Warehouse labelling: how to do it right
Warehouse labelling is an essential process to correctly identify the goods as well as the different areas and elements involved in logistics operations.
Labels make it easier to code products, load-bearing elements and racks quickly and accurately, limiting the risk of error in processes such as goods handling and order picking. Proper labelling minimises confusion in logistics operations and consequently boosts productivity in the facility.
What is warehouse labelling?
labelling is the process of coding goods with a unique code for better organisation in the facility and improved logistics management. Stock coding ensures product traceability during phases such as order picking and dispatch. Labels typically contain key information such as the item code or logistics attributes (weight, volume, etc.) as well as other essential information such as sender or destination warehouse.
Companies not only label the goods but also often code the different warehouse areas and storage systems to streamline the picking and replenishment of products in the locations. The labelling of elements such as storage bins or rack bays simplifies operator tasks and results in a more orderly facility.
The labels — preferably alphabetical or numerical — are placed on storage systems to make it easier for operators to identify the location they need during operations such as stock replenishment and order picking.
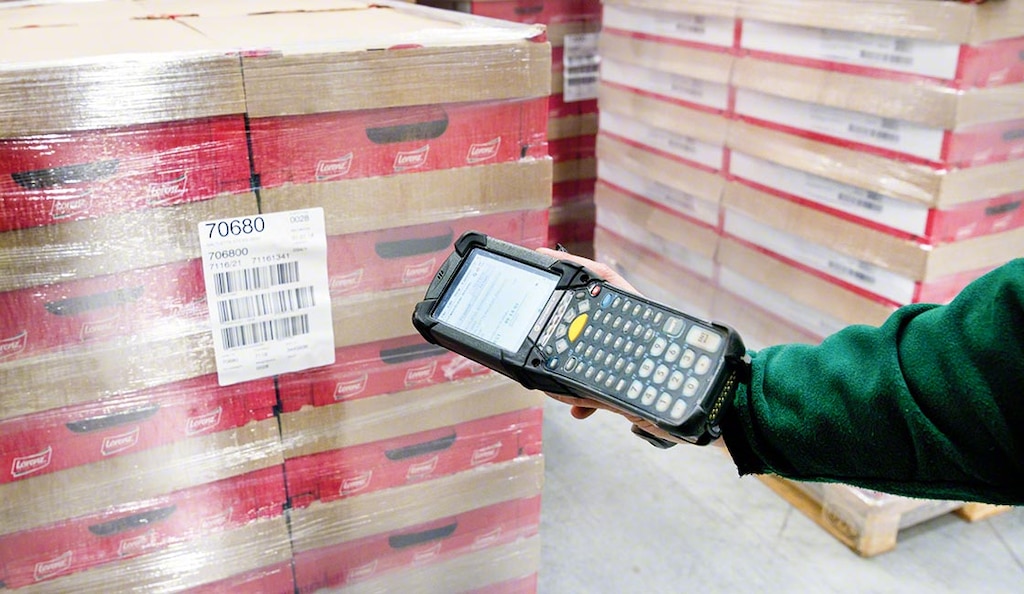
Types of labelling in the warehouse
In logistics facilities, different types of labels are unequivocally associated to each product or element requiring a code to perform operations. These are the most typical types of warehouse labelling:
- Goods coding: this is the most common labelling system in a facility. In the logistics sector, there are many different ways of coding products, such as the GS1-128 barcode. New technologies have given impetus to new methods of product coding, such as QR codes or RF-based smart tags (RFID tags), which streamline the process of identifying and recording goods data.
- Coding of storage systems and locations: coding in logistics includes the labelling of racks, storage locations and other basic areas in the facility. Any item in the warehouse can be labelled to facilitate stock control and operational management. For example, it is common to code racks or storage locations with numerical or alphabetical self-adhesive labels to streamline operations at the facility.
New technologies have made it possible to digitise a large part of the logistics operations in the warehouse. Coordinating processes with advanced warehouse management software facilitates the automatic generation of codes for each item, promoting traceability and real-time stock control.
How does the warehouse labelling process work?
The labelling of fixed elements such as storage systems is usually determined during logistics planning, prior to the commissioning of the warehouse. The logistics manager designs the facility’s layout, distributes the different zones and codes the storage systems to subsequently simplify internal processes.
Item labelling is often performed during goods receipt to aid inventory management and error elimination: when the goods arrive at the loading docks, operators enter the information for each item into the warehouse management system (WMS), which then assigns a unique code for storage and further management. In addition to software that automates the coding of incoming materials, the operation also requires devices such as code readers or label printers to speed up the labelling task.
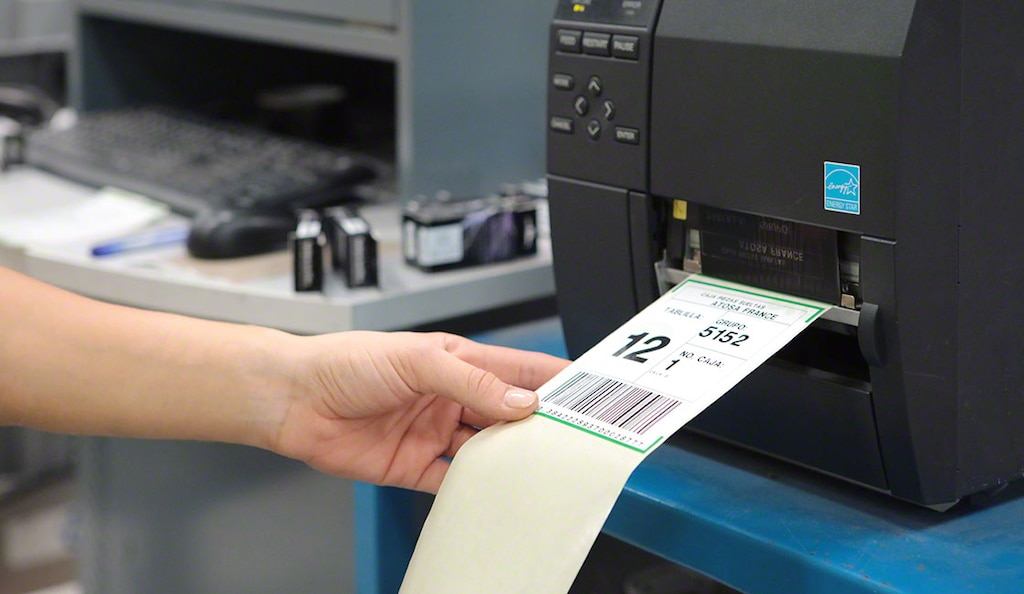
Warehouse labelling software
A WMS generates and prints the product labels that operators place on the corresponding box or pallet. The system also integrates the use of technologies that boost logistics performance: the software connects to RF scanners to automate label reading.
Programs such as Multi Carrier Shipping Software organise the process of packing, labelling and shipping orders, ensuring efficient coding. This module of the Easy WMS warehouse management system automatically generates labels that include, among other information, the tracking number that customers use to track their orders. “Thanks to the Multi Carrier Shipping Software module, we save time in order dispatch. Previously, we had to communicate directly with our transport agencies to print the labels. Now, when we scan each order, the carrier label and delivery note are created automatically. This further reduces the number of errors and helps to better identify the orders to be shipped,” says Anthony Le Fur, Manager at SurDiscount. The French company, which has implemented Easy WMS and the Multi Carrier Shipping Software module, has managed to increase the number of orders prepared at its 2,700 m² warehouse eightfold.
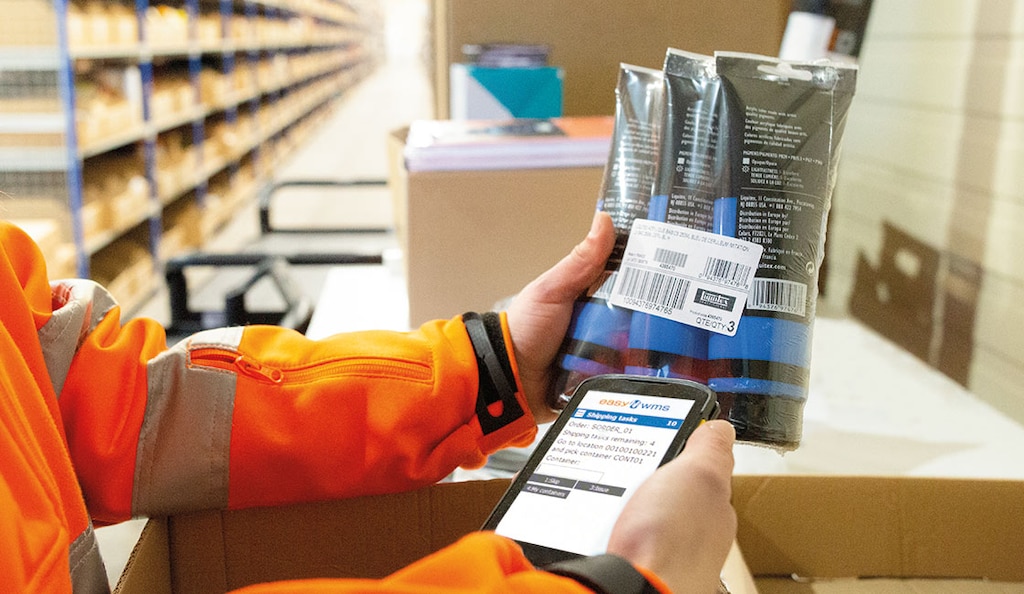
This is also the case of ecommerce company GreenlandMX, which installed the Multi Carrier Shipping Software module to digitise the labelling process and increase its efficiency: “The module makes it possible for us to integrate the entire management of our shipments with the transport agencies and minimise the error rate. As soon as we close an order, Easy WMS generates the labels, the packing list and all the documentation needed by the carrier to distribute the orders,” says Javier Solas, the company’s CEO. Multi Carrier Shipping Software knows in advance which agency will deliver each order, so it prints a customised label for each package, including, among other parameters, the tracking number so that customers can locate the shipment in real time.
Warehouse labelling for effective product traceability
Against a backdrop in which warehouses are processing an increasing number of orders, manual handling of labelling can lead to inefficiencies and errors in tasks such as goods receipt or order picking. Digitising operations with an advanced warehouse management system such as Easy WMS makes it possible to assign a unique code to each product for real-time recording of incoming and outgoing goods.
Easy WMS is warehouse management software designed for companies to have efficient logistics processes. The program maximises logistics performance and facilitates product traceability throughout the supply chain. Interested in finding out how you can benefit from Mecalux software? Don’t hesitate to contact us. One of our expert consultants will work with you to come up with the best digital solution for your warehouse.