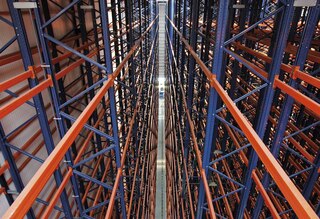
Warehouse too small? What to do when the walls start closing in
One of the most common issues for warehouse managers is what to do when the installation gets too small. The rise in prices in the logistics real estate market means that, in many cases, expansion as a solution to a small warehouse isn’t economically viable. However, on occasion, behind the progressive lack of space lies inefficient management.
In our article, we analyse the most common causes of this shortage of space. Plus, we propose options for leveraging the available surface area and continuing to manage a facility that’s become too tiny.
Signs that your warehouse is getting too small
Here are some indications that you’re about to reach your space limit:
- More than 85-90% of the total storage capacity is continuously occupied. A full warehouse is usually a double-edged sword. Although the end goal from a storage-cost perspective is to make the most of the installation, this can also reduce the flexibility of operations. With such a high occupancy level, the warehouse wouldn’t be able to respond to even the slightest increase in stock.
- There are incidents in location management: they may occur because a certain type of racking or specific location is overloaded, or because other areas in the installation are constantly used as makeshift storage space (aisles, the preload zone, the maintenance area, etc.).
- The number of pending orders or back orders steadily grows: these refer to purchases received by the warehouse but that can’t be fulfilled because of stock imbalances. This affects the dispatch completion rate and prolongs cycle times.
Reasons for lack of warehouse space
Factors that contribute towards shrinking space in an installation can be varied. The most frequent are usually linked to business changes, such as rises in sales, international expansion, or increased goods procurement for commercial reasons.
Nevertheless, the lack of storage space can also stem from the emergence of new digital business models. If the company begins to manage orders online, adopting an omnichannel retail strategy, the installation needs to adapt. To do this, it has to set aside extra space for more complex picking and for labor-intensive returns management.
But what if it’s not merely a square footage issue?
Warehouse mismanagement can also make an installation seem too small. In this vein, the most common causes are:
- Poorly distributed space or an outdated warehouse layout: installations are normally designed on the basis of specific goods flows, a concrete number of SKUs and items with specific characteristics. However, with increasingly volatile supply chains and more demanding levels of service, changes can arrive sooner than expected. Consequently, the distribution of space in the warehouse becomes inadequate, as the market advances faster than the physical infrastructure itself.
- Excess inventory: it’s common for firms to prioritise high-turnover products in their procurement policies. Be that as it may, the boom in sales of “A” (high-turnover) items can dwarf the installation if the space reserved for them isn’t optimised. The opposite can also occur: you can have an excess of low-turnover goods due to too much safety stock or to deviations from the sales forecast (bullwhip effect).
Ideas for maximising current warehouse space
The strong demand for storage space in recent years has driven land prices up, especially around large urban areas. In fact, in the US, warehouse availability is at its lowest point since 2000, with only 7% of space for sale (3 points less than in 2014), according to data from real estate firm CBRE.
So, if expanding or moving to a bigger site isn’t an option, how can you make the most of your square yard?
- Rethink the layout and consider automation
Organising the layout of a small installation comes down to pure precision. The first step to devising the layout of a warehouse consists of accurately measuring the actual working space you have, excluding the area occupied by architectural elements such as columns, walls, doors, etc. From there, the analysis lies with the inventory: you need to know what products are handled (number of SKUs, volume and weight) and where and how often they’re moved (warehouse inflows and outflows).
This study is necessary for assessing alternatives that can articulate the available space in a small installation. One solution that works extremely well is automating the operations with the most repetition and that remain stable over time.
In this sense, automated systems such as miniload warehouses and stacker cranes enable you to concentrate SKUs and eliminate space allocated to aisles. For example, we designed an automated installation for Trumpler that can hold 2,512 pallets in a surface area of just 840 m2.
- Assess other alternative storage systems
Increasing the warehouse’s storage density by adjusting the type of racking is another option that will make the installations appear bigger in terms of number of cycles. Pallet racks bring considerable advantages for goods accessibility, but they offer less storage density than compact storage systems.
Nowadays, there’s a huge variety of high-density racking, whether flow or standard systems, that allows you to operate with different levels of goods movements. This can be seen in the College of DuPage’s small warehouse, which used a high-density flow system to solve height and depth issues in the installation.
- Improve inventory management with a WMS
A small warehouse can be very complex from a stock management point of view, just as an installation can grow small due to poor inventory management. Warehouse management systems become essential for dealing with both situations and leveraging storage space.
A WMS such as Easy WMS organises goods movements and records data in real time. How does this help to optimise storage capacity? WMSs make it possible to:
- Adjust stock location criteria: this software is crucial for effective space management. With this alone, for example, you can implement a chaotic storage system that limits empty spaces as much as possible. Thus, the installation’s effective capacity is increased while maintaining streamlined operations, as the WMS optimally plans operators’ workflows.
- Speed up inventory taking to detect obsolete products or imbalances in SKUs recorded.
- Coordinate procurement management: the purchasing department can schedule stock replenishment more in line with space availability, preventing the warehouse from becoming overloaded.
Add cubic metres to your installation
In the five years between 2012 and 2017, the average warehouse size increased by over 140% in the US, according to CBRE data. But how can an installation gain cubic metre?
- Choose Clad-rack warehouses: the racking makes up the actual structure of the warehouse. Combined with automated systems, these installations can measure over 40 meters.
- Equip the premises with tall racks: it’s important to consider the impact this will have on handling equipment and picking.
- Add mezzanine floors: for instance, at Saint-Gobain’s maintenance warehouse, the space above the loading docks was leveraged to install a mezzanine for small products.
- Rent a temporary installation: this is a good option when the lack of space is due to marked seasonality, as in the case of e-commerce logistics.
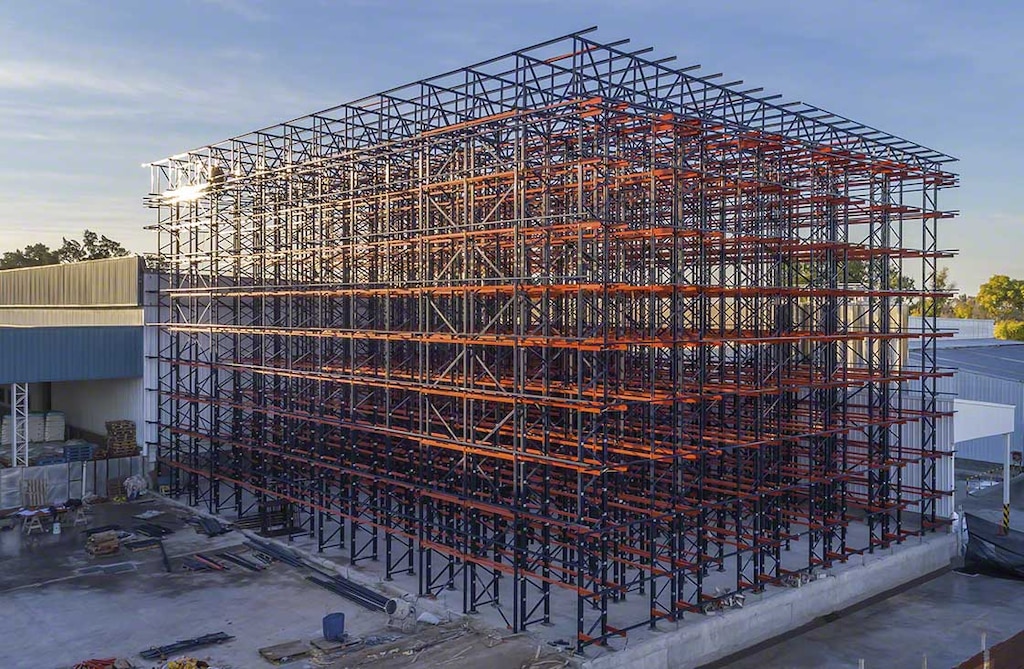
Coping with scarce storage space
Globalisation and new consumption habits have created complex supply chains that require greater storage space at all levels. Future prospects indicate that this trend is here to stay and that it will be normal for warehouses to feel too small from time to time.
If you’ve noticed that it’s getting harder and harder for your storage facility to successfully meet space needs, don’t hesitate to contact us. We’ll analyse your situation and help you to maximise your installation.