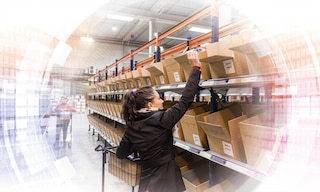
Pick-to-box and how to optimise it
The pick-to-box method simplifies order fulfilment by simultaneously combining the picking, consolidation and packing processes.
In facilities that employ pick-to-box, it’s best to implement a warehouse management system (WMS) that automates decision-making in picking. This logistics software organises operator tasks and boosts productivity in order processing: it designs efficient pick paths, reduces error rates and enables real-time inventory management.
What does pick-to-box mean?
Pick-to-box is an order picking technique that consists of retrieving goods from their locations and consolidating several orders at the same time. That is, operators place products directly in the boxes that will be sent to end customers. With this method, three processes are carried out at once: order picking, consolidation and packing.
In facilities that fulfil orders manually, operators travel around the warehouse with picking carts where they place the merchandise in the packages or cardboard boxes that will eventually be delivered to customers. This reduces the number of movements operators make in the picking phase, increasing their throughput.
Pick-to-box shouldn’t be confused with batch picking. With this technique, operators use a cart to pick items for various orders. But instead of sorting them directly in the cart, they bring them to a conditioning area, where they’re then organised and consolidated separately.
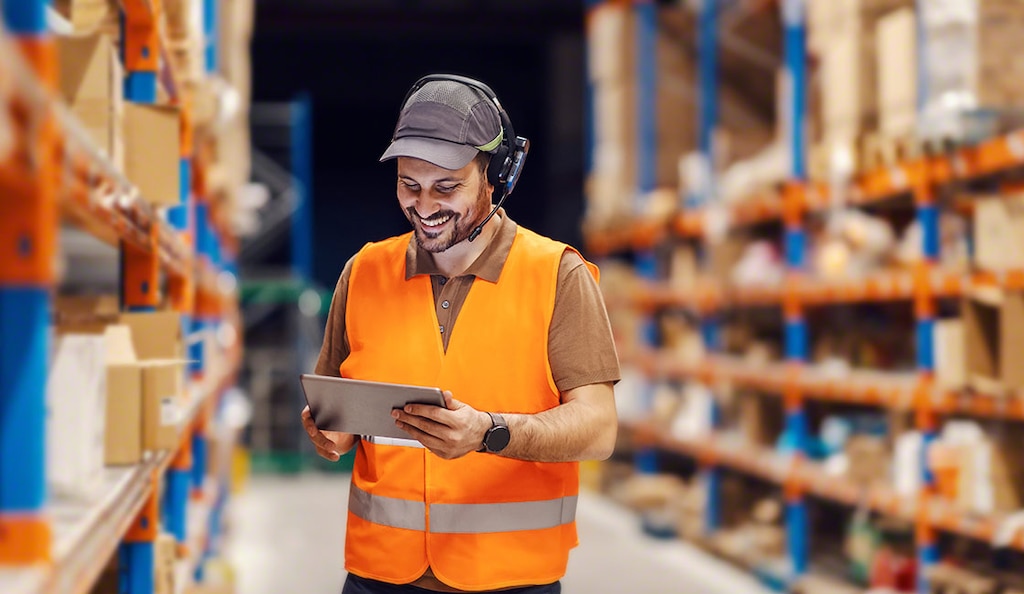
How do you organise pick-to-box?
Although pick-to-box is an efficient order picking method, it does require prior planning. The logistics manager must calculate in advance the number and size of the packages to be sent to end customers and assign the necessary picking carts.
In warehouses that don’t have logistics software, the manager has to calculate how many packages each operator can handle and determine order processing priorities at any given time.
Managers also have to establish pick paths that maximise efficiency in pick-to-box. However, the complexity of decision-making and the risk of error in order fulfilment are driving companies to digitalise picking management.
Software for efficient pick-to-box operations
For most businesses, order picking tends to be one of the costliest processes. Implementing a WMS can ramp up warehouse throughput by leaps and bounds.
This program automates the assignment of storage locations, facilitating picking. Based on a set of rules and criteria that the logistics manager sets in advance, the WMS determines the optimal location for each item. The most advanced logistics programs — e.g., Warehouse Slotting Software ― have functionalities that analyse each product’s historical demand and optimise the distribution of stock to make picking more productive. This type of program is essential for the pick-to-box technique, as it makes it possible to group goods that are normally ordered together, eliminating unnecessary picker travel through the facility.
Warehouses run with a WMS generally employ picking assistance technology such as RF scanners and pick-to-light systems. Connected to the WMS software, these devices guide operators as they fill orders, telling them step-by-step which tasks to carry out at every turn. The pick-to-box method also promotes the implementation of other order fulfilment technology such as pick by voice. This system frees up the hands of pickers, who receive instructions from the software via wireless headsets.
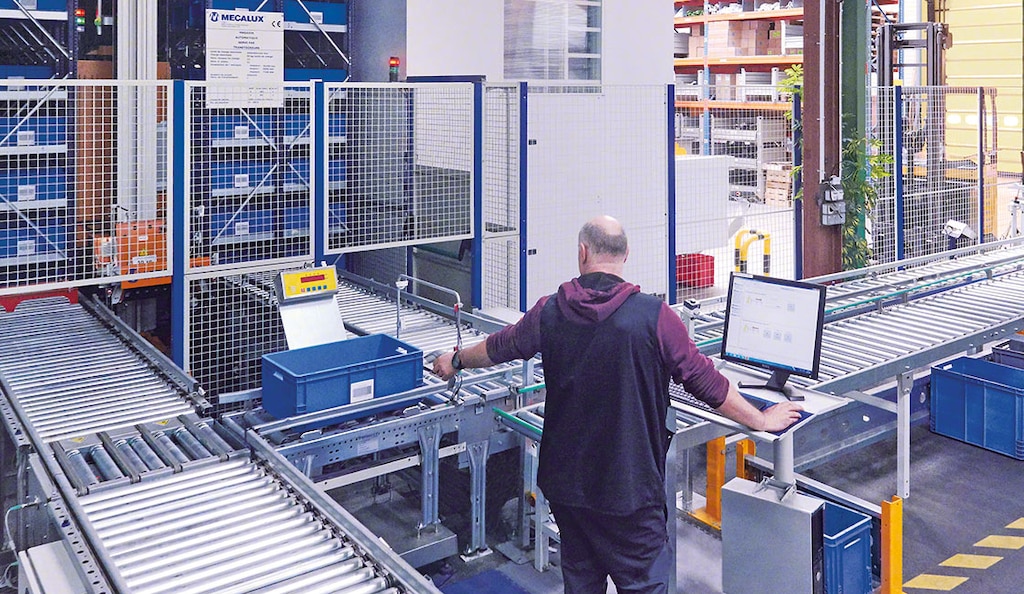
Automated solutions for pick-to-box
Companies that perform large-scale order picking can deploy automated solutions to foster the goods-to-person approach. With this picking technique, operators receive the merchandise by means of automatic equipment.
Part of the pick-to-box operation can be automated, replacing picking carts with a box conveyor. In this pick-to-box mode, operators remove items from the shelving and place them in the boxes that circulate through the automated system. Box conveyors move the picked orders to the shipping area, where they are directly distributed to customers.
The automated solution transports the goods through the facility in a fully autonomous way, limiting operator movements and streamlining picking tasks.
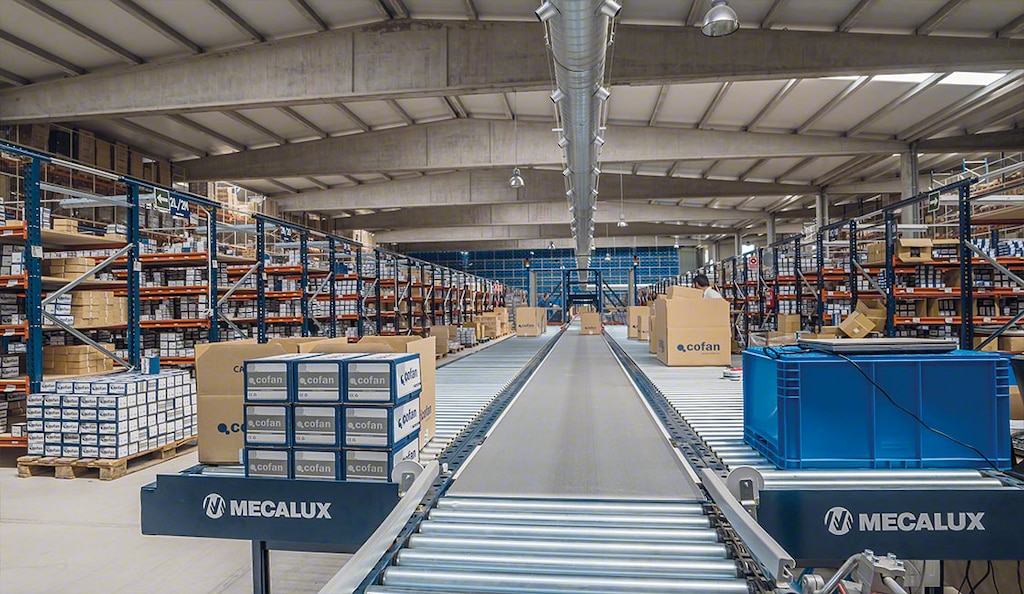
Pick-to-box for faster order picking
Before choosing a specific picking method for your warehouse, it’s important to analyse variables such as product type, number of orders and shipping frequency. To raise picking throughput in your logistics facility, you can choose from a wide variety of approaches. When applied optimally, pick-to-box speeds up order fulfilment by combining the picking, consolidation and packing processes. Nevertheless, due to the complexity of logistics operations nowadays — characterised by many orders with few product units — more and more businesses are relying on automated and digital solutions to minimise the risk of error.
At Mecalux, we have extensive experience in designing and implementing picking systems that maximise warehouse throughput. If you’re looking to enhance the performance of your picking operations, be sure to get in touch. One of our expert consultants will advise you on the best solution for your company.