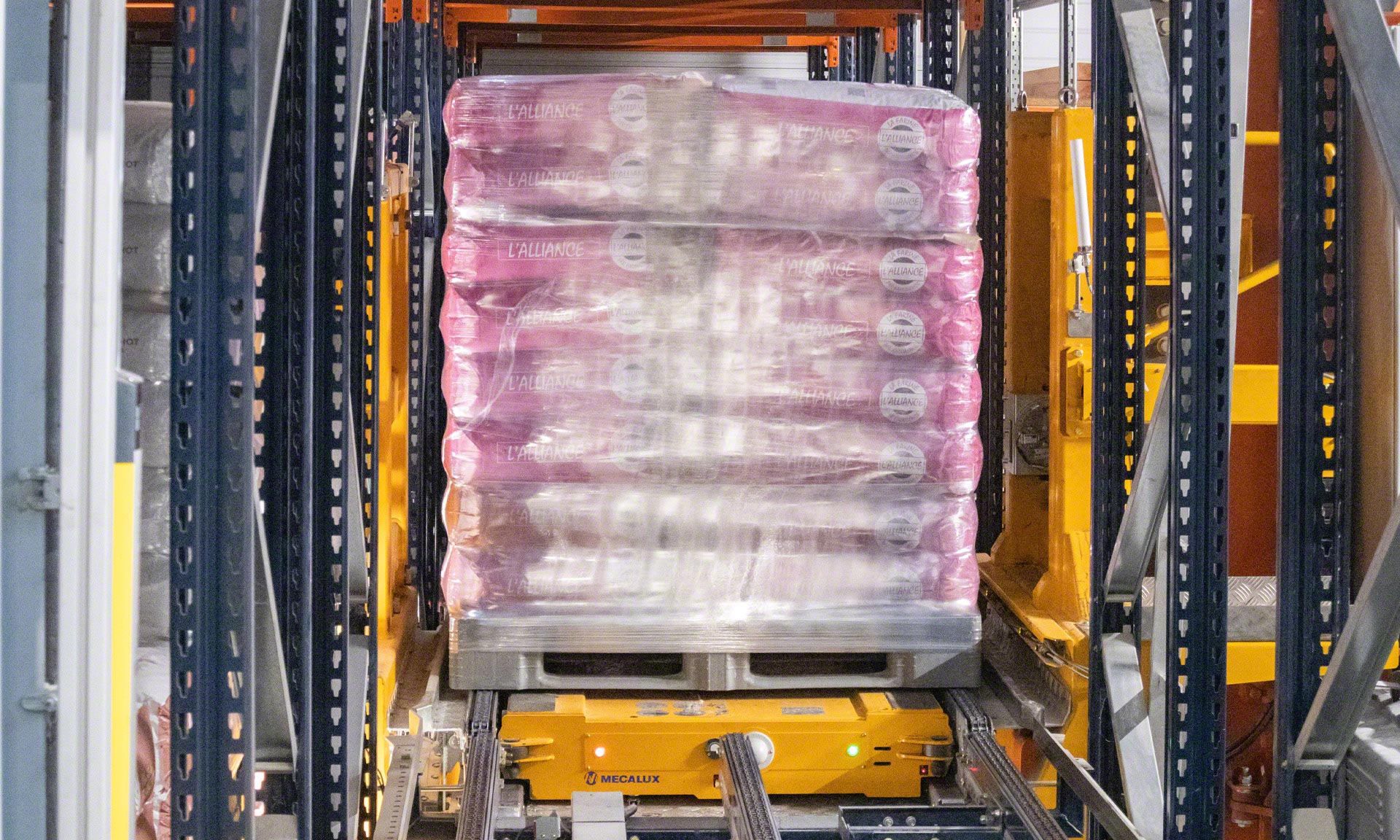
Minoterie Planchot automates its flour warehouse in Saint-Paul-en-Pareds
Flour producer Minoterie Planchot accelerates storage and order fulfilment with the Automated Pallet Shuttle, a picking robot and Easy WMS software.
Renowned French flour producer Minoterie Planchot has digitalised its production plant in Saint-Paul-en-Pareds (France). The company has automated the storage of its finished goods with the Automated Pallet Shuttle system and Easy WMS warehouse management software.
Five generations of millers
Minoterie Planchot, a French family-run business based in the town of Saint-Paul-en-Pareds, specialises in flour production for bread, pastries and other baking applications. It works closely with local farmers, applying sustainable techniques that ensure the quality of its products. Renowned in its sector for its commitment to traceability, Minoterie Planchot offers a wide range of traditional and ecological flours, adapted to the needs of artisan bakers and food-industry professionals. Founded in 1912, Minoterie Planchot produces 110,000 tonnes of flour annually.
CHALLENGES
|
SOLUTIONS
|
BENEFITS
|
---|
With an annual production of 100,000 tonnes of 100% French wheat flour, Minoterie Planchot has positioned itself as a front-runner in France’s flour industry. From its modern plant in Saint-Paul-en-Pareds, the producer supplies artisan bakers, mass retailers and food industry manufacturers.
A 35% increase in production volume and growing SKU diversity led the company to rethink its logistics operations. Yves Fradin, Industrial Manager at Minoterie Planchot, explains what made the business take the leap: “Before, we stored and transported pallets in the warehouse manually. All we had was a floor storage area and basic racking. We needed a solution that would enable us to automatically manage flour sacks arriving from production and speed up order fulfilment of full and mixed pallets.”
Mecalux has accelerated Minoterie Planchot’s logistics operations with an all-in-one solution comprising the Automated Pallet Shuttle, a picking robot and the Easy WMS warehouse management system. “Automation has provided us with numerous advantages, including increased productivity and a significant reduction in manual product handling,” says Fradin.
The throughput offered by these storage systems was crucial in the company’s final decision. “We chose Mecalux as our logistics solutions provider after visiting the warehouse of a business in our sector, where we saw first-hand how well its storage systems performed.”
Productivity and ergonomics
“The main function of the AS/RS is to house finished goods, ingredients and packaging in addition to facilitating order picking,” says Fradin.
The Automated Pallet Shuttle in Minoterie Planchot’s facility stands out for its compact design. This automated storage and retrieval system (AS/RS) consists of a single 30-metre-long aisle and 18-metre-high pallet racking, combining throughput and high capacity in an optimised space. The company can now store 1,189 pallets with flour sacks in just 260 m².
In line with this space maximisation strategy, Mecalux set up product infeed and outfeed stations on the sides of the AS/RS. These have streamlined the supply chain flow without compromising storage capacity.
“We receive and ship around 250 pallets a day,” says Fradin. “Thanks to the AS/RS conveyors, we now carry out 90% of our internal material transport operations without manual intervention. This has reduced physical strain and improved efficiency.”
Another logistics process optimised by automation is the order processing of flour sacks. To perform this operation, Mecalux installed a transfer car to serve as a buffer and a picking robot that loads the sacks automatically, improving ergonomics and productivity. “Automation has cut down on physical strain by 80%. Proof of this is that presently, we fill 85% of orders using the picking robot,” says Fradin. “Every day, we process around 30 orders, which are shipped on 125 pallets to the north-western regions of France and the export market.”
Traceability of 250 SKUs
The Easy WMS management software supervises inbound and outbound product orders, ensuring complete traceability of the 250 SKUs stocked. With this method, Minoterie Planchot strictly monitors each pallet in its warehouse. This facilitates accurate batch identification and monitoring of every SKU, from production to end-customer delivery.
Traceability enables precise, systematic control of the quality of goods received. Equipped with RF scanners, associates inspect items by completing a questionnaire, it covers key points such as the type of load support, the compliance of supplier documents (e.g., the presence of a BIO label), and the availability of samples. With this process now digitalised, goods that do not meet standards can be quickly identified and set aside in a designated area for further handling.
Integrating Easy WMS with Minoterie Planchot’s ERP system has synchronised manufacturing and logistics in real time. Now, the warehouse identifies finished goods arriving from the production plant and is equipped with detailed information on SKUs scheduled to be sent to clients. With data synced between the two systems, the company has enhanced efficiency and shortened order shipment lead times.
A future-forward leap
The comprehensive Mecalux solution has transformed Minoterie Planchot’s logistics operations to efficiently handle the 35% rise in its production pace. By automating critical processes, the flour producer has increased its responsiveness to demand and optimised the logistics management of its 250 SKUs. Traceability, improved ergonomics and greater storage capacity have become key pillars of Minoterie Planchot’s strategy for the future.
Automation has provided us with numerous advantages, including increased productivity and a significant reduction in manual product handling.
Gallery
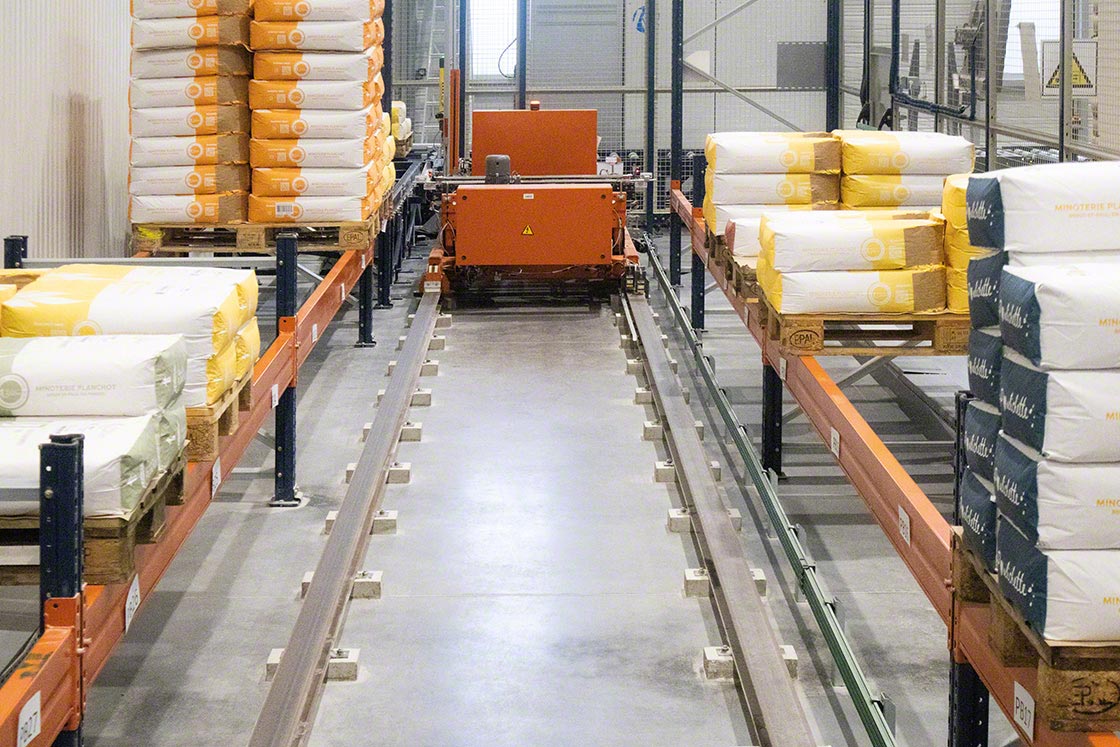
Minoterie Planchot streamlines the internal transport of flour sacks with conveyors
Ask an expert