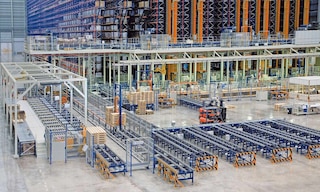
Warehouse organisation ideas to boost efficiency
The best warehouse organisation ideas are those tried and tested in numerous client facilities across multiple sectors and validated by storage experts.
How to organise the warehouse
When organising a warehouse, it’s essential to consider all the processes and operations performed daily, such as inventory management, order fulfilment and shipment coordination. The purpose of storage systems is to improve efficiency in these spaces, reduce operating costs and ensure high accuracy and quality for a company’s customers.
A crucial aspect of managing inflows and outflows is arranging product placement for easy identification and quick retrieval. Visible labels, correctly adapted shelving and efficient inventory control are critical for optimising these work areas.
Another excellent strategy for supervising and digitalising a facility is installing a warehouse management system like Easy WMS. This software intelligently assigns locations, sequences tasks and automates information flows to minimise errors, provide real-time inventory visibility and streamline key logistics processes. Additionally, it integrates with leading ERP solutions and automated storage and retrieval systems (AS/RSs) on the market.
Common mistakes when organising a warehouse
Starting operations in a logistics facility without prior planning or the guidance of an expert team often leads to these problems:
- Inefficient design. If pick paths and product storage are suboptimal, valuable time and resources will be wasted by the day. Attention should be paid to loading docks, space layout and the type of shelving, robots and machinery to be used. In addition to causing bottlenecks, design flaws often lead to overstock due to incorrect product turnover.
- Lack of item location knowledge. If goods aren’t correctly labelled or employees don’t have a WMS to indicate their positions, all processes will be delayed.
- Stockouts. When stock levels are unknown and real-time access to this information is unavailable, customers may not receive what they ordered.
- High return rates. If fulfilment processes aren’t sufficiently optimised, professionalised or automated, there may be shipment errors or delays, resulting in customer dissatisfaction.
What are the best practices when organising a warehouse?
Although no two facilities are the same and may require different solutions to reach their full potential, certain practices can significantly streamline operations. Here are some warehouse organisation ideas we recommend:
Move away from paper-based management
Relying on paper-based organisational systems makes it difficult to archive information for future reference and could lead to lost data. To achieve real-time visibility into what’s occurring in your facility, transitioning away from pen and paper or Excel should be one of the first changes.
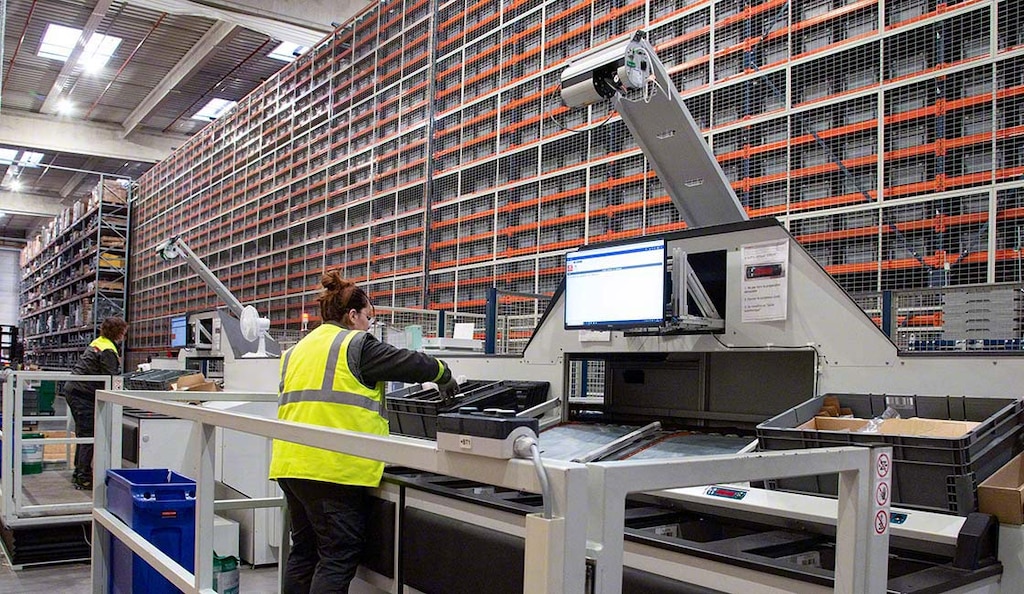
Apply the lean method
The Japanese management and operations philosophy known as the lean method identifies and eliminates activities that fail to add value to the production process. These include excess stock accumulation, bottlenecks and unnecessary movements.
Leverage vertical space
Instead of expanding horizontally or relocating your facility, look at making the most of its height. AS/RSs can lift loads using stacker cranes or pallet shuttle systems and clad-rack warehouses can be built up to 45 m high.
Automate processes
The rise of online sales and events like Black Friday have transformed warehouse and distribution centre operations. Installing automated systems like picking robots helps operators handle peak periods more efficiently.
Use the ABC analysis
The ABC inventory categorisation technique organises goods based on their relevance, value and turnover. Type A items are the most strategic, B items move more slowly and C items are those consumed the least.
Label products
Identifying products according to industry standards via barcodes that operators can read with RF scanners makes it easier to pick the correct merchandise.
Implement cross-docking
In cross-docking, goods spend minimal time in the warehouse between their receipt and subsequent distribution to the customer. Allocating a small space for this activity improves the use of storage areas in addition to reducing operations and material handling.
Collect metrics
Gathering data on warehouse tasks helps detect possible inefficiencies, identify areas for improvement, increase profit margins and lower operational costs.
Deploy Easy WMS
The Easy WMS warehouse management system ensures fast, simple integration with any ERP and other third-party software. It’s a valuable tool for all of the scenarios mentioned above. Similarly, it integrates with Mecalux’s automated and robotic systems as well as solutions from external companies.
How AI can optimise warehouse organisation?
AI is another valuable tool for improving warehouse organisation. For instance, picking robots successfully sort items and fulfil orders using computer vision, while autonomous mobile robots (AMRs) navigate without predefined routes thanks to machine learning. Moreover, predictive maintenance keeps machinery running longer by avoiding unplanned downtime.
Practical use cases of how to organise an industrial warehouse
Many companies rely on AS/RSs and specialised management software to handle large volumes of inventory:
- Miguélez. This Spanish manufacturer of low-voltage electric cables stores more than 35,000 tonnes of products in its facilities. With two AS/RSs and a pallet racking system, Miguélez efficiently accommodates various product formats, including coil, spools and reels.
- Blechwarenfabrik. At its Offheim (Germany) centre, the company makes over 100 million containers a year. Operations are structured around two automated warehouses — one for raw materials and another for finished goods — and managed by Mecalux’s Easy WMS.
- Grégoire Besson. The French farm machinery manufacturer works with a wide range of sizes, weights and product classifications. To optimise order processing, it combines cantilever racking, selective pallet racking and a miniload system at its Saint Germain sur Moine site.
How do you organise a small warehouse?
When your space is limited, warehouse organisation becomes even more critical. To maximise its potential, bear in mind the three Fs: function, form and flow of materials.
- Function. Define the operations that will take place in the facility.
- Form. In a small warehouse, every centimetre counts. The storage solutions you choose should maximise available space to support your project’s success.
- Flow of materials. With limited square metres, bottlenecks are more likely. Careful planning is vital for ensuring smooth movement of goods.
Organise your warehouse with Mecalux
At Mecalux, we upgrade operations in all kinds of facilities with storage systems, cutting-edge AS/RSs and WMS solutions. We work closely with our clients, tailoring our software to their particular needs. Are you looking to take your supply chain to the next level? Be sure to contact us to learn more about Easy WMS and how we can optimise your logistics operations.