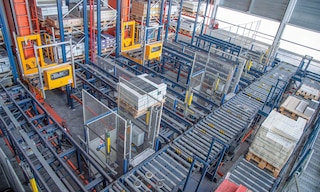
3 tips for advanced logistics
Advanced logistics is based on the use of technological solutions to improve the performance of stages such as warehousing, order picking and distribution of goods.
With the help of state-of-the-art technologies, companies can optimise times and costs to foster better logistics service. Advanced logistics relies on efficient planning and the use of solutions that, through the automation and digitisation of processes, boost warehouse productivity.
1. Designing efficient logistics planning
The first step towards advanced logistics is to plan and organise your company’s internal processes. Well-structured logistics planning is essential to improve the efficiency of operations such as raw material sourcing, stock management and order delivery.
Logistics planning must take into account aspects such as the warehouse layout, the type of product, the stock turnover and the seasonality of the stored goods. This preliminary analysis phase is aimed at optimising your company’s logistics resources and establishing KPIs that allow you to regularly assess your facility’s performance.
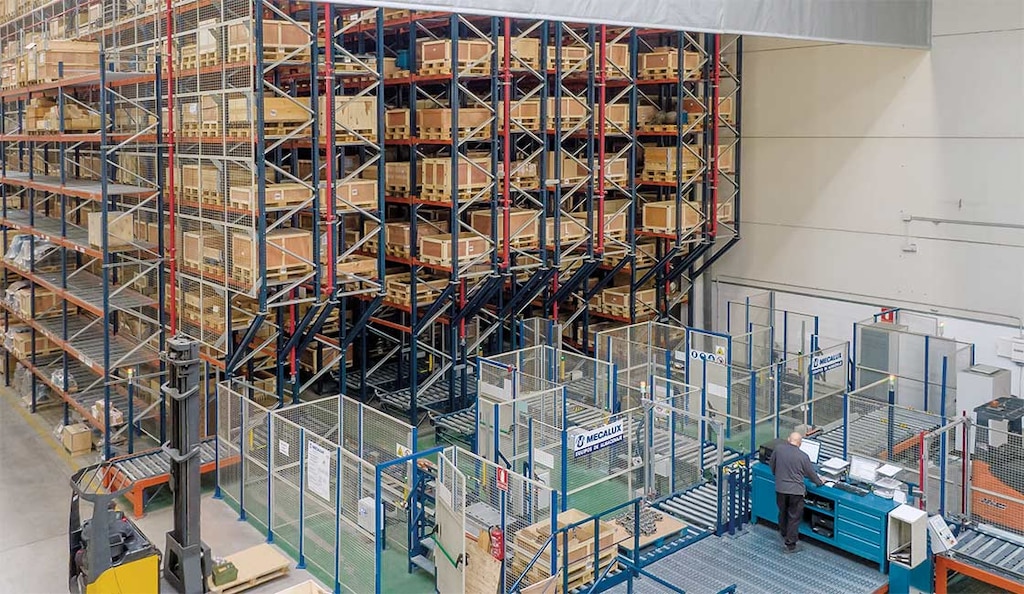
To achieve advanced logistics, planning must include the choice of storage systems that contribute to enhancing operations. There’s a wide range of solutions on the market adapted to each logistics need. Therefore, it’s crucial to analyse the type of goods, their demand and their seasonality to determine the ideal storage method, handling equipment and degree of automation.
Your logistics strategy must also determine the most efficient order processing method based on criteria such as the volume of SKUs, the characteristics of the product stored and the type of warehouse.
2. Digitising warehouse processes
Advanced logistics requires digitised management of the operations performed in your facility. Warehouse management software (WMS) is the most suitable tool for synchronising the processes that take place in the facility, from goods receipt to order picking and dispatch. The program maximises the performance of all types of warehouses. In manual facilities, the software sends instructions to operators on the tasks to be carried out. In automated warehouses, it connects with the different control programs to synchronise the movement of the robotised handling equipment.
WMS software automates decision-making such as the most convenient location for each SKU, the order of the tasks to be fulfilled out by each operator and the most efficient pick paths. For error-free warehouse management, it’s vital to configure the software with a set of preestablished criteria and rules. The parameters should be determined in advance, during the logistics planning process.
WMS software also controls the available resources in the different storage areas. The program promotes error-free inventory management: it provides real-time product status tracking, facilitating product traceability and avoiding losses of goods in warehousing operations.
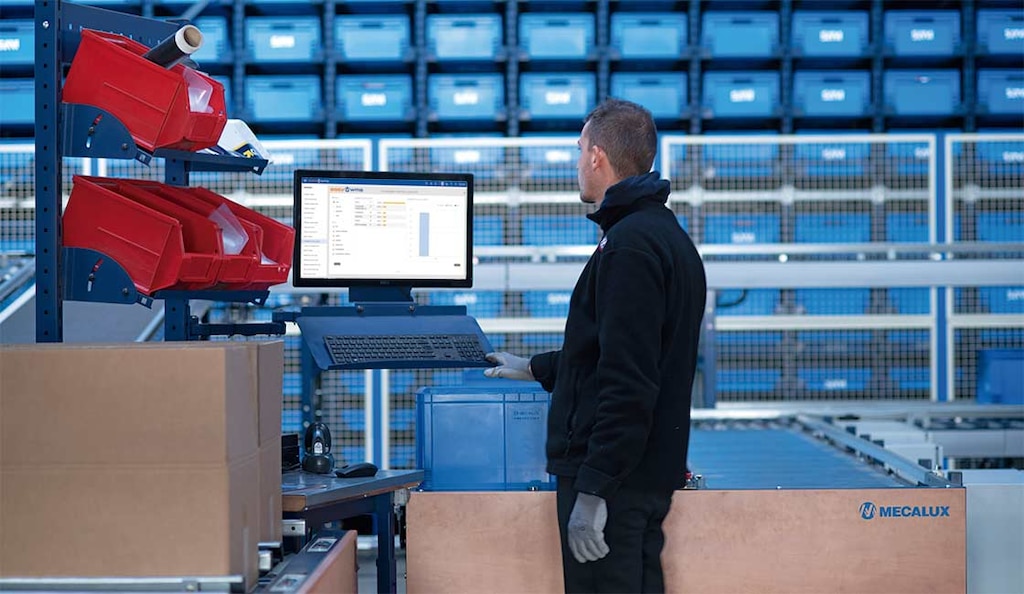
3. Automating company logistics
Implementing automated solutions in a warehouse or production centre enhances advanced logistics and increases throughput in steps such as order picking and internal goods transport.
During logistics planning, it’s necessary to determine the degree of automation of your operations. This usually depends on the business’s requirements, the warehouse layout and the technical characteristics of the products, among many other factors.
One of the first operations to automate is usually the movement of loads between the areas within the facility. Depending on the needs of your warehouse, these solutions can range from conveyor systems and pallet or box lifts to modern devices such as autonomous mobile robots (AMRs), which can perform tasks and move around the facility unmanned.
Companies with advanced logistics also often automate the storage and retrieval of products. Installing automatic handling equipment such as stacker cranes eliminates the risk of error and ensures maximum reliability in product handling. Depending on the type of unit load used in your warehouse, you can invest in solutions such as the automated Pallet Shuttle to speed up the storage of pallets or the Shuttle System, which streamlines the supply of goods to the picking areas.
To achieve advanced logistics, productive picking processes need to be in place. High-performance pick stations are an innovative solution that boosts the performance of warehouse pickers, enabling up to 1,000 picks/hour.

The road to advanced logistics
Advanced logistics starts with the implementation of new technologies in warehouses and distribution centres. Your company’s logistics manager must rely on the latest storage, production and order picking solutions to maximise your facility’s throughput. An intelligent warehouse uses technologies such as data analytics or process simulation to increase logistics performance. The most advanced management programs make it possible, for example, to create digital reproductions of the various types of operations so that changes can be implemented in a virtual environment.
Moving towards advanced logistics, it’s important to seek the advice of warehousing experts who accompany businesses in the implementation of innovative technologies. Want to get the most out of your logistics operations and your facility? Don’t hesitate to contact us. One of our consultants will advise you on the best solution for your company.