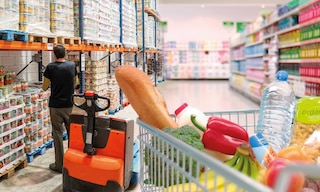
FMCG industry: How to optimise warehouse management
The fast-moving consumer goods (FMCG) industry presents some of today’s greatest logistics challenges due to the rise of e-commerce, supply chain digitalisation and the expansion of omnichannel strategies.
What is the FMCG industry?
The FMCG industry deals with fast-selling products that are low-priced and consumed on a large scale. Used daily by the vast majority of the population, they have a short shelf life due to high consumer demand or short expiry dates. They are purchased frequently, run out quickly and are sold in large quantities. The FMCG industry comprises the companies responsible for manufacturing these commonly used goods.
What is an FMCG product?
Generally, fast-moving consumer goods fall into three main categories:
- Food and beverages. Fresh food, prepared meals, dairy products, baked goods and alcoholic and non-alcoholic beverages are considered FMCGs.
- Personal care and hygiene products. Likewise, soap, shampoo, toothpaste and cosmetics used daily are FMCG industry goods, as are certain popular non-prescription medications like aspirin.
- Cleaning and household products. Detergents, glass and floor cleaners and insecticides are also fast movers.
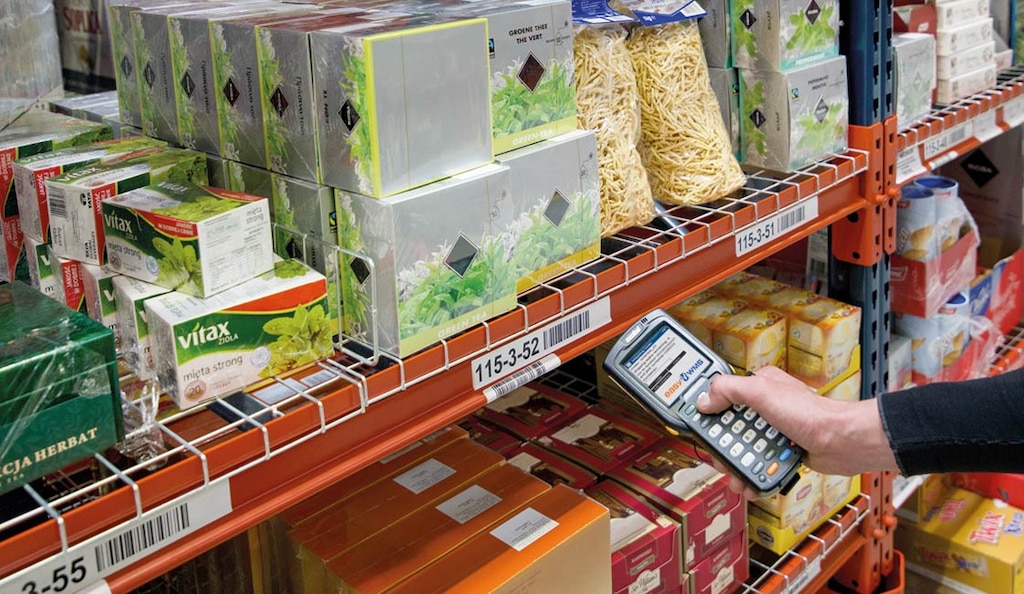
Inventory management in the FMCG industry
Transporting these products to points of sale has always had its share of obstacles. However, against a backdrop of rising e-commerce activity and changing consumer habits, companies need to be light on their feet to remain competitive. These are some of the challenges of FMCG warehouse management:
- High turnover rates. Businesses dealing with food or other FMCGs need to ensure very high turnover. The goal is for products to spend as little time as possible on shelves; to stay fresh, they should be sold every few days. This means they must be easily accessible to expedite order fulfilment.
- Tighter lead times. The high demand for these goods, their perishable nature and growing consumer expectations are driving retailers to offer increasingly shorter shipping times, even same-day delivery.
- Traceability as a requirement. In the FMCG industry, tracking the origin, intermediary steps and destination of each food or medicinal product is crucial. This can be easily achieved with a warehouse management system like Easy WMS.
As a result, many organisations are investing in automation technologies and digital demand forecasting methods to anticipate consumer behaviour and preferences.
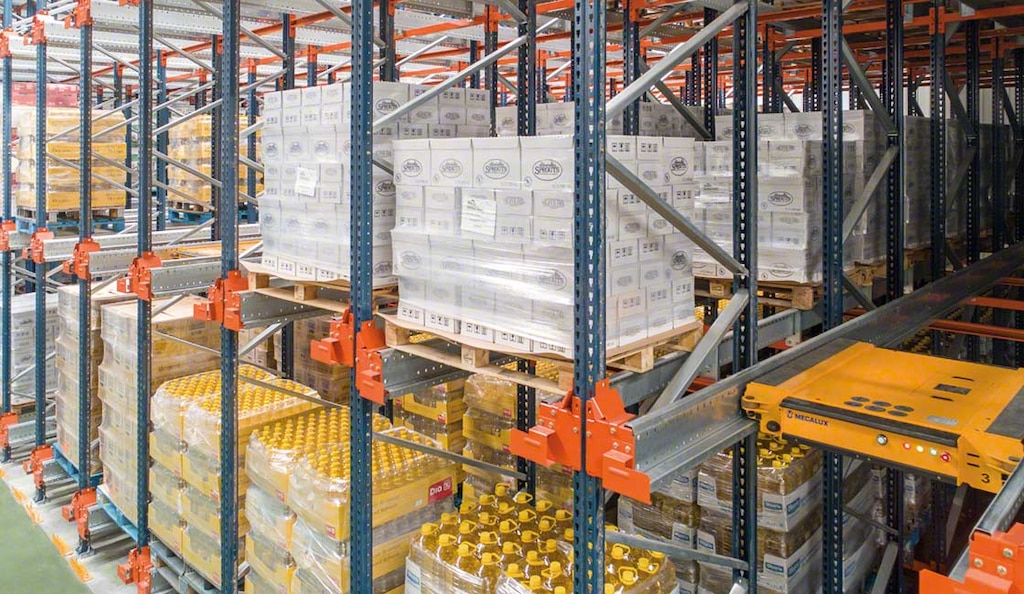
Recommended FMCG warehousing methods
Businesses in the FMCG industry should leverage inventory management techniques such as just-in-time, drop shipping and ABC analysis, which organises stored goods considering their relevance for the company, their value and their turnover. Similarly, it’s advisable to follow the lead of businesses that rely on high-density racking, automated storage and retrieval systems (AS/RSs) and logistics software to streamline FMCG fulfilment and distribution.
- Pallet Shuttle. The high-density Pallet Shuttle storage system is made up of electric shuttles that move along rails to load and unload pallets within storage channels. This solution handles large volumes of goods efficiently and quickly.
- Conveyors. Another FMCG industry staple is conveyors for connecting connect racking systems with loading docks. This strategy enables automatic goods-in/goods-out processes so that warehouse associates can focus on other tasks. Wholesalers like French food and beverage company Firat Food employ this setup.
- Drive-in racking. Green bananas are one of the fastest movers of Argentinian supermarket Coto. To allow easy access to them, the business installed high-density drive-in racks, which provide a high storage capacity for a large number of FMCG products.
- Pallet flow racking. This solution is ideal for high-turnover products such as potatoes and onions. The racks consist of a set of slightly inclined roller channels that enable goods to slide forward by gravity. Pons Químicas, which specialises in household and professional-grade cleaning products, uses pallet flow racks in its manufacturing centre in Jávea (Spain).
- Push-back pallet racking. Medium-turnover products also enter and leave the warehouse throughout the day, albeit at a less intensive pace. Coto stores these types of products (e.g., potatoes, carrots, pumpkins, onions and beets) on push-back racks. When an associate removes a pallet, the ones behind it slide forward by gravity toward the first position, ensuring correct turnover. Italian beverage manufacturer Abafoods installed them in its warehouse in Badia Polesine.
- Pallet racking (selective system). FMCG industry giant Unilever — the multinational behind leading brands such as Axe, Dove, Hellmann’s, Degree, Knorr and TRESemmé — has a massive 67,320m² distribution centre (DC) in Pouso Alegre (Brazil). Outfitted with pallet racking, the facility has a storage capacity of 83,569 pallets.
Optimise your FMCG warehouse operations
Are you looking to enhance your logistics facility to comfortably handle FMCG industry demands? At Mecalux, we can help. As warehouse automation experts, we developed Easy WMS, a management software solution designed to boost your operations. We also offer Easy DOM, an advanced order management system for companies with multiple DCs and omnichannel strategies. Be sure to contact us for expert advice on these and other storage solutions.