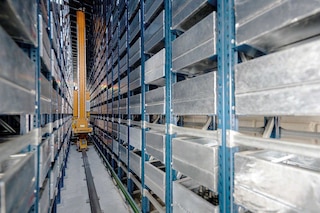
Warehouse control systems: calling the shots
Warehouse control systems (WCSs) play a crucial role in Logistics 4.0. The need to be more efficient and optimize resources has compelled numerous companies to implement the latest technologies in their logistics processes.
In fact, a study by Zebra concludes that over 27% of warehouse managers plan on implementing an automated solution in their installations by 2024. An example of this would be dark warehouses.
Although automation of warehouse operations is increasingly widespread, the implementation of automated systems is impossible without a tool that coordinates the movements of the machines. This software consists of a warehouse control system (WCS).
In this post, we’ll explain its applications and how it integrates with other systems. Plus, we’ll showcase the multiple advantages of installing a WCS in your storage facility.
What’s a warehouse control system?
A WCS is the tool that controls and manages all the automated elements in an installation so as to coordinate all their movements. That is, it oversees the automated handling equipment, such as miniload systems or AS/RS for boxes, stacker cranes for pallets, sorters, and conveyors.
A WCS’s main function is to sync the operation of the various control software programs specific to each of the automated elements. This application is also coordinated with the higher-level systems (WMS and ERP) to fully automate the warehouse.
Advantages of WCSs
Emphasis is usually placed on the benefits of automating an installation, such as improved efficiency or the elimination of errors in complex processes. But what can a WCS do for a warehouse that’s already automated? These are some of its most significant benefits:
- Efficiency in operations: the software coordinates the movements of all the automated equipment in the installation to ensure its effectiveness.
- Maximum throughput: the WCS enables the handling equipment to perform combined product entry and exit cycles, maximizing flow rate.
- Machinery/software integration: incorporating a warehouse control system makes it possible to integrate the operation of the machinery with a higher-level software (a WMS) that establishes criteria and operating rules to adjust to workflows in the installation.
Relationship between the WCS and the WMS
A WCS alone cannot multiply a warehouse’s efficiency. In fact, it requires other software app to transmit information about the installation to it. Thus, the control system makes sure that a machine moves a pallet to its assigned location. But who stipulates that specific location? How are the particular characteristics of each warehouse considered, such as product turnover or the number of operators required per shift?
This is why a warehouse control system needs to be integrated with a warehouse management system (WMS) that syncs operator movements, picking routes, product entry and exit orders and many other processes.
Let’s take a look at an example illustrating the relationship between a WCS and a WMS. Suppose a pallet arrives at the installation. The first step will be to validate the goods. To do so, the pallet will be inserted into the checkpoint. The WCS, by means of the scale and loading gauge control, will verify that it complies with the required measurements. The WMS, meanwhile, will analyze the label information and check to see that the content matches the entry order. Finally, the WMS will send instructions to the WCS for the conveyors and stacker cranes to move the goods to the relevant location.
Easy WCS, the software control from Mecalux
Easy WCS, Mecalux’s control software, serves as the link between the control software for the lower-level equipment and the WMS (in the case of Mecalux’s Easy WMS). Every automated element in a warehouse has its own control program to execute movements. With machinery supplied by Mecalux, these low-level software apps are known as Galileo or PLC (programmable logic controller).
The Galileo and PLC systems require users to program the machines’ every movement. However, to sidestep this tedious, complex operation, companies usually use a WCS, which automates these instructions as directed by the WMS. That is, although Easy WCS isn’t essential, in theory, in practice, it’s actually quite necessary in order for the installation to run smoothly.
In short, the implementation of Easy WCS guarantees that Easy WMS controls the warehouse automatically according to criteria established in advance by the logistics manager. The software, thus, will manage, among other operations, product turnover, the slotting of each SKU, and the type of picking done in the installation.
Automation and digitalization, the cornerstones of Logistics 4.0.
More and more, companies are choosing to automate their processes. In automated installations, a warehouse control system is the key to obtaining maximum productivity and a high number of storage cycles. The result, of course, is greater profit for the business.
Against a backdrop of product diversity, firms have been forced to seek solutions that optimize their logistics resources. And this trend isn’t going anywhere anytime soon. Implementing a warehouse control system maximizes the workflow of the automated elements.
Moreover, in coordination with the WMS, the installation is capable of managing itself: from locating the widest range of SKUs possible to preparing orders without operators, in the case of the most advanced warehouses.
Mecalux specializes in providing logistics solutions tailored to its customers. Digitalization of logistics is a reality, and our various software products ensure that your installations’ productivity and efficiency will increase. Get in touch. One of our expert consultants will advise you on the best solution for your business.