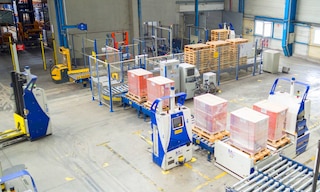
Automated forklifts: efficient internal goods transport
Automated forklifts are robotic handling equipment that emerged in response to the need for companies to streamline the internal transport of materials between different areas of a warehouse.
The growing complexity of logistics processes and the demand for agile operations have led businesses to automate movements in their facilities to boost competitiveness. In contrast to traditional equipment, automated forklifts provide uninterrupted performance 24/7 if necessary. In a world where companies strive to be more competitive, equipping logistics centres with robotic systems is becoming an ever more common solution.
What is an automated forklift?
An automated forklift is a type of handling equipment used in warehouses, production centres and other industrial environments to transport loads efficiently and with complete autonomy. These forklifts are designed to move goods from one place to another without the need for drivers.
Automated forklifts are outfitted with advanced technology, including sensors, navigation systems and cameras to enable them to function independently. Moreover, thanks to the warehouse control system, these forklifts can:
- Navigate safely in their environments, avoiding people and obstacles.
- Pick up and release materials with precision.
- Perform specific tasks, such as loading and unloading pallets from racks.
- Optimise routes to minimise internal transport times.
- Communicate with other equipment and systems within the facility to coordinate operations.
Automated forklifts are especially well-suited for warehouses that manage large volumes of goods or require highly reliable product handling.
Types of automated forklifts and examples in industry
The market features several kinds of automated forklifts designed to meet all possible applications in industrial and logistics environments. These are the most common varieties:
AGVs
Automated guided vehicles (AGVs) are driverless machines that move loads autonomously. Similar to manual forklifts, their main difference lies in the fact that they follow a pre-configured circuit that guides their movement. AGV forklifts can navigate by means of two guidance systems. Laser-guided vehicles employ a laser to detect markers on the floor, while wire-guided machines use a wire embedded in the floor.
AGVs automatically connect various areas within a logistics centre or specific storage areas to production lines. One example of the application of AGVs in industry can be seen in Novartis, a multinational pharmaceutical and biotechnology company. The business uses these types of vehicles in its rack-supported building constructed by Mecalux in Poland to ensure the efficient delivery of goods to production. “These forklifts have allowed us to completely free up space and aisles,” says Tomasz Marchewa, Supply Chain Manager at Novartis.
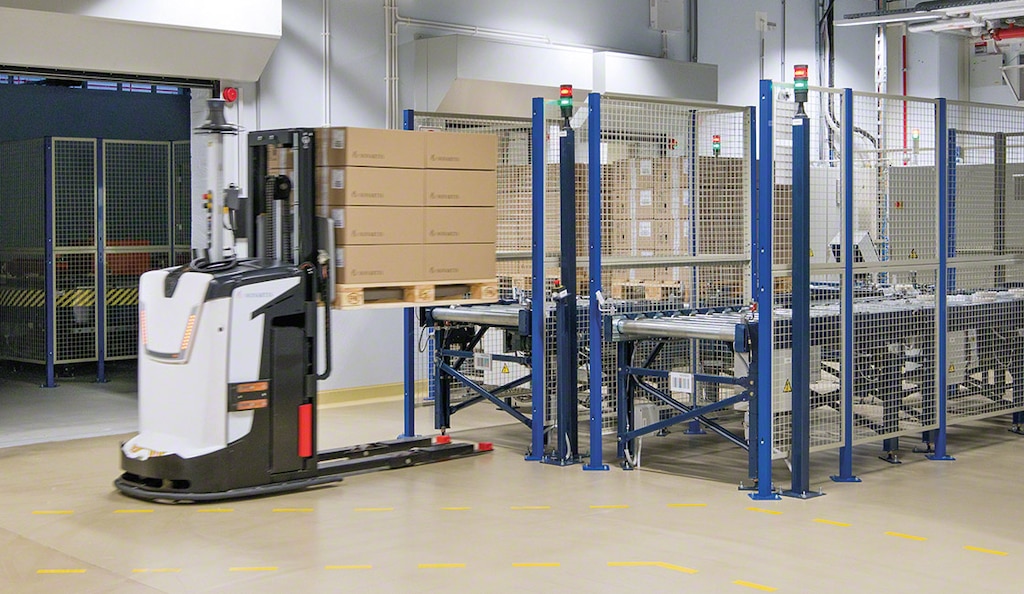
AMRs
Autonomous mobile robots (AMRs) are devices capable of executing tasks and moving within a facility without human guidance. To do this, they’re equipped with sensors, navigation software and digital layouts of the space to interpret their environment.
Their function is the same as that of AGVs: to move materials between two points. The difference between the two lies in their navigation system. AGVs travel along a predefined path using laser- or wire-guided systems. AMRs, on the other hand, adapt their routes according to the information they receive from their environment in real time, without the use of guides, wires or magnetic strips.
AMRs enhance productivity in warehouses. The Spanish emergency lighting company Normagrup turned to this solution to optimise the transport of raw materials. Four AMRs move goods from its mini-load system to its production lines. Every time a kit is assembled, a vehicle picks it up and brings it to the production line that requires it as quickly as possible. “With an increasingly hectic production pace, we needed to effectively optimise and organise the management of these materials,” says a Normagrup representative.
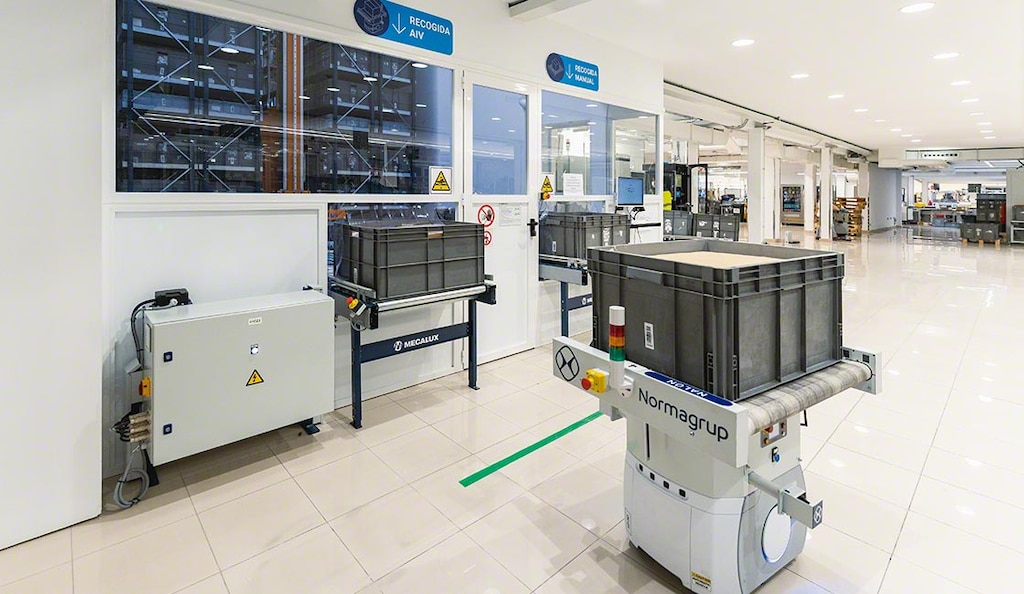
Other automated material handling equipment
In addition to automated forklifts, the logistics market offers other robotic transport solutions that expedite internal product movements:
Storage robots (AS/RS)
In this category, automated storage and retrieval systems (AS/RS) — e.g., stacker cranes (AS/RS) for pallets and for boxes (mini-loads) — stand out for their capacity and agility in inserting and removing products from racks. There are several types of stacker cranes, including single-mast, twin-mast and AS/RS trilateral stacker cranes.
Many companies opt for AS/RS to automate internal goods transport in their warehouses, replacing conventional forklifts. The robotic devices move along the length and height of the storage aisles, aided by sensors and cameras to locate and remove products from the racking. The French paper manufacturer Clairefontaine, for instance, implemented this technology to accelerate storage tasks in its logistics facility in Alsace (France): “By automating our warehouse, we’ve improved our throughput and responsiveness. Plus, we’ve reduced operating costs and errors relating to manual management,” says Florian Challe, Logistics Operations Manager at Clairefontaine.
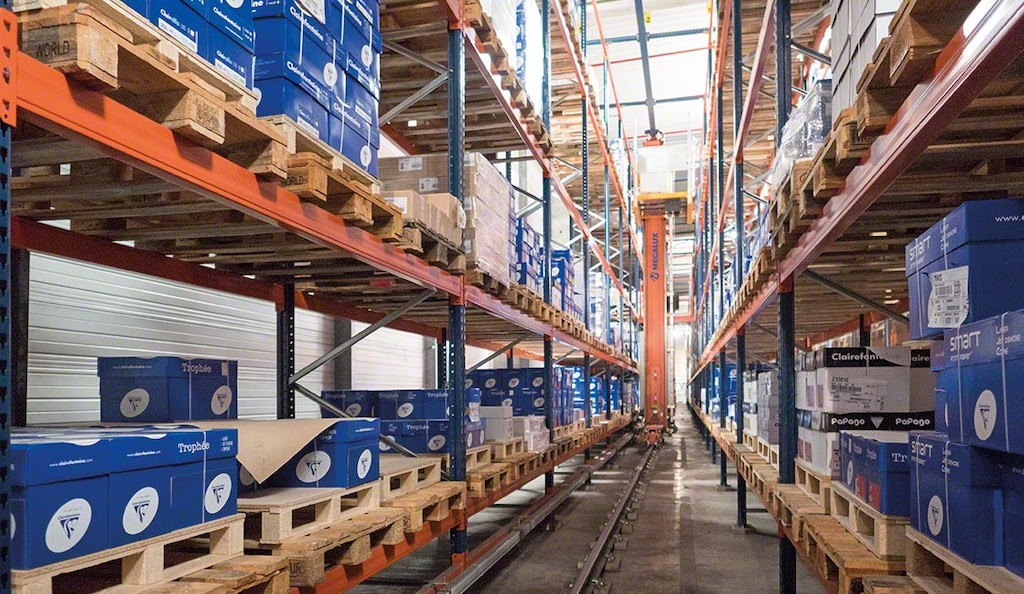
Transport robots
Automatic transport equipment, such as box and pallet conveyor systems, are effective solutions that facilitate product movements within a logistics facility. These automated transport systems allow for the creation of various configurations to connect the different zones in the warehouse.
Another transport solution for linking separate areas within a facility is the electrified monorail. This system consists of a set of automatic trolleys. Driven by an electric motor, they move along an electrified rail suspended from the ceiling or fixed to the floor.
For example, in the logistics complex of ALPLA in Golborne (UK), transport robots save time and boost efficiency in repetitive load movements. This global leader in the development and production of plastic packaging solutions automated internal goods transport via an automatic conveyor system by Mecalux. The conveyor connects the warehouse to the production lines. “Thanks to the automated transport solution, we’ve slashed costs and CO2 emissions. And we can now move around 2,500 pallets a day 24 hours, 7 days a week,” says Liam Grimwood, UK Plant Engineering Manager at ALPLA.
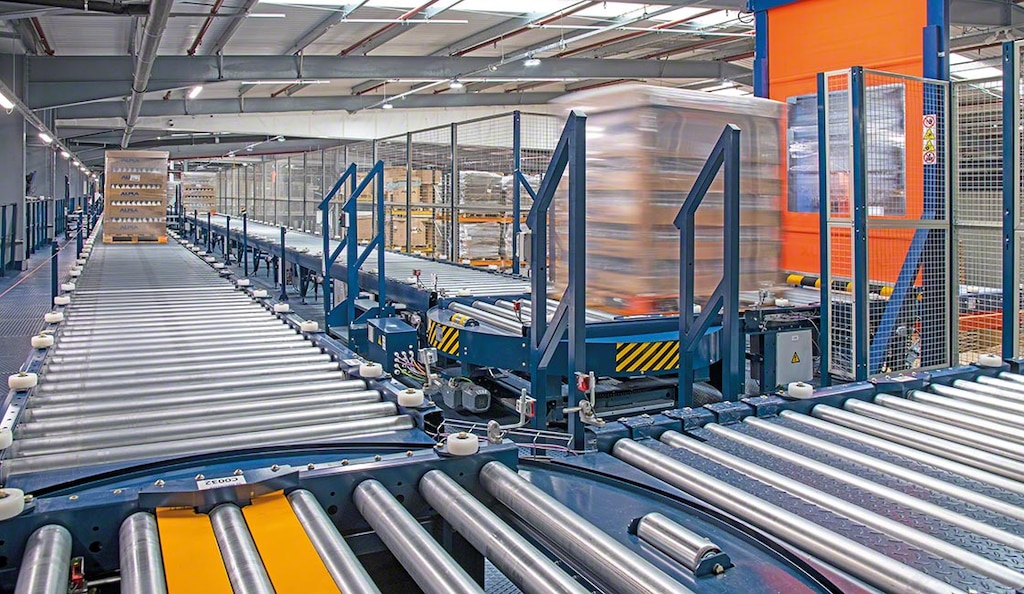
Benefits of automated forklifts
Autonomous forklifts offer numerous benefits in industrial and logistics environments, namely:
- Increased efficiency. Automatic forklifts can operate 24/7, raising productivity and the efficiency of goods movements.
- Enhanced reliability. This material handling equipment is programmed to perform specific tasks with pinpoint accuracy, minimising errors and damage to merchandise.
- Improved safety. Advanced sensors and safety systems enable automated forklifts to detect obstacles and avoid collisions, minimising the risk of accidents in the warehouse.
- Space optimisation. Automated forklifts can be designed to operate in narrow storage aisles, maximising storage space.
- Greater flexibility. These machines are programmable and easily adapt to various tasks and work environments, making them versatile and valuable in a wide range of applications.
- Better inventory management. Automated forklifts use software connected to the warehouse management system, providing stricter, real-time control over stock levels.
Warehouse productivity
Automated forklifts can be tailored to diverse logistics needs. Their implementation in industrial and logistics environments offers multiple advantages, including increased productivity, reduced errors and enhanced safety. Additionally, these forklifts are often part of broader logistics automation systems, leading to more efficient inventory management and shorter delivery times.
The benefits of these internal transport systems are driving more companies to embrace automation to streamline their storage and order fulfilment tasks. At Mecalux, we have extensive experience in implementing these types of solutions for businesses across all sectors. Get in touch to learn how an automated forklift system can help boost efficiency in your warehouse.