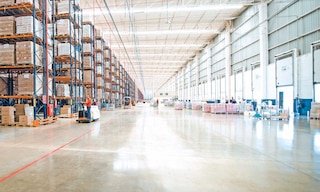
Dock to stock: efficiency starts at the loading dock
How much time do you need to store goods that have just arrived at the warehouse? This process, known as dock to stock, pertains to all operations involved between the receipt and storage of the merchandise. Optimising this is the first step towards having efficient logistics operations.
In this article, we’ll analyse the importance of dock to stock and the phases that make it up. We’ll also explain how to automate this process as much as possible, thus, cutting down on cycle times.
What is dock to stock?
Dock to stock refers to the process that begins when the warehouse receives goods at the loading docks and ends once they have been stored on the racks. This operation encompasses a series of phases that determine the warehouse’s efficiency.
Among them, the most complex is stock management, which includes the validation and inclusion of new products in the inventory. These days, in fact, most installations use a WMS (warehouse management system) to speed up this operation.
But how long should it take a warehouse to store goods on the racks after receiving them? According to data from the American Productivity Quality Center (APQC), the most competent warehouses devote less than four hours to the dock-to-stock process, while other logistics centres need up to 48 hours.
Dock-to-stock procedure
These are the internal operations directly involved from the time a warehouse receives the merchandise at the docks until they are stored on the racks:
- Receipt: lorries carrying goods from production plants or suppliers arrive at the loading docks. The pallets are unloaded from the vehicles and temporarily placed on the floor.
- Goods validation: workers check to ensure that the supplier or production centre has sent the items in the correct quantities and that they are in proper condition. Likewise, they verify that the goods meet the physical specifications stipulated.
- Updating of stock: all materials received must be entered into the warehouse inventory.
- Storage: the goods are placed on the unit load (pallet, box, or container) and deposited in the relevant storage system, taking into account stock turnover criteria.
Any incident or delay in any of the tasks has a negative impact on the dock-to-stock cycle time.
How to cut dock-to-stock cycle times
Reducing the cycle times necessary to complete the dock-to-stock process is fundamental for having an effective supply chain. A number of elements take part across this process and optimising them will improve dock-to-stock throughput. To do this, it’s essential to bear in mind these guidelines:
- Warehouse design: the loading dock area should be prepared to receive lorries quickly and continuously, without the need to wait to be unloaded. It’s also important to define the surface area dedicated to the staging area for placing the pallets on the floor.
- Reduce employee movements: the physical distance travelled by operators as they perform their tasks is directly related to the dock-to-stock cycle time. Centralising and defining the order of receipt tasks helps to optimise internal operator travel time.
- Streamline information management: this is, undoubtedly, the most crucial and labor-intensive operation, as errors occurring at this point affect stock management on a large scale. Implementing a WMS is the best solution for expediting this process.
- Automation: having automatic handling equipment and storage systems decreases the dock-to-stock cycle time. As a matter of fact, all operations involved in this process can be automated.
- Cross-docking: proper inventory management lets you know whether or not a product you’ve just received should be stored. Cross-docking prevents you from wasting time on unnecessary storage tasks.
In general terms, to shorten the dock-to-stock cycle time, it’s critical to carry out good logistics practices, paying attention to all elements involved.
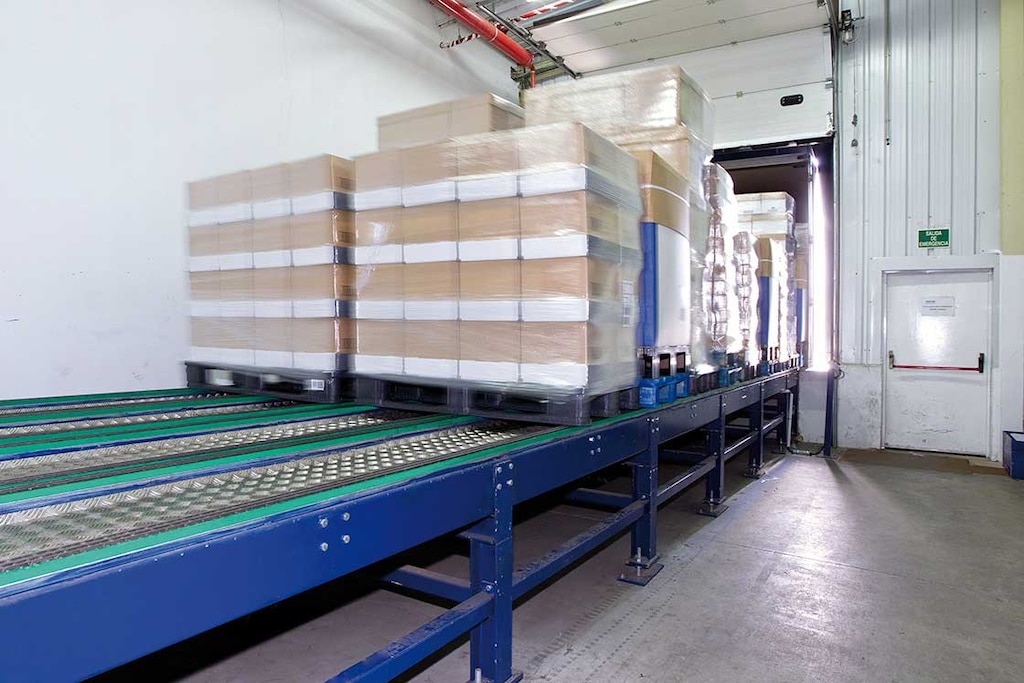
Automated dock to stock
Automated storage systems and handling equipment help to reduce dock-to-stock cycle times as much as possible. Nowadays, this process can be automated from start to finish.
Each company needs to assess, based on its needs, whether it’s more cost-effective to automate all or some operations by means of elements such as automatic unloading platforms, conveyors, checkpoints and/or stacker cranes.
Automation makes it possible for the warehouse to operate 24/7, without interruption. The reduction in errors and, in turn, in costs, is another major advantage. Automation drastically limits mistakes arising from manual handling, thereby ensuring maximum efficiency in all automatic operations. In short, automating dock to stock is one of the most effective solutions for boosting productivity, improving service quality and minimising warehouse operational costs.
Dock-to-stock software
WMSs such as Easy WMS help to increase the throughput of all these operations. In addition to reading and checking all the items, entering them into the inventory and assigning them a location according to turnover strategies, the WMS knows in advance which products will be received (advance shipping notice or ASN).
This way, and, given that the data are already in the system, you can devise goods receipt strategies based on whether the items consist of full containers, multi-SKU items, or even unplanned receipts.
Easy WMS offers several modules that can be used to adapt the software to your logistics requirements, dramatically improving the dock-to-stock process. This is the case of Supply Chain Analytics, which segments and sorts large amounts of daily data to then convert them into useful information. This software creates customised KPIs, for instance: receipts per hour, percentage of damaged merchandise, warehouse occupancy, etc.
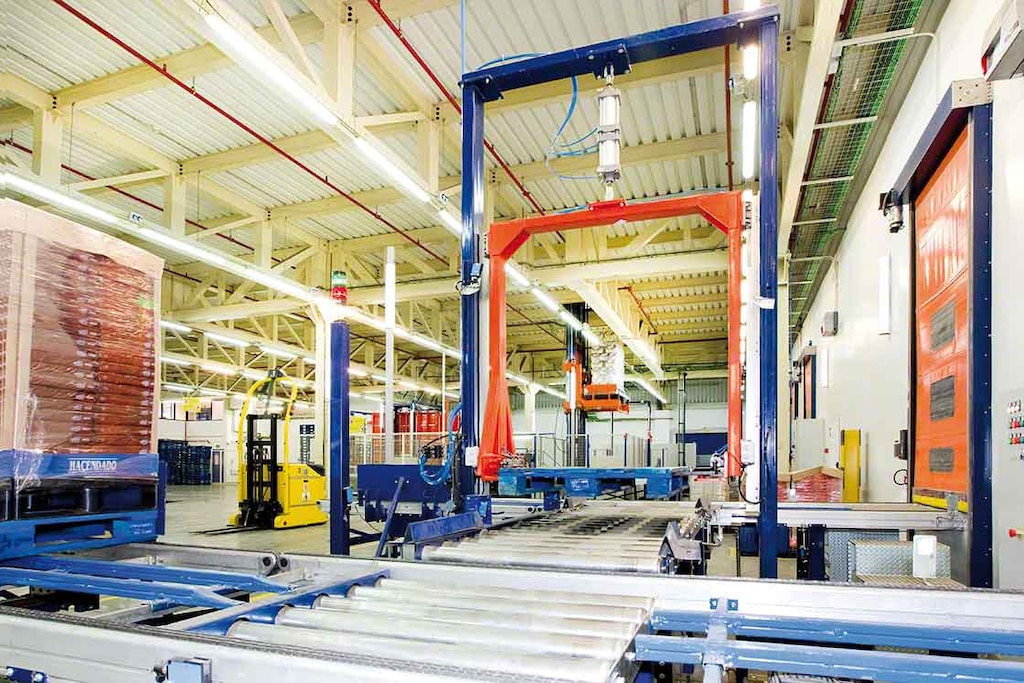
The first step towards an efficient warehouse
Dock to stock is the first logistics challenge a warehouse needs to respond to before carrying out the rest of the operations. It's impossible to prepare orders and dispatch them so that customers receive them on time if, prior to that, there are issues in goods receipt, inventory management and storage tasks.
You can’t build a house from the roof down, just as you can’t successfully deliver orders without efficient goods receipt and storage processes. So, if you’re having issues in terms of communication with suppliers, inventory management, or turnover criteria for storing goods, don’t hesitate to contact Mecalux. We’d be happy to help you optimise your logistics operations.