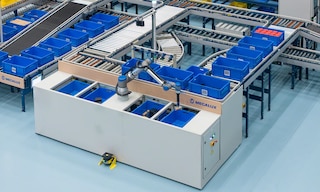
Goods-to-robot: the picking revolution
In the pursuit of continuous improvement, companies turn to automation to improve their speed and accuracy in complex operations like order processing. The purpose of the goods-to-robot method is to enhance picking efficiency in all types of warehouses.
What is goods-to-robot picking?
The term goods-to-robot (GTR or G2R) refers to fully automated order picking with minimal human intervention.
It’s considered an evolution of the goods-to-person system, where a picking robot is integrated to assist with order picking. Aided by computer vision software and a gripping device, these machines autonomously remove products from one box and place them into another.
Automated internal transport systems — e.g., roller conveyors for boxes or autonomous mobile robots — move goods automatically to the high-performance pick station where the robot is installed. Operators used to perform this process manually, with the person-to-goods method. They would travel around the warehouse, locating the SKUs needed to fill orders.
Robotics cuts down on movements in logistics facilities, slashing operational times and raising picking efficiency. By automating the process from start to finish, businesses can expedite order processing and ship more goods in less time.
How does the goods-to-robot method work?
Goods-to-robot involves the complete automation of picking. To implement it, companies will need an automated storage and retrieval system (AS/RS) to house the goods eventually used to put together orders. They’ll also require handling equipment such as stacker cranes or transfer cars to supply the pick stations when necessary.
An AS/RS for boxes is ideal for performing goods-to-robot picking. Why? With these types of solutions, a mini-load stacker crane removes goods from their locations and places them on conveyors. These machines then move the products automatically to the robot at the pick station.
Another common option is the Shuttle System. As opposed to operating with stacker cranes, this variety of AS/RS for boxes works with a transfer car on each level. These devices insert and retrieve bins from their slots, resulting in high-speed product movements.
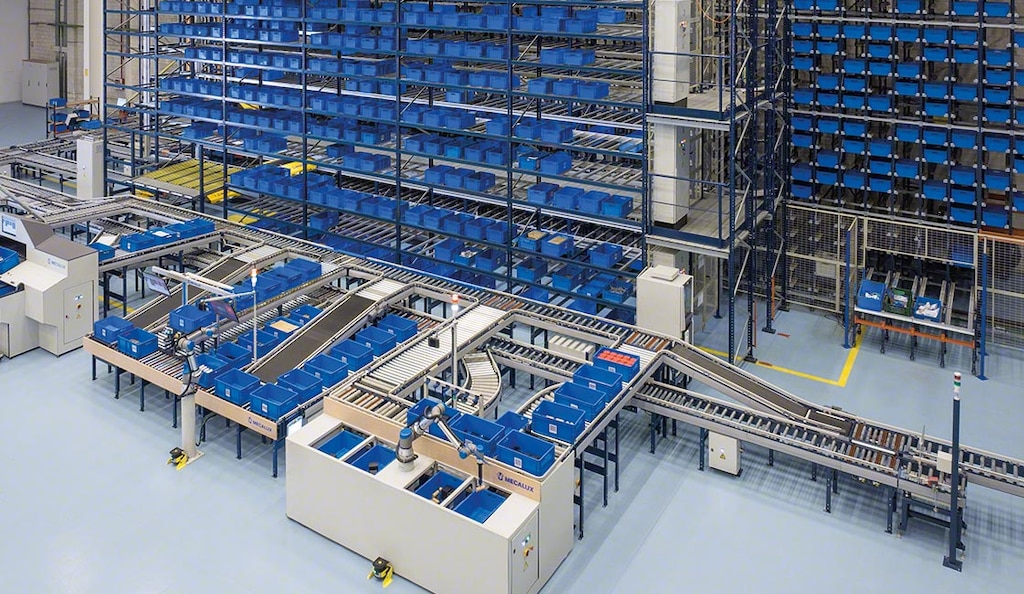
How is goods-to-robot picking carried out?
Goods-to-robot automates order picking by employing robots capable of handling a wide range of items and operating 24/7.
The robots are equipped with a computer vision system specifically designed to identify and classify products. For example, the Mecalux Group’s model, integrated with Siemens’ SIMATIC Robot Pick AI technology, selects the corresponding items and calculates how to effectively retrieve them. These types of robots incorporate a gripping system that can handle a vast array of products.
With the goods-to-robot method, several processes are executed:
- Bin receipt. Conveyors transport the goods needed to fill orders to the pick station where the robot is located.
- Product visualisation. A high-resolution camera captures an image of the items inside the tote. The vision software analyses the image and identifies the best way to pick the SKUs.
- Item removal. Depending on the type of product, the robot automatically changes the gripping system to safely remove goods from inside the bins.
- Merchandise placement. The robot picks the item from the tote and places it inside the corresponding order box.
The goods-to-robot system doesn’t just boost picking — it impacts other warehouse processes as well. Automation improves reliability and efficiency across the supply chain.
Advantages of goods-to-robot
The goods-to-robot method offers a number of benefits. These include:
- Increased productivity. Robots are designed to enhance operational efficiency by shortening response times and ramping up picking speed.
- Nonstop operations. Robots can work 24/7, processing a greater number of orders in the shortest possible time.
- Higher precision. Thanks to computer vision and their grip system, robots move products safely and accurately.
- Flexibility. Goods-to-robot systems cater to a multitude of needs. They can handle different types of SKUs for companies from any sector.
- Adaptation to Industry 4.0. The integration of advanced technologies like robots, the Internet of Things and artificial intelligence helps optimise manufacturing and logistics processes.
Although automation requires an initial investment, it leads to substantial long-term cost savings for companies. Ultimately, fulfilling orders with robots increases productivity. It results in uninterrupted operations, greater reliability and fewer errors.
Efficient picking
Goods-to-robot represents a major leap towards continuous improvement and supply chain efficiency. It marks an evolution in order fulfilment, transitioning from the traditional person-to-goods method. The integration of robots capable of handling an extensive range of products is made possible through their computer vision system and automatic gripping mechanism.
Robotic picking translates into excellent agility and smooth operations in all kinds of warehouses. It minimises manual movements and potential errors. The Mecalux Group’s picking robot raises order fulfilment productivity through precise, round-the-clock operations. Are you looking to modernise your logistics processes in line with Industry 4.0? Be sure to contact us. One of our experts will analyse your supply chain so you can unlock its potential.