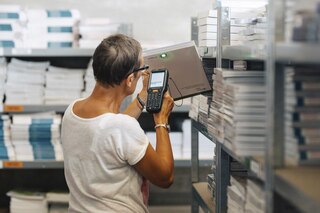
Item coding in the warehouse
In storage installations, item coding enables efficient inventory organisation, which reflects positively on all operations carried out in the warehouse. Therefore, each product should be identified upon receipt.
The item coding process consists of explicitly identifying the goods with a code or sign. This code is linked to a label affixed to the product that can be accessed electronically. In logistics, the most standard labels are barcodes and RFID tags.
In this article, we’ll delve into codification and the advantages of properly identifying all products in the warehouse. We’ll also indicate the equipment and criteria that go into coding, with special emphasis on WMSs.
What’s item coding in a storage installation?
Coding means assigning a code to a product. This code lets us see some of the item’s main characteristics: its SKU, ingredients, hazard level, warehouse arrival date, packaging and expiry date, among other data.
The objective of coding is to identify goods in a unique way (there can’t be two products with the same code). Warehouse management systems (WMSs) play a key role in this process. The WMS is what generates the code for each item, assigns locations to the products in the installation and monitors the various phases the goods go through (in other words, it controls their traceability).
Nowadays, trends such as super-fast deliveries and the storage of small products have made warehouse processes more complex. Thus, establishing comprehensive control of the items and registering all their movements is vital for accurately analysing and optimising goods flows. Thanks to coding and the help of a WMS, operators can locate and dispatch products more swiftly and with fewer errors.
Advantages of coding and labelling products
Coding is extremely helpful in all links of the supply chain, from the manufacturer to the end consumer. It helps manufacturers to find out the status of their inventory and quickly locate and dispatch goods. Consumers, for their part, benefit from the good logistics practices that companies implement. These ensure that products are in stock when customers go to make purchases and that they will receive their online orders promptly and without error.
So, coding items and ensuring that they are suitably identified provides the following benefits:
- Agile goods receipts. If all the products arriving at the installation are labelled, they can be identified more speedily. The moment its label is read by a radiofrequency terminal, the item is automatically recorded in the system.
- Traceability. With all the products identified, it’s easy to monitor the different phases the goods go through.
- Real-time inventory control. It’s possible to know the exact number of SKUs in the warehouse at all times.
- More in-depth business knowledge. The more data you have, the easier it will be to make decisions on how to fine-tune operations and anticipate new customer demands. Coding makes it possible to analyse a host of variables, from the quantity and date on which each product is sold to the space needed to store it in the installation.
- Efficient order prep. Picking is a warehouse operation that requires additional time and resources. Having all items controlled and identified ensures speed, as the WMS knows the exact location of all SKUs and gives operators specific orders on how to locate them.
- Error-free processes. Coding the goods prevents deviations and mistakes in all kinds of operations, resulting in improved logistics service, increased customer satisfaction and considerable cost savings.
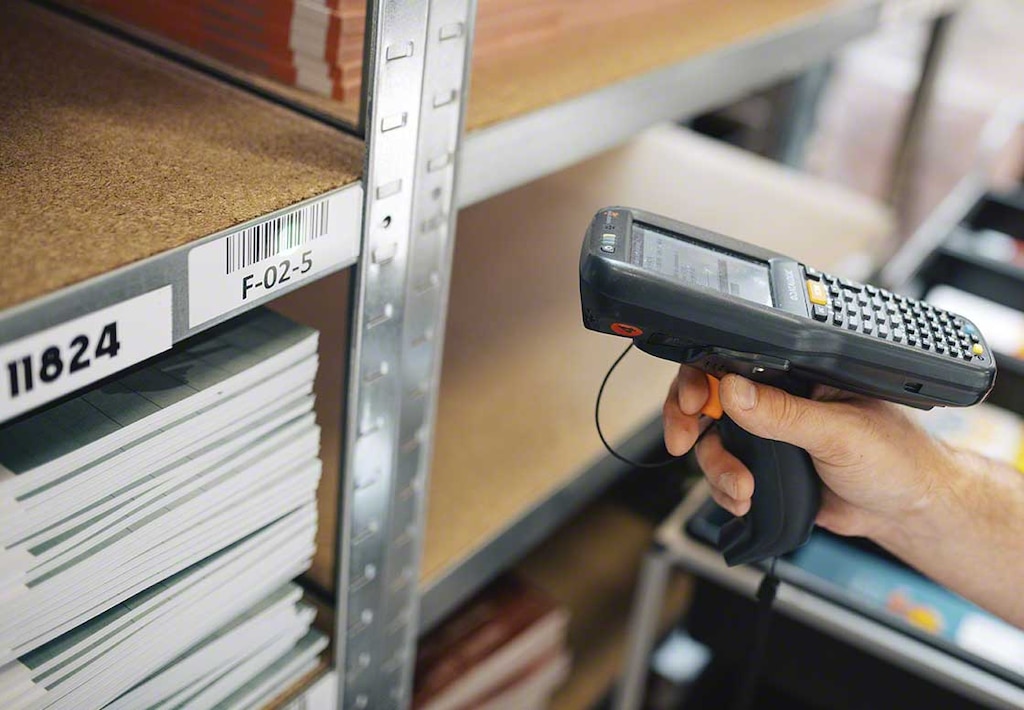
Item coding methods and standards
Depending on the symbols used, there are various ways to code warehouse goods. Companies choose the system that best suits them. The most common are:
- Numeric coding. Only numbers are used (no letters or signs).
- Alphabetic coding. Composed solely of letters.
- Alphanumeric coding. The code is a combination of letters, numbers and signs.
If a company decides to deploy its own coding system, it should be user-friendly for all staff involved. The codes should be short and always have the same length so that they are easy to read and write.
Once the type of coding has been chosen, the next step is to label the merchandise. This is where the barcode, the most universal way to represent a code in a warehouse, comes into play. The laser scanner is charged with reading the bars and converting them into their alphanumeric equivalent, making this a quick, precise system.
Although there are more modern alternatives, such as QR codes and RFID tags, it’s tough to top the simplicity and effectiveness of barcodes. Hence, their ubiquitous presence in the logistics sector. Moreover, barcodes can be used both internally and externally. However, to be used outside the company, among various businesses, a series of norms and standards should be adopted.
The GS1 (previously known as the International Article Numbering Association) has developed a coding system that guarantees the unique identification of products on an international level.
Let’s take a look at the most typical codes established by this association:
- EAN-13: Serves to identify, for the most part, items displayed at points of sale. It was given this name because it includes 13 numeric digits divided into four categories: country of origin, product manufacturer, product code and control number. The manufacturer code is provided by the competent body of each state. UPC-A format barcodes have traditionally been used in the US, whereas EAN-13 format barcodes have been used throughout the rest of the world, according to the International Barcodes Network. Nowadays, the majority of shops throughout the world accept barcodes in either format. Nevertheless, there may be some older systems that only accept one or the other. This means that if your product is being sold in the US, the UPC-A format barcodes are best. However, if your product is international, or sold in a country other than the US, an EAN-13 Barcode is best.
- EAN-128 or GS1-128: created for the purpose of facilitating information that supplements that of EAN-13 (for example, a product’s weight, manufacturing date, expiry date, batch, series number, final destination, etc.). It’s the baseline code of the logistics sector.
- SSCC (Serial Shipping Container Code): implemented for order handling and monitoring. This code is especially useful for ensuring efficient deliveries.
ERPs and WMSs: software for coding goods
The only way to code items in the warehouse accurately is by using software: fundamentally, ERPs and WMSs.
The ERP assigns a code to each item in the company’s catalog in a completely automatic way. The code needs to respect the type of coding applied by the company (UPC-A, EAN-13, EAN-128, RFID tags, etc.).
For its part, the WMS (Easy WMS by Mecalux, for instance) can also generate codes. By way of illustration, this can be done for items that have arrived at the warehouse without coding and for new products created in the installation, such as kits. In these cases, operators have to identify each item one by one and enter them all into the system manually (indicating their characteristics so that the WMS can recognise them and create the appropriate codes).
By scanning a code, workers access all the information on the item in question (weight, volume, precautions to take into account when storing it and turnover).
The ERP is equipped with the masters, that is, databases with all the rules and data required to carry out the business activity (among others, transport agencies, suppliers and, of course, the item master). The item master is what’s most relevant in logistics and coding, in particular, since it includes all the information on the goods.
The WMS absorbs all the item-master data to adequately manage the products in the warehouse. The ways in which the various processes are carried out will depend on the characteristics of the goods. In picking, for example, it’s necessary to know the item’s volume to designate the boxes and packaging to be used.
The connection between the ERP and the WMS has to be continuous and bidirectional; with all the information from the code and the item master, the WMS can organise the products in the warehouse as per criteria such as their nature, volume, weight, status, packaging and attributes (expiry date, quality, color, etc.).
The WMS should be designed to devise a goods slotting strategy based on the company’s preferences and needs. Proper product distribution in the installation will have a positive effect on all activities taking place in it, above all, order preparation.
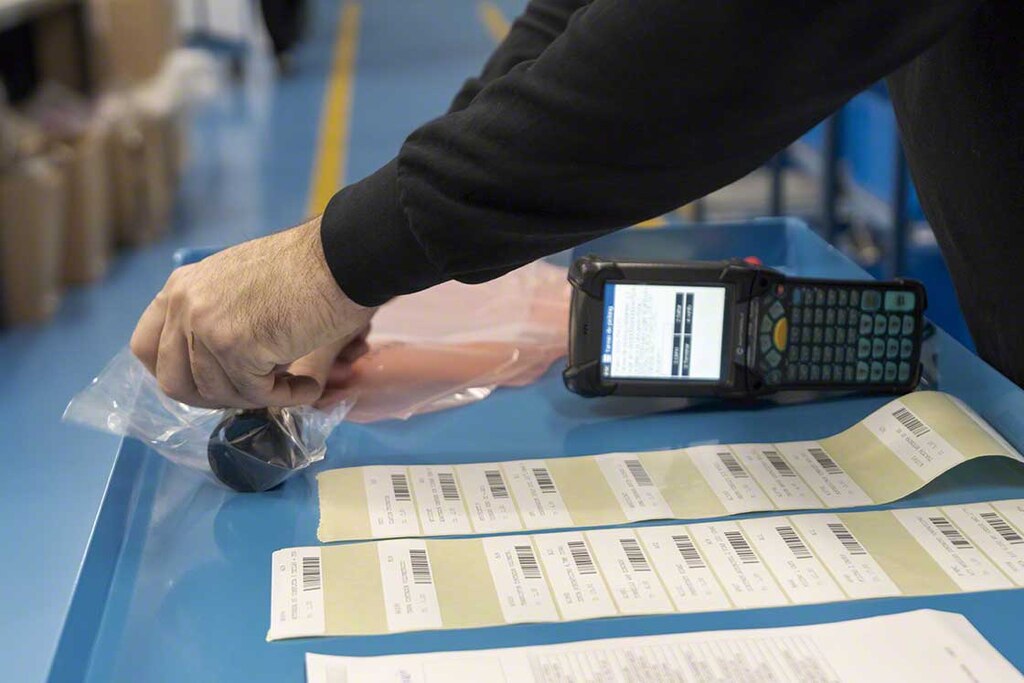
Coding: order and control
The ultimate goal of the coding process is to facilitate the location of merchandise in the warehouse and ensure full traceability. Coding is synonymous with organisation and control. Having identified all the items contributes towards much more efficient storage management. The most evident advantage is traceability: the recording of every movement of the products along the supply chain.
There’s no doubt about the importance of a WMS, a system capable of controlling stock and all movements produced in the installation for the purpose of both knowing the product inventory and locating the goods. To accomplish this, coordination between the ERP and WMS is essential (the former manages the item master with the data on each product, while the latter reads the product code and assigns the goods a location in the warehouse).
Companies need to identify all products as they arrive at the installation in order to slot them properly, according to their characteristics. The WMS incorporates rules for adequately distributing goods throughout the warehouse. This system knows the exact location of each item in real time.
Be sure to get in touch with Mecalux if you want to equip your warehouse with a WMS prepared to control and optimise all processes, strictly monitor the products, code them and efficiently manage flows. Easy WMS is a system that can be easily integrated with any ERP to coordinate all these processes, including item coding.