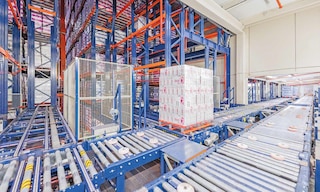
Internal transport: systems and examples
In the age of modern logistics, where efficiency and speed are vital for operational success, internal transport solutions play a key role in warehousing. Designed to move products and materials inside logistics centres, these systems are the backbone of the supply chain. They ensure each item arrives at the right place at the right time.
From more traditional material handling methods to state-of-the-art automated solutions, internal transport elements have undergone significant transformations to meet the challenges of an ever-more demanding market.
What is an internal transport system?
An internal transport system consists of equipment designed to move items within a warehouse or distribution centre. These solutions are crucial for improving productivity, speed and safety in material handling. They can be implemented across a range of warehouse processes, including receiving, storage and, finally, shipping.
The design and selection of an internal transport system depends on several factors, such as product type, number of movements anticipated, warehouse layout and specific business needs in terms of inventory management accuracy.
Types of internal transport and practical examples
Internal transport systems encompass a variety of technologies and equipment, both manual and automatic. These are the most common:
Pallet trucks and forklifts
These varieties of internal transport devices are ideal for expediting movements of goods along short distances. Equipment can be manual or motorised. The machine found in most manual warehouses is the pallet truck. It supports loads using its parallel forks, raising them slightly off the ground to facilitate movement.
Within the forklift category is a wide range of motorised material handling equipment. These machines run the gamut from counterbalance forklifts (known for their versatility) and reach trucks (perfect for homogeneous goods) to very narrow aisle (VNA) trucks, side loaders and order pickers.
An example of this type of internal transport can be seen in the warehouse of Giménez Ganga, a leading manufacturer of solar protection solutions, ceiling coverings and decorative blinds. The company uses side loader forklifts in its facility in Alicante (Spain) to efficiently handle aluminium profiles measuring between 5 m and 7 m long.
Conveyors
Box and pallet conveyor systems, both roller and chain, are another category of essential internal transport systems for high-traffic warehouses. They are used to connect different areas of a facility as well as storage with production.
Conveyors consist of a set of rollers or chains that carry the load (boxes or pallets) and propel it along a circuit. The system is equipped with electric motors that move goods in a safe, controlled way. Conveyors operate using a warehouse control system (WCS), which executes machine movements as per instructions sent by the warehouse management system (WMS).
In the UK, pallet conveyors have successfully linked the production and storage facilities of the packaging solutions multinational ALPLA. The solution installed by Mecalux runs 24/7, moving around 2,500 pallets daily between the two buildings, separated by a public road.
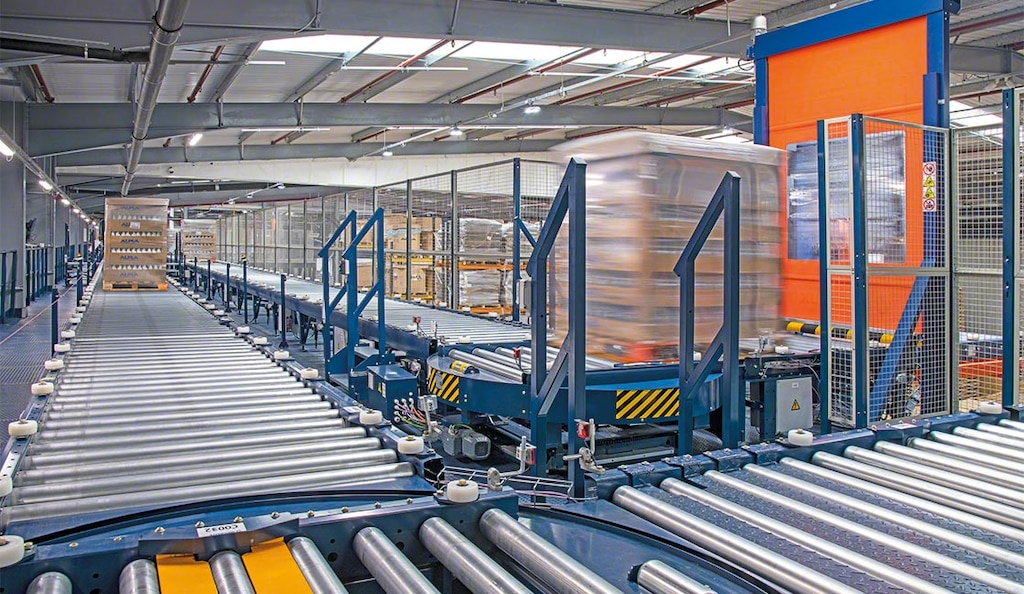
AMRs
Like conveyors, autonomous mobile robots (AMRs) and automatic guided vehicles (AGVs) are extremely useful in environments with a continuous and repetitive flow of materials. This is because they save time and increase productivity.
AMRs move without human guidance or predefined routes, adapting to their path based on real-time information from their environment. They do this through sensors, navigation software and digital layouts of the space to interpret their surroundings. Spanish emergency lighting company Normagrup turned to this solution to optimise the transport of raw materials. Four AMRs move goods from its miniload system to its production lines.
AGVs
Automatic guided vehicles (AGVs), meanwhile, are warehouse machines that travel autonomously along a preprogrammed route. They can be either wire-guided (AGV) or laser-guided (LGV). Swiss pharmaceutical company Novartis, for instance, uses a set of AGVs to transport goods between its automated clad rack warehouse and its manufacturing centre.
Electric monorail systems
Another internal transport solution employed to connect different warehouse areas is electrified monorails. These consist of automatic trolleys driven by an electric motor. They move along an electrified rail suspended from the ceiling or fixed to the floor.
Electric monorail systems are advisable for companies that require speedier operations. A case in point is Sokpol’s juice warehouse in Poland, connected to the production centre via a monorail conveyor. This internal transport system reaches 100 m/min and ensures a continuous flow of goods.
Stacker cranes
Internal transport systems not only move goods between two zones but also inside storage aisles. The automatic handling equipment in this category — e.g., stacker cranes for pallets and boxes (miniload systems) — stands out for its agility in storing and retrieving products from racks. Stacker cranes come in several varieties, including single-mast, twin-mast and AS/RS trilateral stacker cranes.
Stacker cranes for boxes have optimised the storage of electric chargers for manufacturer Wallbox. Its facilities in Barcelona (Spain) feature an automated storage and retrieval system (AS/RS) for boxes with five miniload stacker cranes. Equipped with telescopic forks, these machines simultaneously transport two cardboard boxes containing chargers. This efficiency enables the company to ship up to 6,000 chargers a day.
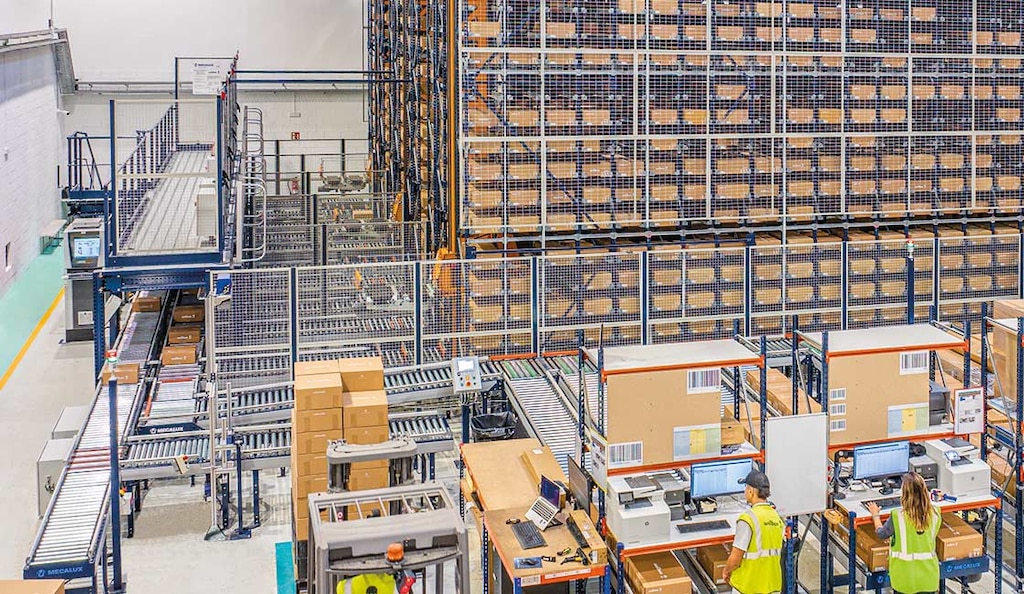
How to choose the right internal transport system
Selecting appropriate internal transport elements is fundamental for streamlining operations and raising productivity. These systems, which range from conveyors to AVGs, expedite the movements of goods within a warehouse. Moreover, they improve inventory management, reduce errors and maximise the use of available space.
Your choice of internal transport system shouldn’t be taken lightly. It calls for a thorough analysis of your specific warehousing needs. Mecalux has implemented intralogistics solutions in multiple countries on different continents. If you’re looking to optimise intralogistics processes in your facility, be sure to contact us. One of our expert consultants will analyse your needs and come up with the best solution for your business.