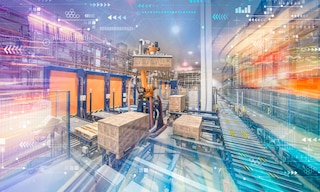
5 robotics applications in logistics
Robotics applications in logistics demonstrate that the industry is going through an unprecedented period of expansion and transformation.
In an increasingly demanding market characterised by extremely short lead times, companies are looking for solutions that streamline processes and enable them to provide optimal customer service. Supply chain automation can help businesses simplify their operations and fulfil orders more quickly.
What’s robotics in logistics?
Robotics in logistics consists of introducing automated solutions in your supply chain processes. The goal? To increase flows of goods, maximise product safety and enhance your warehouse’s performance.
The potential of robotics in logistics is unquestionable: automatic handling equipment makes for reliable, efficient, accurate and flexible operations. The latest technological advances have fostered the development of new robotics applications in several logistics processes.
Robotics applications in industry and logistics
Technological innovation in warehousing has led companies to explore new ways to optimise their processes:
1. Product storage
One of the most common robotics applications in logistics facilities is the warehousing of goods. Automation of storage tasks involves the use of cutting-edge technologies to execute movements in the facility.
Stacker cranes — for both pallets and boxes — are a type of automatic handling equipment that replaces forklifts. These machines insert unit loads in their locations quickly and autonomously. They pick up the products on one end of the storage aisle and move them to the corresponding position. Likewise, they retrieve materials from the racks and transport them to a pick and deposit (P&D) station or an outgoing conveyor, following instructions from the warehouse management system (WMS).
So, what benefits do storage robots have? Among others, 24/7 operations, a higher number of goods-in/goods-out cycles per hour and fewer errors in product slotting and retrieval. By automating storage tasks, all product movements are computerised. Therefore, you’ll know the status of your available merchandise and of goods entering and exiting the facility.
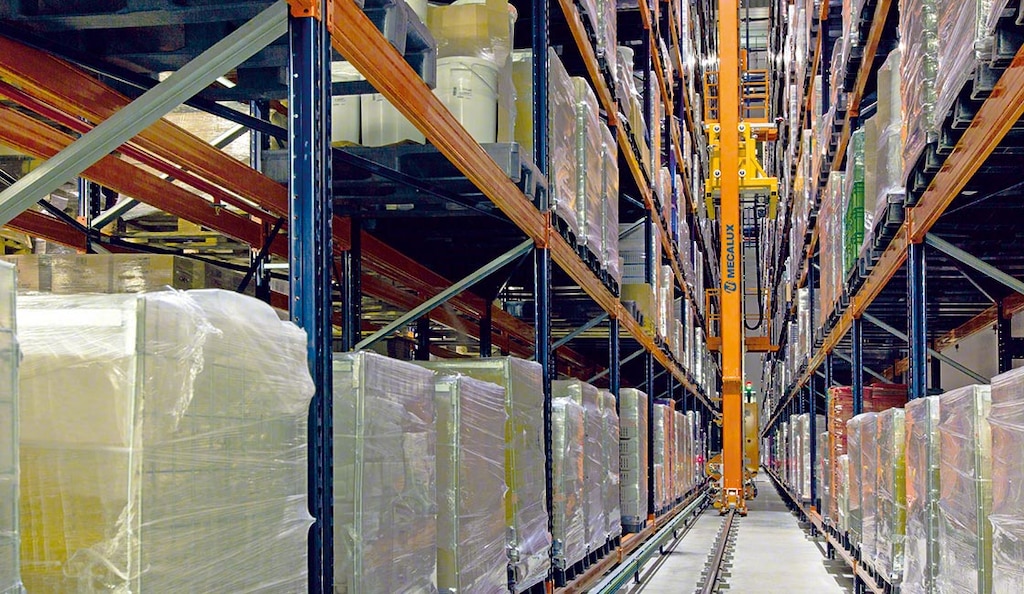
2. Internal transport of materials
The movement of goods disrupts the activity of both handling equipment and operators, who spend a significant amount of their time on these tasks.
Another valuable robotics application for high-throughput facilities is the automation of internal product movements. On-site transport systems such as pallet conveyors, electrified monorails, automated guided vehicles and autonomous mobile robots (AMRs) move large volumes of goods.
Of all the internal transport solutions on the market, conveyors — for both pallets and boxes — are the most widespread in warehousing. They’re used in distribution centres to move items between the areas of the facility, reducing costs and ensuring faster deliveries.
One of the most promising conveyance systems is AMRs. These devices can perform tasks and move around the warehouse without the need for human guidance. According to consulting firm Grand View Research, the global AMR market size “is expected to expand at a compound annual growth rate (CAGR) of 15.5% from 2023 to 2030.” These robots connect the different zones of a warehouse, logistics facility, or production centre, moving goods to the working areas as required by the operations.
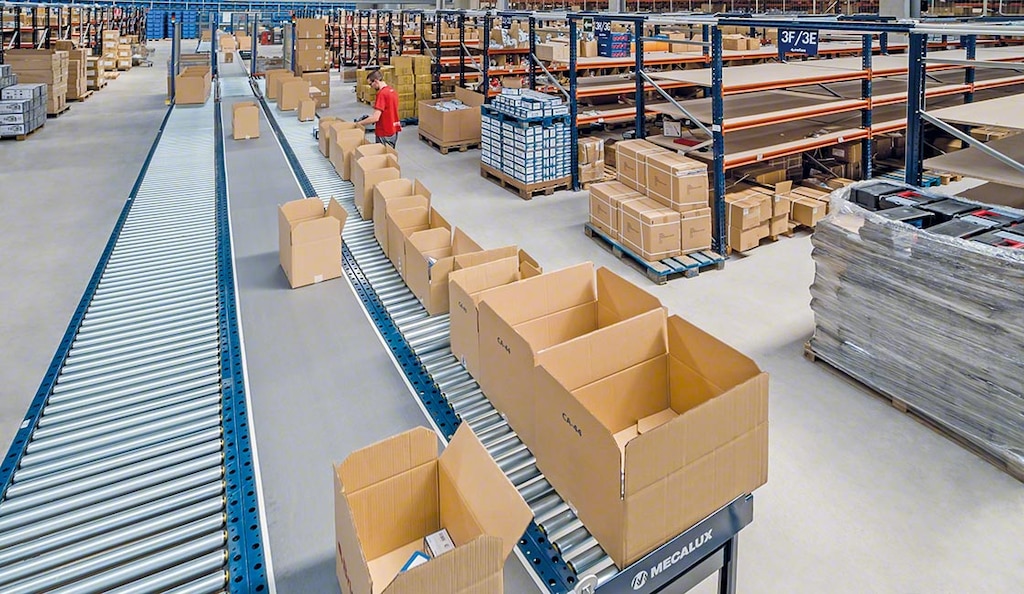
3. Order picking
Order processing is one of the costliest and most complicated operations in any warehouse. And robotics facilitates and streamlines picking through the goods-to-person method. With this picking strategy, automated systems bring the products to the operators so that they can put together orders without having to travel.
One of the most effective goods-to-person robotics applications is the Shuttle System. The transfer cars, lifts and conveyors integrated into this automated storage and retrieval system (AS/RS) for boxes supply workstations with the merchandise required to fill orders.
Companies with large numbers of orders can also rely on robotic arms, programmable devices that simulate or replace human arms during production and logistics operations. These arms can handle heavier loads faster and without tiring. As they operate with full autonomy, these robots are ideal in temperature-controlled facilities.
4. Truck loading/unloading
Businesses can robotise the incoming and outgoing flow of goods in their warehouses with automatic truck loading and unloading systems.
Also known as automatic truck loading systems (ATLS), this solution automates the movement of pallets on and off trucks. It incorporates rollers or chains, extendable forks and skids to move materials with minimal operator intervention.
This solution boosts productivity since loading and unloading is carried out in a matter of minutes. Moreover, automation prevents brusque movements of merchandise, minimising potential damage to products.
5. Autonomous distribution
You can also implement robotics applications in the final step of logistics: the shipment of products to end customers. Autonomous order distribution using robots or drones could take off in the near future.
Companies like Amazon and Google are developing projects related to autonomous order distribution with drones. The advantages of this solution are evident: traffic congestion relief, less pollution and access to remote areas. Will we really see drones delivering orders to our homes within a few years?
According to Yeming Gong, Head of the Artificial Intelligence in Management Institute (Emlyon Business School, France), “drone-based inventory management is already being implemented in warehouses and some drones are even used in 3D-order picking — they fly through the facility to pick the required items. Although today these are just experiments, they’ll probably become popular one day.”
Robotics applications to transform logistics
Robotics has a major presence in the supply chain, optimising operations and assisting companies in meeting their customers’ changing needs. Robotics applications such as stacker cranes, AMRs, picking arms and conveyors expedite the flow of goods in logistics facilities, streamlining storage tasks and maximising operational efficiency and safety.
In the face of the challenges posed by Logistics 4.0, robotics stands as a remarkably effective solution for productive warehouses. At Mecalux, we design and implement automated systems to meet any logistics need. Get in touch and we’ll show you how you can modernise your supply chain.