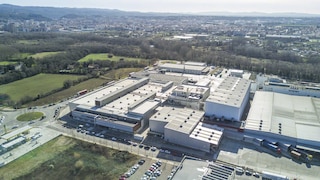
Smart factories: the way of the future
Smart factories have come to play a leading role in the supply chain. Rapid technological progress, competitive pressure, the fragmentation of demand and production on a global level have sped up the transformation of factories, which are becoming increasingly smarter, thanks to automation and digitalisation.
In fact, 86% of manufacturers think that the ability to convert conventional production plants into smart factories will be decisive for improving their competitiveness, according to the Smart Factory Study by Deloitte and MAPI (Manufacturer's Alliance for Productivity and Innovation).
What features do these smart factories have? How do they relate to the rest of the links in the supply chain? We’ll analyse this below.
What are smart factories?
The concept of smart factory refers to the implementation of the latest automation techniques and to the use of digital systems in controlling and executing industrial production. Smart factories manage large amounts of data from both sensors integrated into the machines and the various software programs that coordinate the operations taking place inside and outside of the production centre.
The objective is to gain in productivity while limiting the need for continuous human supervision. The most advanced smart factories have to be able to adapt their production to changing demand, respond swiftly to the requirements of the supply chain and correct deviations in processes to prevent technical downtime. This is achieved through big data mining and the integration of technologies such as IIoT (Industrial Internet of Things) sensors and of digital simulation, such as digital twins.
Hallmarks of smart factories: advantages
Smart factories represent a step forward in the management of production operations. Smart factories are characterised by:
- Flexible and agile manufacturing
Redesigning the production line and altering the functioning of industrial machinery have a significant financial and operational impact. Therefore, these are complex decisions requiring in-depth analysis and testing so as not to make any missteps.
The agility of smart factories to adjust processes is explained by the systematic use of tools such as digital twins. This type of software makes it possible to simulate new production processes digitally and verify their effectiveness before starting them up physically.
In the same way, 3D printing is facilitating the rapid development of product prototypes and modifications prior to their definitive manufacture on a large scale. Thus, technology enables the diversification of production tasks while minimising risks.
- Smart automation solutions
To understand the adaptability of smart factories, we need to consider the automated systems that support it, in addition to the aforementioned digital technologies. In smart manufacturing, industrial machinery has gone from being a rigid system that executes limited movements to comprising much more versatile systems that interact with their surroundings. This would be the case, for example, of the implementation of cobots (collaborative robots) or mobile robots in manufacturing tasks.
On the other hand, in smart factories, control tools monitor production across the board, collecting data in real time through all kinds of sensors. This information serves to optimise processes. For example, it allows you to adjust as much as possible the amount of raw materials used and to save energy by making machinery movements more efficient.
- Safer, more efficient processes
Industrial automation minimises human intervention, thereby reducing the incidence of injuries and musculoskeletal disorders in workers. In addition, the machinery is equipped with advanced sensors and safety protocols that prevent risks to staff.
Smart factories likewise have detailed industrial preventive maintenance plans that aim to limit the number of technical stoppages during the manufacturing process. In fact, this field is one of the most promising for the development of machine learning applications, as failures and breakdowns compromise efficiency and prolong production times.
- The use of data for decision-making
Smart factories have a greater capacity for extracting information from the real world and working with it in a digital environment. These installations don’t operate in a vacuum: they share and analyse more data, thanks to integration between systems (the MES, ERP and WMS, primarily) and the high degree of specialisation of each of them.
Consequently, smart factories are characterised by increased process control and the generation of relevant technical knowledge that’s extremely useful for strategic decision-making.
Relationship between the warehouse and the smart factory
The competitive advantages offered by smart factories run the risk of falling by the wayside if they don’t have the support of an ally in the pursuit of efficiency: the warehouse. How can you achieve optimal coordination between the smart factory and the warehouse? Ideal storage installations must guarantee:
- Automated load handling
In manufacturing logistics, it’s common to find warehouses located next to production centres. These installations are responsible for storing semi-finished goods and managing finished products, preparing them and dispatching them to end customers. The internal flow of goods between both installations can be anticipated in large part, which makes automation of these facilities highly cost-effective.
Therefore, the use of automated systems doesn’t end with smart factories, but rather continues with their connection to the warehouse: conveyors and stacker cranes are charged with handling loads and transporting them from the production lines to the storage racks. An example of this is the installation Mecalux built for DAFSA, a manufacturer with the most advanced plant in Europe for producing, processing and packaging juices, soups and horchata (tigernut milk).
- Full traceability of parts and components inventory
Depending on the nature of production, warehouses can have inventories with thousands of different SKUs that play a role in the various manufacturing phases. Some SKUs will be final products received from the factory, while others will comprise parts or raw materials used on the production lines. Installations have to be prepared to control the stock level and location of each SKU in order to adequately supply smart factories.
A case in point is the warehouse of GKN Driveline, a company that manufactures and distributes parts for the automotive and aerospace industries. We equipped this firm with two automated warehouses for boxes: one dedicated to supplying the factory and another designed to prepare and dispatch orders of parts for customers. Faced with an extremely high volume of stock with approximately 5,000 SKUs, GKN Driveline achieved comprehensive traceability, thanks to the Easy WMS warehouse management system.
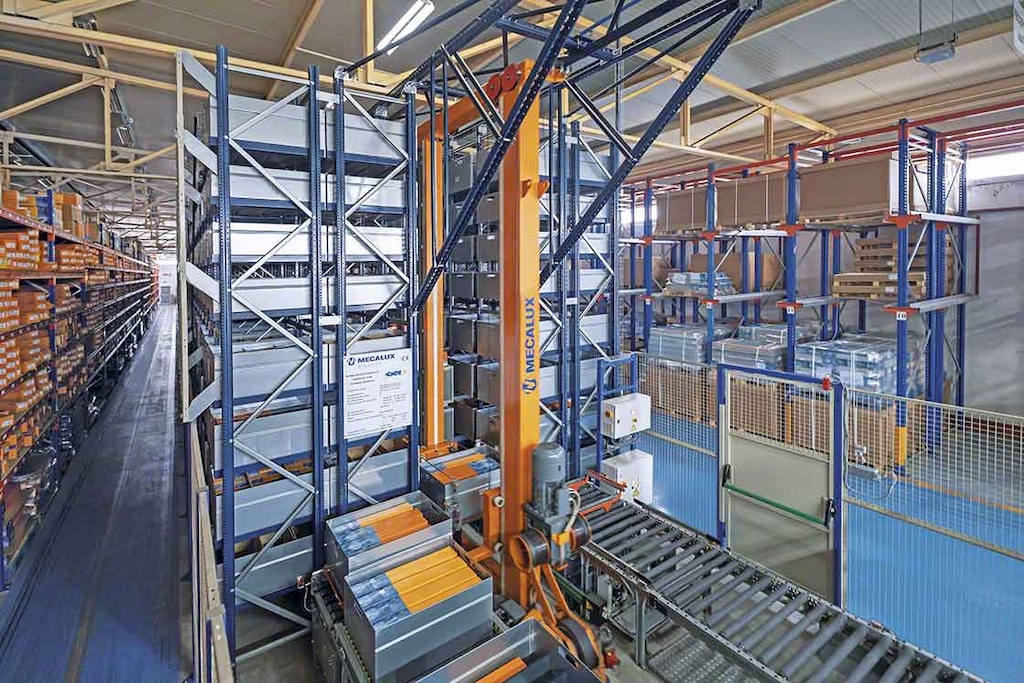
- Visibility of manufacturing and logistics operations
Material flows between installations are just as important as data flows between systems. They can’t be separated, which is why it’s essential to do away with information silos in a smart factory environment. In relation to the warehouse, the WMS has to be integrated with the rest of the company’s software; this controls warehouse shipping and receiving to ensure that there are no disruptions or errors in the supply of materials.
In this vein, not all WMSs are compatible with these requirements. That’s because the needs demand that these systems go a step further when it comes to their degree of specialisation. With that in mind, Mecalux’s Easy WMS has a production module that enhances the functionalities of the WMS to fulfil the specific demands of the manufacturing sector.
Manufacturers and the challenge of converting into smart factories
According to the Smart Factories at Scale report by the Capgemini Research Institute, companies are already implementing smart production strategies in 30% of their processes. Likewise, they plan on scaling up these initiatives to cover 40% more operations in the coming years. Not surprisingly, 68% of manufacturers surveyed claim that they have put in place smart manufacturing projects in their production plants.
These data point toward an upward trend, yet one that is progressing very gradually. Smart factories aren’t immune to challenges, which, in many cases, present major stumbling blocks that prevent them from being deployed quickly. For example, cybersecurity is an issue for 46% of those surveyed, while 51% of respondents were concerned about the lack of technical capacity to carry out integrations (many times due to the shortage of profiles trained for this, the highly-valued Talent 4.0).
In the field of warehousing logistics, we see similarities with this scenario. Nevertheless, the unstoppable changes associated with Logistics 4.0 are speeding up the transformation of warehouses to maintain market competitiveness. If you’re looking for expert advice on software and logistics automation solutions, be sure to get in touch. We’ve been optimising the logistics systems of all sorts of companies for over 50 years.