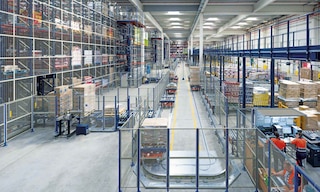
Warehouse setup: definition, types and examples
Warehouse setup is an essential aspect of logistics and supply chain management for any company. A well-designed facility not only boosts operational productivity but also directly impacts cost-effectiveness and customer satisfaction.
To achieve an efficient setup, you need to have a thorough understanding of warehouse layout design principles, types, best practices and applied technologies.
Warehouse setup: the basics
Warehouse setup is the process of strategically organising products, storage systems and equipment in a logistics facility. Ultimately, the setup aims to optimise the arrangement of goods to facilitate the main operations performed: receiving, storage, order picking and shipping.
Objectives of a good setup include reducing lead times, maximising space, minimising operating costs and increasing operator productivity. Your warehouse setup is closely linked to the success of your supply chain: it directly affects how fast orders are filled and sent to customers.
Types of warehouse setups
Logistics facilities can be configured in several ways. Each is tailored to the products it stores and its function within the supply chain. These are some of the most common warehouse setups:
- Transit warehouses house goods temporarily.
- Distribution centres ensure stock availability through their strategic location close to potential customers.
- Manufacturing warehouses, also known as production warehouses, store raw materials and semi-finished goods used to make other products.
- Picking warehouses are specifically dedicated to order processing.
- Consolidation warehouses streamline shipments for companies with large numbers of orders or multiple logistics centres.
Depending on the type of facility and product turnover, the warehouse setup can be characterised primarily by the following:
- Block stacking: similar products are grouped on the floor.
- Racks: materials are stored in these structures.
- Aisles: goods are organised in multiple aisles for easy access.
- Zones: merchandise is assigned to specific areas by category.
Main areas affecting warehouse setup
Generally, you should prioritise these 4 warehouse areas when planning your warehouse setup:
Receiving area
This zone is charged with receiving, inspecting and managing inbound materials or products. It should be positioned strategically, near the main entrance for efficient stock unloading and inspection. Additionally, it should occupy the appropriate space for its intended purpose. It can incorporate a staging area for storing goods temporarily prior to distribution.
The receiving area is typically equipped with loading docks, goods lifts and other devices to help unload and transport materials internally. Products are also inspected in this zone to verify their quality, quantity and condition before being stored.
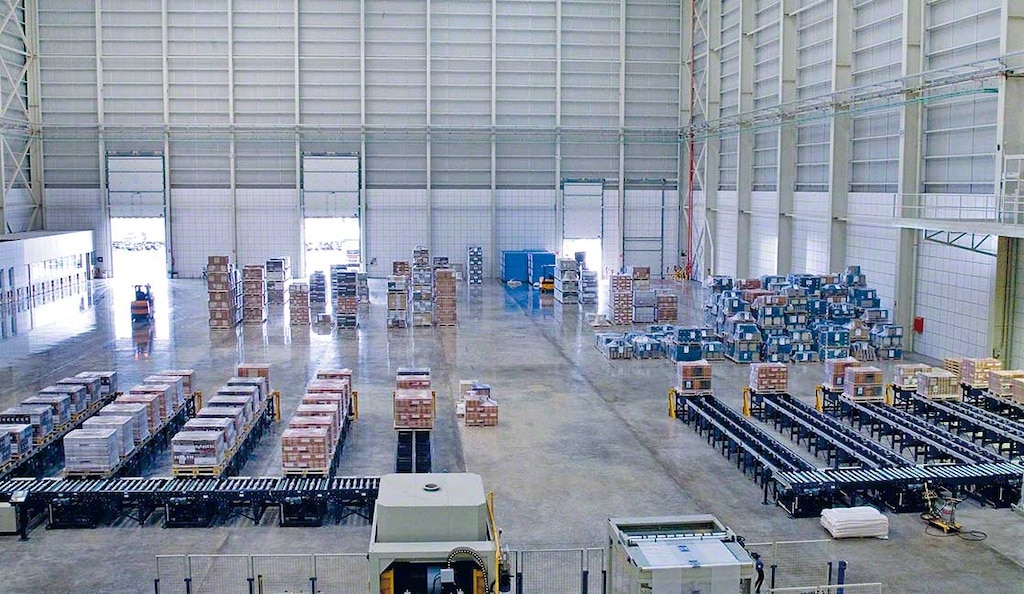
Storage area
This zone is crucial in the warehouse setup and logistics design process, as its organisation directly influences operational efficiency. Your choice of storage system is critical for maximising space and facilitating access to goods. Additionally, storage is often zoned based on the nature of the products, whether perishable, high-turnover or bulk merchandise.
The warehouse setup also takes into account the design of aisles and passageways to enable easy access and safe movement of operators and handling equipment. Lastly, the storage area should be adaptable to fluctuations in demand, the addition of new products and changes in logistics processes.
Picking area
This zone is home to the picking phase of order processing, in which operators fill orders to satisfy customer demand. To perform picking successfully, this area has to be organised to allow operators to move efficiently and comfortably. The setup should minimise pick paths and use ergonomic workstations to reduce fatigue.
Often, a space is created to consolidate picked products prior to packing and shipping. This can help to optimise workflows and eliminate errors. Like the storage zone, the picking area can be designed to adapt to changes in demand, variable order sizes and other factors that can affect the process. A correctly designed picking area contributes significantly towards a warehouse’s overall effectiveness. It bears directly on customer satisfaction by guaranteeing accurate, timely deliveries.
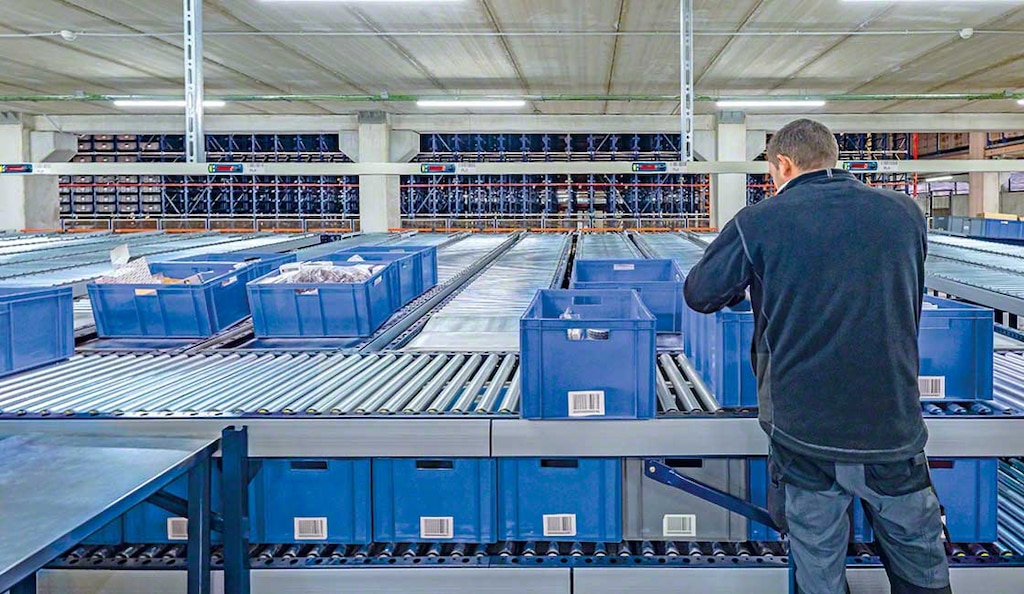
Shipping area
In this zone, orders are sent to their destinations: retail stores, individual customers or any other designated location. This is the last step before products leave the logistics facility.
The shipping area should have a space dedicated to packing. It’s helpful to include workstations equipped with the necessary supplies (e.g., boxes and labels). Likewise, there should be areas for loading lorries or other vehicles. A well-organised shipping area is paramount for ensuring on-time deliveries, thus fostering customer satisfaction and supply chain excellence.
Warehouse setup examples
You can configure your logistics facility’s layout in various ways. Your choice will depend on factors such as product type, stock volume, picking methods and infrastructure. Here are some standard warehouse setups:
- Process-based setup. The logistics facility is organised according to stages such as receiving, storage, picking and shipping. This configuration enables a logical sequence of operations and specific workflow streams. Consequently, items will move seamlessly from receiving to the storage, picking and shipping areas.
- Racking-based setup. This type of layout focuses on the racks and shelves used to store products. It favours access to a wide variety of goods and is popular in facilities with an extensive product catalogue. An example would be an ecommerce centre that handles stock of different sizes and characteristics.
- Setup based on racking blocks/block stacking. In this design, SKUs are housed in large blocks of racking or directly on the floor (block stacking). This type of layout allows operators to locate similar products quickly and facilitates the picking of large numbers of the same item. This configuration can be found in warehouses dealing with fast-moving consumer goods, where substantial volumes of identical products are stored in particular areas.
- Setup based on picking blocks. High-turnover items are grouped in strategic areas to streamline picking. The purpose is to minimise operator pick paths and expedite order fulfilment. This might be seen, for example, in an ecommerce warehouse aiming to accelerate the picking of high-demand products.
- Workstation-based setup. The warehouse is organised around dedicated workstations for tasks like order packaging, labelling and verification. The aim is to enhance efficiency by grouping related activities in specific areas.
Warehouse setup can vary according to the needs of each company. When configuring your facility, remember to consider the type of merchandise you handle, the size of your inventory, picking methods and your available infrastructure.
Warehouse setup for a competitive supply chain
Although an efficient setup offers numerous advantages, it can pose certain challenges. These might include lack of space, complexity in inventory management and adaptation to changes in demand. To overcome these obstacles, it’s advisable to implement advanced technologies, regularly reassess your layout and provide your staff with continuous training.
To sum up, your warehouse setup is a key component for improving operational efficiency and satisfying market demands. Are you looking to upgrade your logistics setup with a layout that combines sound design principles, cutting-edge technologies and best practices? Be sure to get in touch. At Mecalux, we have extensive experience assisting businesses across multiple sectors and product lines.