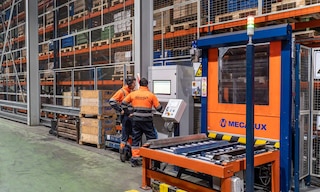
Genchi genbutsu: On-site observation to improve company processes
Genchi genbutsu, a concept rooted in Japanese industry, is based on the belief that sometimes the best way to know what’s happening is to go there and see it for yourself.
What is genchi genbutsu?
Genchi genbutsu is one of the principles of continuous improvement, i.e., kaizen. It contends that to solve a problem, you have to go on-site to assess the situation firsthand. This way, you can understand the seriousness of the incident and take measures to correct it as efficiently as possible. In Japanese, genchi means real place, while genbutsu translates to real thing. Together, they concisely summarise this approach to work.
Ultimately, genchi genbutsu emphasises that it’s best to go and see it for yourself to understand all the implications, verify what occurred and identify the root causes. This method avoids misunderstandings or lack of information, fostering a culture focused on operational excellence.
Origin of genchi genbutsu
This concept was developed by industrial engineer Taiichi Ohno, father of the just-in-time manufacturing system. Ohno believed that beyond reviewing reports and statistics, employees should be fully immersed in processes. Additionally, during the early days, he trained engineers on observation.
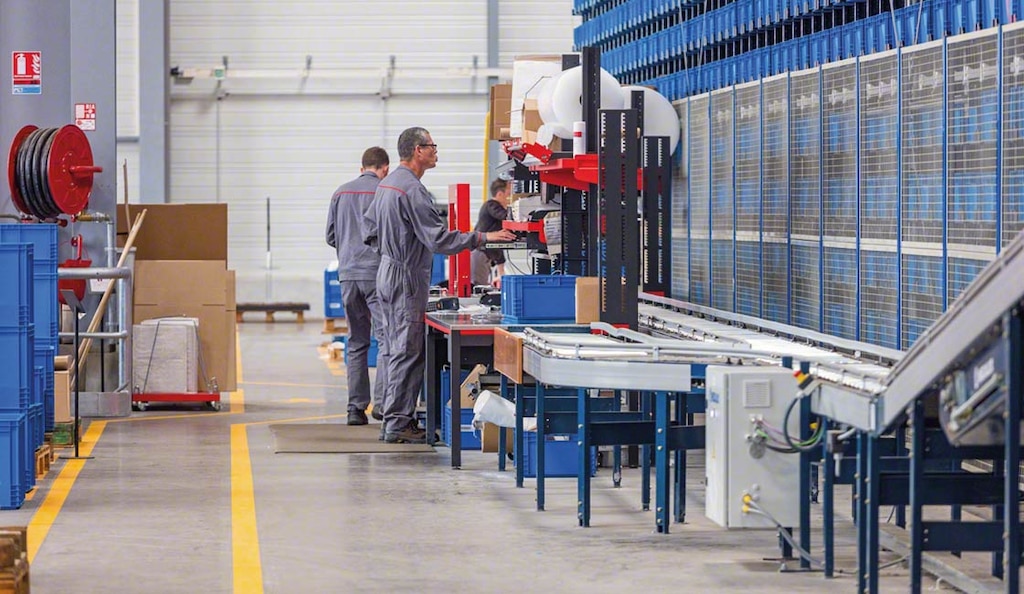
Genchi genbutsu and lean manufacturing
Although it originated in a production plant, genchi genbutsu can be applied to other departments and centres and is useful for analysts, executives and managers alike. Supervisors can visit the plant or office to understand the root cause of a problem. They walk through the area, examine the work environment and gather information on processes and equipment. They can also talk with team members to get their perspective on the issue and inspect machines and devices. The ultimate goal is to find solutions that enhance production and enable the lean supply chain to run smoothly.
Real example of genchi genbutsu
Yuji Yokoya, a chief engineer at Toyota, led the development of the second-generation Sienna minivan. To find out how to make it a popular vehicle, he decided to travel across North America (all 50 US states, Canada and Mexico) with his family. He drove over 85,000 km in the first-generation Sienna and other similar vehicles, observing and exchanging insights with minivan users.
The experience allowed Yokoya to gain firsthand insight into what consumers needed and expected from the product. He noticed that children typically sat in the rear of these vehicles, leading him to implement features that would improve their comfort. After using this information to make some adjustments, sales of the 2004 Sienna were 60% higher than those of the first generation. This model was longer and wider, providing the space and versatility customers were looking for.
Advantages of genchi genbutsu for companies
Following the genchi genbutsu philosophy and going on-site to observe what’s happening offers numerous benefits:
- Firsthand information. Experiencing what happens on the shop floor or in the office provides a more realistic perspective than simply reviewing reports or summaries.
- Holistic approach. Genchi genbutsu helps supervisors understand interactions and relationships between different variables, their causes and their potential effects.
- Troubleshooting. By taking out the guesswork and speculation, genchi genbutsu identifies possible obstacles and bottlenecks and helps implement immediate solutions.
- Greater cooperation. When employees and managers share the same space, it fosters interaction, communication and teamwork, resulting in better coordination, collaboration and constructive feedback.
- Continuous improvement. Genchi genbutsu aims to identify opportunities and take measures to fine-tune processes, products and services. It also encourages reporting issues as they arise, in line with the jidoka approach.
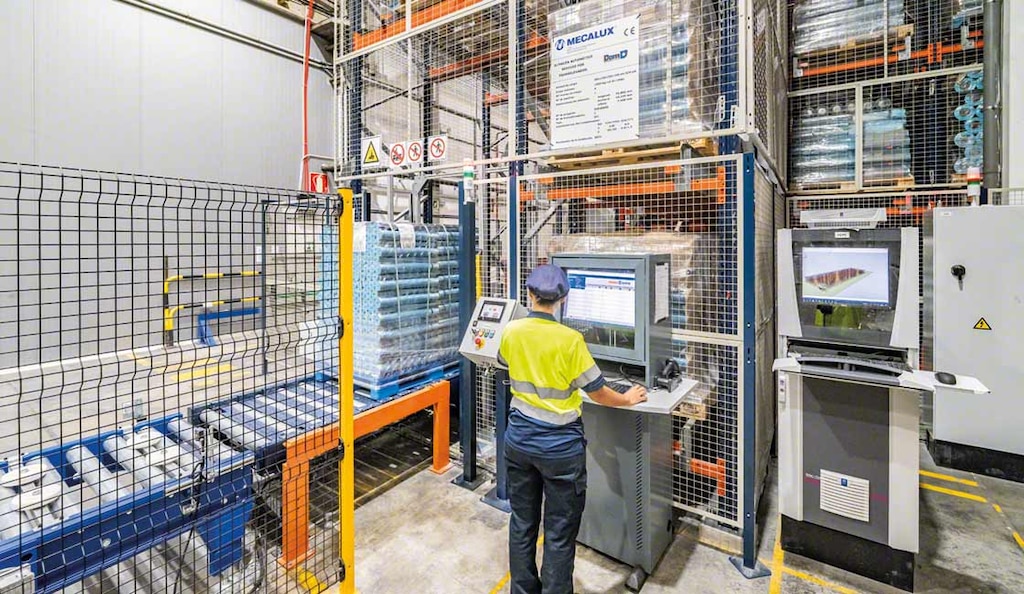
Differences between genchi genbutsu and gemba
Genchi genbutsu is similar to another practice common among senior executives who follow the lean philosophy: gemba or gemba walks.
Despite the name, gemba isn’t limited to walking around a factory. It involves observing day-to-day operations in an organisation’s value-creation epicentre, becoming familiar with its processes, understanding potential issues, promoting continuous improvement and identifying growth opportunities. Its goal is to foster a spirit of problem-solving and excellence among employees while also commending teams when they are successful.
The main difference between genchi genbutsu and gemba is that the former is conducted only when an issue arises. It focuses on investigating the problem on-site to prevent its recurrence. In contrast, gemba emphasises understanding the routines and dynamics where daily activities take place.
Tips for applying genchi genbutsu
To implement genchi genbutsu effectively, it’s advisable to apply these tips when visiting the area where the incident was detected:
- Consider the on-site experience when choosing a solution.
- Take into account the opinions of the operators or employees who carry out the work.
- If necessary, conduct surveys or interviews to resolve discrepancies.
- Check reports and historical data linked to the process.
- Determine whether the cause is human error or equipment failure.
Fine-tune your warehouse with Mecalux
Originally, genchi genbutsu highlighted the need to go to the scene of the incident to understand what happened. However, situations like the Covid-19 pandemic have changed this perspective — even within Toyota. Sakichi Toyoda, CEO of the company and great-grandson of the founder, stated that the definition of genchi genbutsu should be revisited in an era where telecommunications make it possible to collect vast amounts of information remotely.
Are you looking to apply genchi genbutsu to your logistics operations? At Mecalux, we can help. Our Easy WMS warehouse management system provides real-time visibility of processes, while our distributed order management system (Easy DOM) automates order fulfilment for companies with an omnichannel strategy. Feel free to contact us for advice on warehouse IT and storage solutions.