businesses strive for greater competitiveness, more and more organisations are equipping their facilities with robotic systems with varying forms and functionalities. According to a report by consulting firm LogisticsIQ, the warehouse automation market is slated to maintain an annual growth rate of 15% until 2027.
What’s a warehouse robot?
A warehouse robot is an autonomous device designed to enhance the flow of goods, safety and operational productivity in a logistics facility. Robots can be fully independent or carry out their functions in collaboration with human operators.
The rise of robotics in logistics stems from the need to achieve a threefold objective: to reduce operational costs, boost warehouse efficiency and improve service quality.
Robots are increasingly gaining ground in several logistics operations: goods receipt, storage, stock management, order processing (picking) and shipping. Why is this? Compared to conventional equipment, warehouse robots ensure maximum throughput: 24/7.
Types of warehouse robots
In logistics, different kinds of robots are employed based on the operations performed, the characteristics of the goods and the desired throughput. These are the main types of warehouse robots:
Storage robots
Stacker cranes — for both boxes (mini-load system) and pallets — are warehouse robots that travel up and down storage aisles to slot and remove products from the racks. Several kinds of stacker cranes stand out for their agility and efficiency, namely single-mast, twin-mast and AS/RS trilateral stacker cranes.
If you require a high number of goods entries and exits in addition to space optimisation, you can install the automated Pallet Shuttle. This high-density storage solution consists of an electric shuttle that moves inside the storage channels, streamlining pallet storage and retrieval.
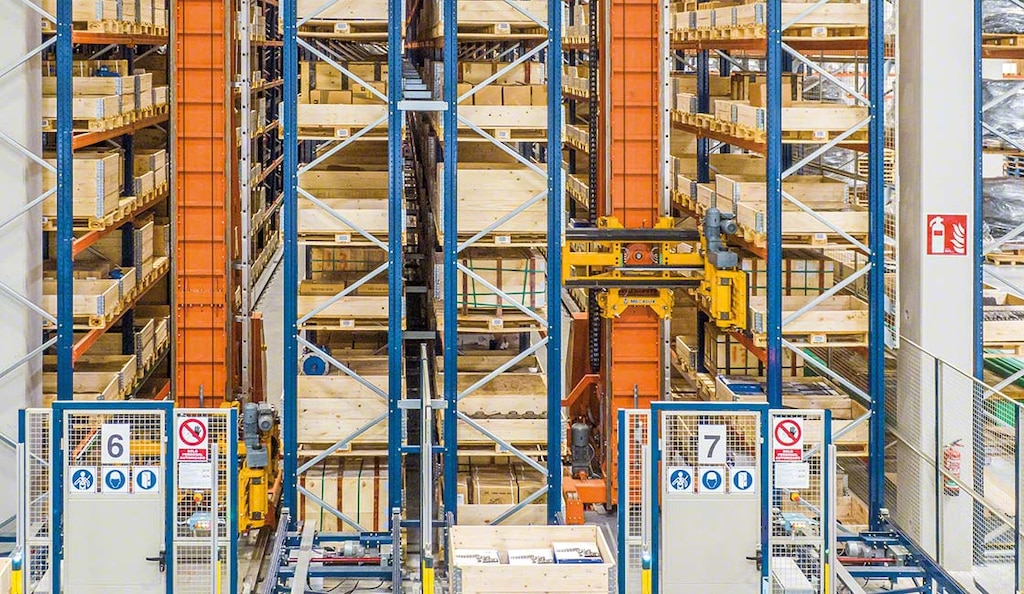
AMRs and AGVs
Autonomous mobile robots (AMRs) are machines equipped with technologies such as AI and machine learning to move around a logistics facility without human intervention. These types of warehouse robots have sensors, software to guide them and digital maps of the facility to interpret their surroundings.
Another internal transport solution for connecting the different areas of a warehouse is automatic guided vehicles (AGVs). The main difference between AMRs and AGVs lies in the navigation system they use. While AGVs travel along a predefined route with laser- or wire-guided systems, AMRs adapt their routes according to the information they receive from their environment in real time.
Picking robots
Picking robots are machines designed to raise productivity and reliability in one of the most demanding processes in a multitude of facilities: order picking.
The most popular picking robots are those with robotic arms that perform pick and place actions. In this operation, the robots select the products, remove them from their slot and put them in a designated location (e.g., in a box that will be used to send a customer order).
Robotic arms help operators in handling heavy loads. These machines are typically equipped with a vision system that enables them to identify items, a gripping element for handling the goods and software programmed to ensure that they operate at full throughput without errors.
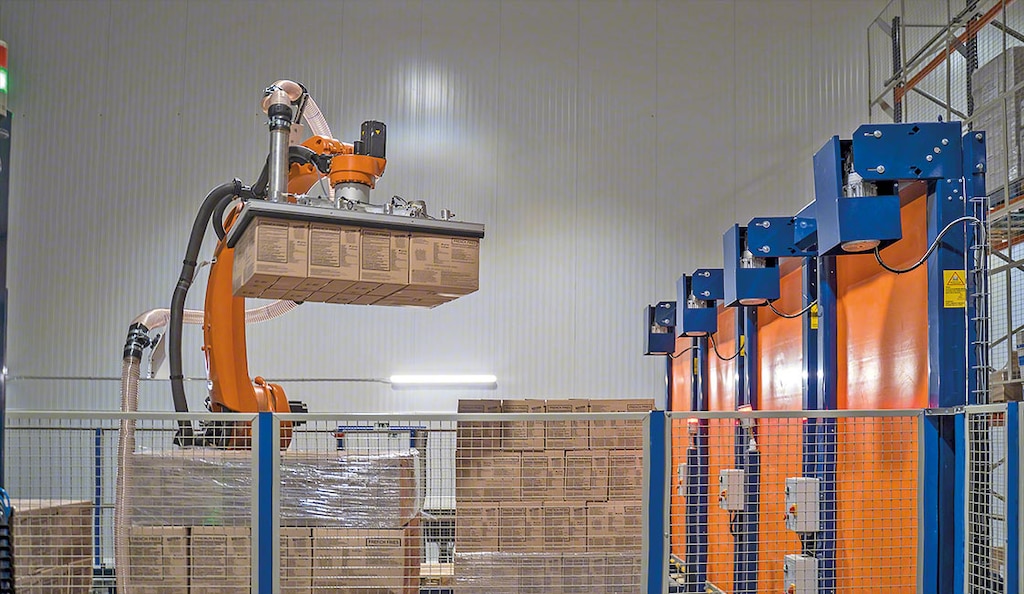
Other types of logistics robots
The market also features other types of warehouse robots, including drones. Also known as unmanned aerial vehicles (UAVs), drones have recently been adopted by the logistics industry on account of their promising capabilities. Tech giants like Google and Amazon are already working on prototypes of drones to deliver orders to customers. This solution would bring advantages such as cost reductions, faster deliveries and a lower environmental impact on road transport. Another application being put into practice in some facilities is drone inventory management to automatically detect stock imbalances, without the need to assign operators to this task.
Cobots are also becoming popular in companies’ logistics operations. Collaborative robots were created to interact with humans to free workers from the most repetitive, complex or hazardous tasks. Their design enables operators to safely interact with the machines, protecting both the worker and the goods.
Finally, warehouse robots that foster the goods-to-person strategy have become a mainstay in logistics facilities. These automated systems move products directly to pick stations, cutting down on operator movement in the warehouse and thus the possibility of errors. With these solutions (conveyors, stacker cranes and transfer cars, primarily), operators don’t have to travel. They merely pick the units indicated from the box or bin they receive at their post.

Warehouse robots: the present and future of logistics
All warehouse operators and managers are aware of the effort and resources required to have an efficient supply chain. Incorporating warehouse robots into logistics facilities raises throughput due to their agility, efficiency and safety in handling goods, all while preventing errors.
Want to make your logistics operations more competitive? Don’t hesitate to contact us. One of our expert consultants will assess your situation and advise you on the best solution for your business.